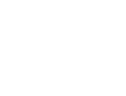
Water Transport Solutions
PAENAL fabrication yard, Porto Amboim, Angola | 2007
The PAENAL fabrication yard is located on the Enseada de Benguela Velha beach site located in the Kwanza Sul province, on the Atlantic shoreline of Angola. The site is approximately 3 km south of Porto Amboim, around 220 km south of Luanda.
Download the full case study
This new yard is being developed in three distinct phases. Each phase will increase the capacity of the yard, which will comprise at the end a 460 m long quay wall and a 630 m breakwater for berthing of Sonangol product tankers in replacement of the offloading CBM terminal presently located at the selected site. It will also add a dry dock for repair and overhaul of construction vessels, supply boats and small coastal tankers up to 150 m in length. The total area will be approximately 120 000 m2. It will be self-sufficient in terms of power, water and sewerage. The project provides a significant stimulus for the local economy by tapping into the resources of small and medium-size companies in the region.
Quay 1 & 2 is 460 m long, and is formed by a steel sheet pile wall with the top level at elevation+4.0 m (LAT). At one end, the perpendicular return wall is 30 m long. A reinforced concrete capping beam constitutes the superstructure, where the equipments, such as mooring bollards, stairs and fenders are installed. The main sheet pile wall is fixed with tie-rods to a sheet pile anchor wall. The design of the sheet pile structure was relatively complex and took into account several surcharge load combinations, and different wave load cases. The engineering department of AM CRPS worked closely with the contractor in order to optimize the final solution.
To speed up installation, a dyke in quarry run was erected with a crest level at +3.0 m (LAT). The edge of this working platform was at a distance of about 11.0 m from the alignment of the main sheet pile wall. This working sequence allowed using terrestrial means for the pile driving, which is faster than working from water, and additionally, it reduces construction time as the quay core was executed in parallel to the driving. This installation method contributes to better results, especially in quality.
Driving of the anchor wall, an AZ 20-700 in 9.0 m length, started simultaneously to the backfilling operation. A simple template was used to guide the sheet piles during driving. Driving of the piles started with a vibratory hammer ICE 815C and to reach final depth, a hydraulic impact hammer IHC S70 was used.
The installation of the main quay wall made of 21.0 m long AZ 50 began after the pile driving of the anchor was completed. A new and stiffer template was utilized to install the AZ 50, the strongest hot rolled steel sheet pile in the world. The main wall is connected by tie rods to the anchor wall, which is located at 29.5 m behind.
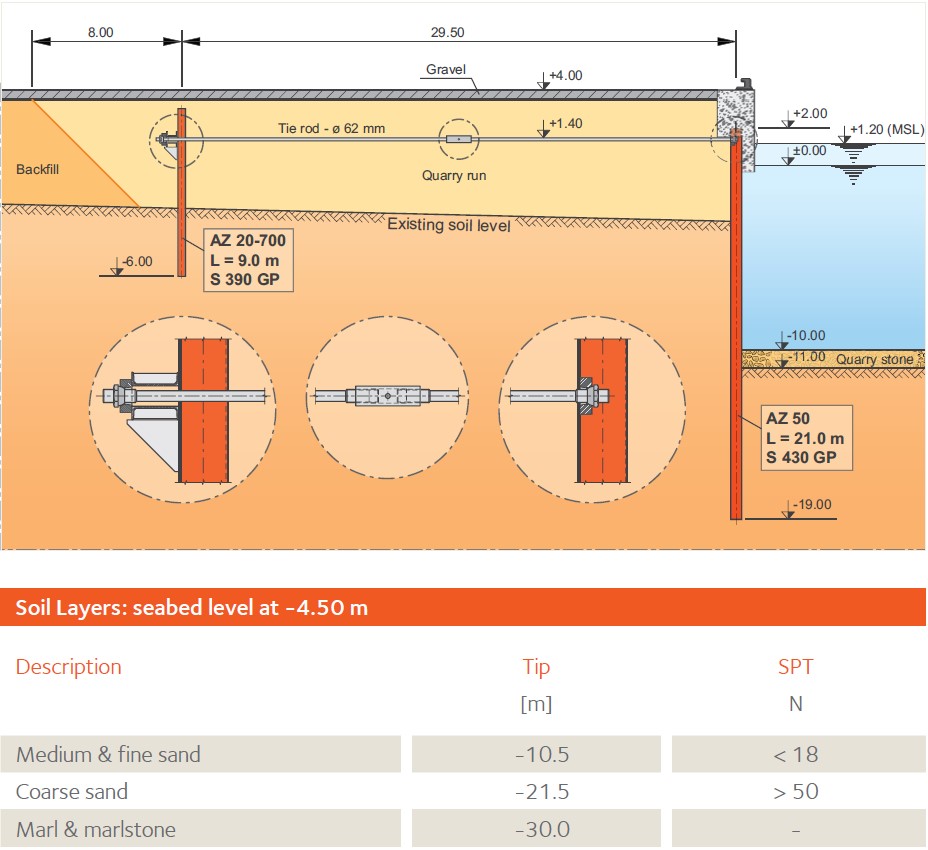
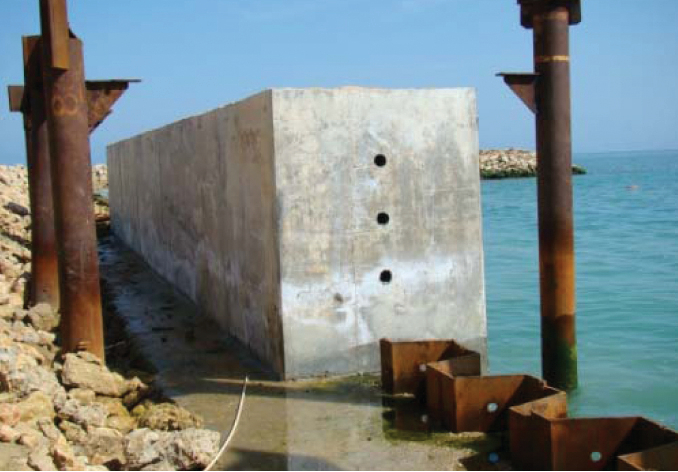
The final embedment of the main sheet piles is 8.0 m. The driving took place in 10.0 m long panels, which corresponds to the length of the guiding template. Five CAZ 50 box piles were incorporated in the main quay wall to support additional high vertical loads from a heavy lift crane.
