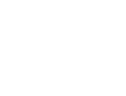
Water Transport Solutions
HMS Alliance, Restoration in Hampshire, UK | 2012
In 1973 she was decommissioned and became a training vessel. In February 1978 she was transferred to the Royal Navy Submarine Museum at Gosport.
Download the full case study
Since then, the submarine was exposed to the sea water. Corrosion to the bow, stern and keel, as well as to the original concrete cradle supports, called for an urgent restoration programme to replace corroded components. Furthermore, Gifford (now Ramboll UK Ltd) designed a scheme to reclaim the land around the submarine to protect it from continued sea water exposure.
Main Contractor Dean & Dyball Civil Engineering (now part of Balfour Beatty Ground Engineering) was appointed to clear the site of existing structures and construct the sheet pile cofferdam which was to be backfilled to afford visitors a new perspective of the vessel.
The steel sheet piles range from AZ 18 to AZ 50 in S 355 GP steel grade, in lengths 14.6 to 19.8 m, and include many special fabricated piles to accommodate the unique cofferdam shape which closely resembled the outline of the submarine. In addition, all sheet piles interlocks were prepared over the full length with ArcelorMittal’s BeltanTM sealant before dispatch to site, and the external façade of each pile was partially coated with a 530 μm nominal dry film thickness Sikacor paint system in the very appropriate Navy Blue colour.
Commercial Marine & Piling were appointed as specialist piling subcontractor and they utilised a PVE 2316 High Frequency Variable Moment vibrodriver, initially with special clamp to extract the existing timber piles, then to install and partially drive the sheet piles. From land a Zeppelin 17 m rig with leader mounted vibrodriver was used to pitch and drive the piles. Over water a crane on a floating pontoon used the PVE vibrodriver. There were concerns that installation vibration may cause settlement in the concrete support cradles and so the hydraulic press ZU 100 Stillworker from Watson & Hillhouse was employed to silently and with negligible vibration, drive the sheet piles within 5 m radius of the cradles.
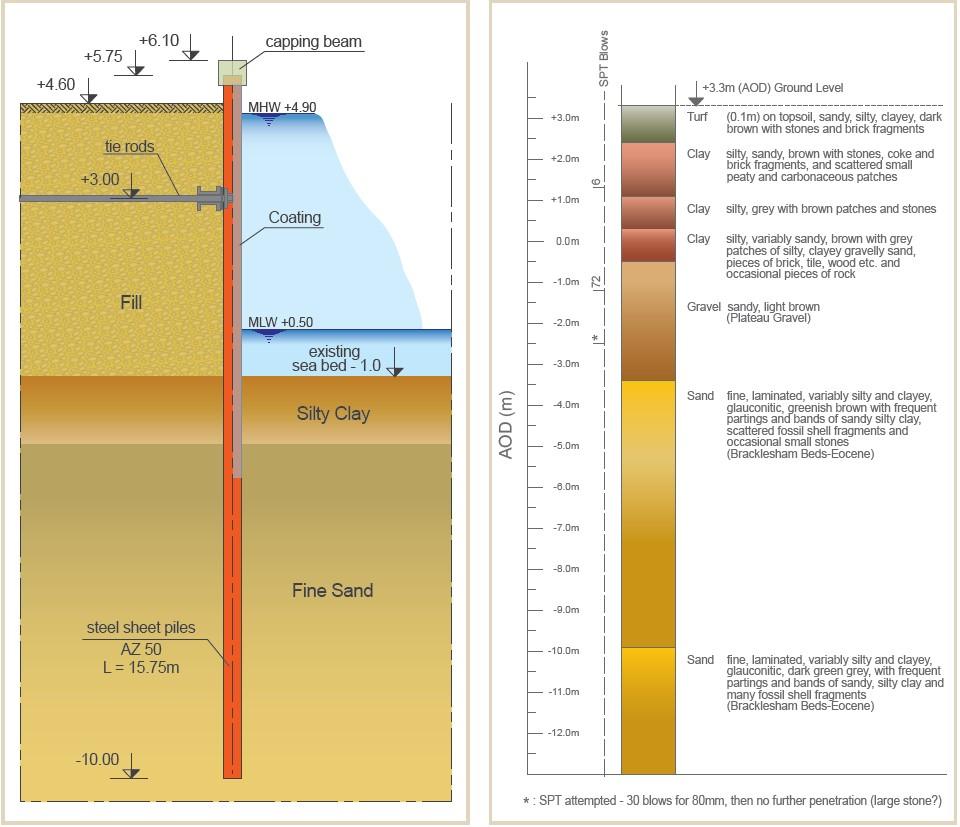
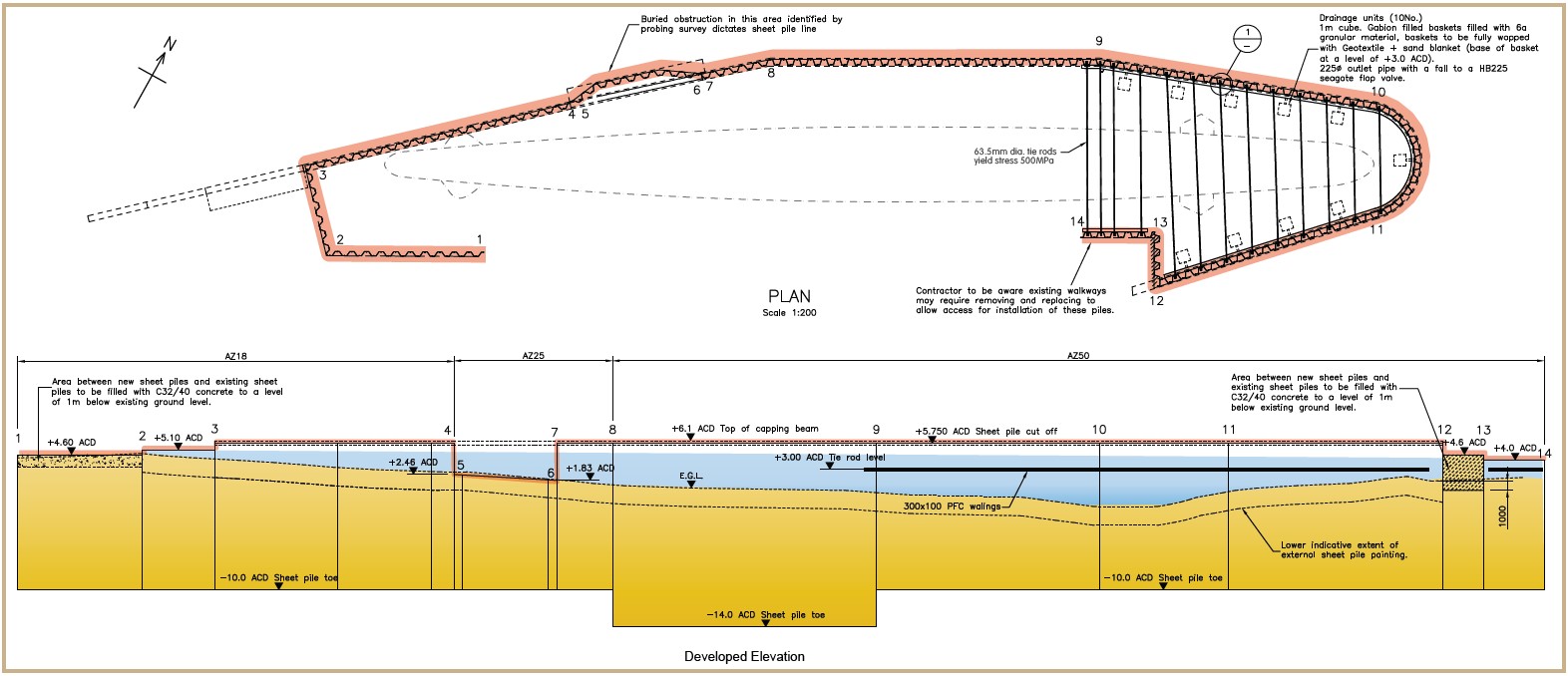
Logistics to deliver the piles to site were very complex, with four points of delivery and numerous water and landside stakeholders to accommodate including Ministry of Defense and a Sail Training School. Most of the piles were trans-shipped in Portsmouth Docks and barged across to the site as required.
The complex shape of the cofferdam dictated a large number of special piles, in conjunction with the numerous sections and lengths of painted and sealed piles to be delivered in the correct order to the multi user water frontage with very tight land side working space, all conspired to make a highly challenging project which was completed professionally and successfully.