Once the pile driving was finished, the working platform was excavated to elevation +1.30 m (LAT), which is the elevation required for the installation of the tie rods. Every pair of AZ 50 was supported by a tie rod with 62 mm diameter and upset ends of M72, respectively M80, at a distance between centerline of tie rods of 1.16 m. After the installation of the tie rods, backfilling to final elevation took place concurrently to the execution of the concrete capping beam. The large capping beam stiffens the sheet pile wall at the top, and transmits the loads from fenders and bollards to the sheet pile wall.
The dredging went down to -11.0 m and a quarry stone protection layer of 1.0 m thickness was installed at the bottom of the seabed level, up to elevation -10.0 m.
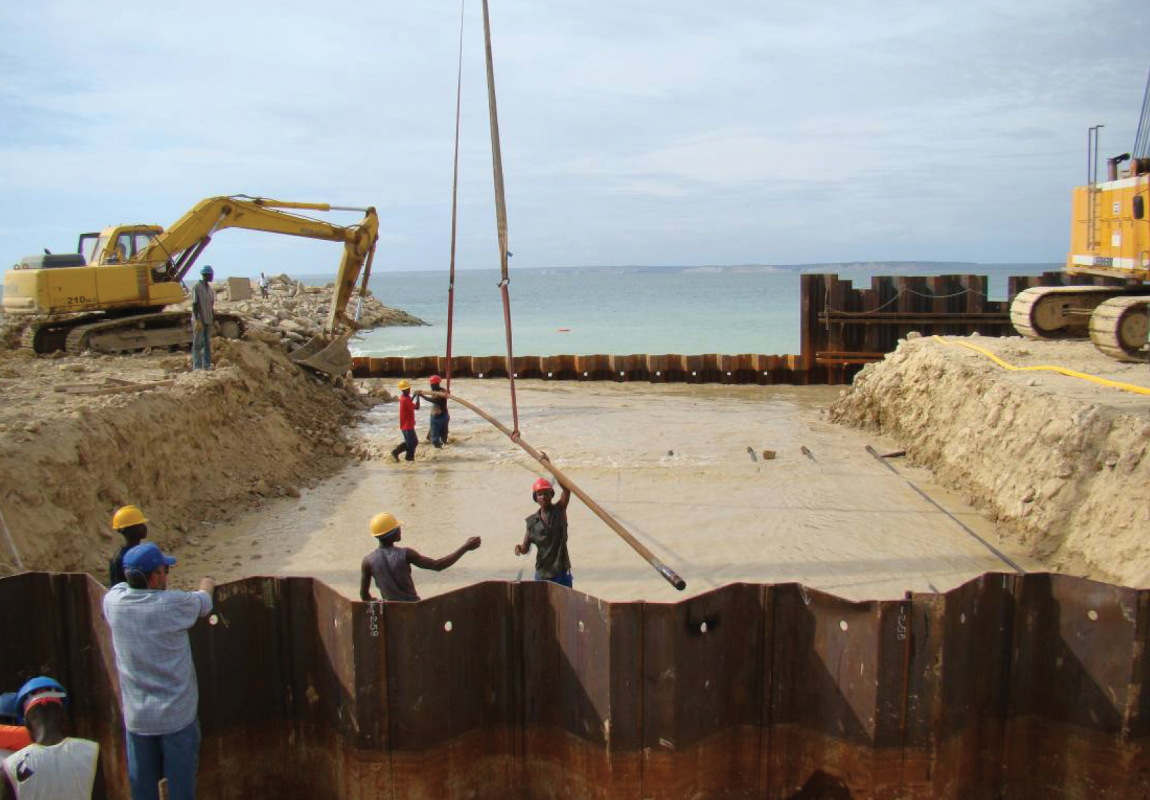
Despite high corrosion rates assumed by the design engineer, the anchor wall does not have any complementary protection against corrosion. The design considered a loss of steel during the 50 years’ design life (sacrificial thickness). Due to higher corrosion rates on the water side, the main sheet pile wall is treated differently: a concrete capping beam down to +0.0 m (LAT), in combination with cathodic protection. Furthermore, sacrificial thickness was considered for the period above 25 years, which is the service life that was assumed for the sacrificial anodes.
The main contractor, Conduril, started the works in 2007 and plans to conclude them in 2010.