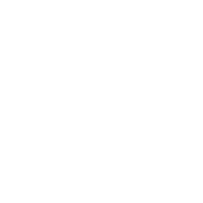
Temporary Applications
Temporary works
798 tonnes of sheet piles
New BVK headquarters in Munich, DE | 2023
Download the full case study
A total of 188,300 m3 of soil will be excavated and disposed of. Temporary sheet piling was used to shore the excavation pit on the south and east sides of the construction site. The contractor chose ArcelorMittal’s PU sheet piles, which have a very low CO2 footprint thanks to their scrap-based production and, in this case, the use of renewable electricity in their manufacture.
The overall project aims to achieve a high level of sustainability and has already been awarded the “Sustainable Building Site” certificate by the German Sustainable Building Council (DGNB).
Execution
The excavation pit is a project with the classic challenges of a city centre location: residential and commercial buildings in the immediate vicinity, special requirements for dust and noise emissions and challenging logistics. As the tunnel for the U4 underground railway line runs directly alongside the excavation pit, any vibrations or deformations are recorded using a monitoring system. Before the sheet pile wall was installed, the sheet pile wall axis was first surveyed for explosive ordnance. The first special civil engineering works began in January 2023 and the first PU 28 sheet piles for the shoring system were then delivered in March. The sheet piles are rented out by ArcelorMittal and returned to the rental stock after temporary use in the excavation pit. The sheet piles are then processed at the stockyard and later used for other projects.
The installed sheet piles have a length of 15.20 - 22.20 m and were installed using an ABI TM 22 (vibration method). This resulted in a total tonnage of 798 tonnes, which led to a considerable sheet pile wall installation area of 4,850 m2. From March to May 2023, the sheet pile walls were installed and the first tie-rod and wailing works were carried out. To loosen the soil, the first step was to pre-drill in the area of the sheet pile interlocks using an auger. Jetting-assisted driving was used in some areas. The injected water loosens the soil and removes loosened material. This reduces the peak resistance at the toe and, depending on the soil structure, also reduces skin friction and interlock friction due to water flowing down or rising up. In addition, soil replacement was done in advance along the drain where the existing soil was replaced with 8/32-grain gravel.
This should subsequently ensure that the sheet pile wall in that area can be retrieved without any problems and that groundwater can flow around it. The subsoil consists of Quaternary gravel, with the sheet pile wall penetrating into the Tertiary. As the excavation and excavation work progresses bracing and anchoring layers of the sheet pile wall are installed after the dewatering work. In its final state, the sheet pile wall is partially back-anchored in up to 3 layers. The anchor length is equally impressive at up to 60 metres.
As this is a temporary shoring, the sheet pile wall will be removed after the construction of the basement slabs of the future BVK headquarters. Prior to removal, the tie-rods must be released and the anchor heads removed at the appropriate time.
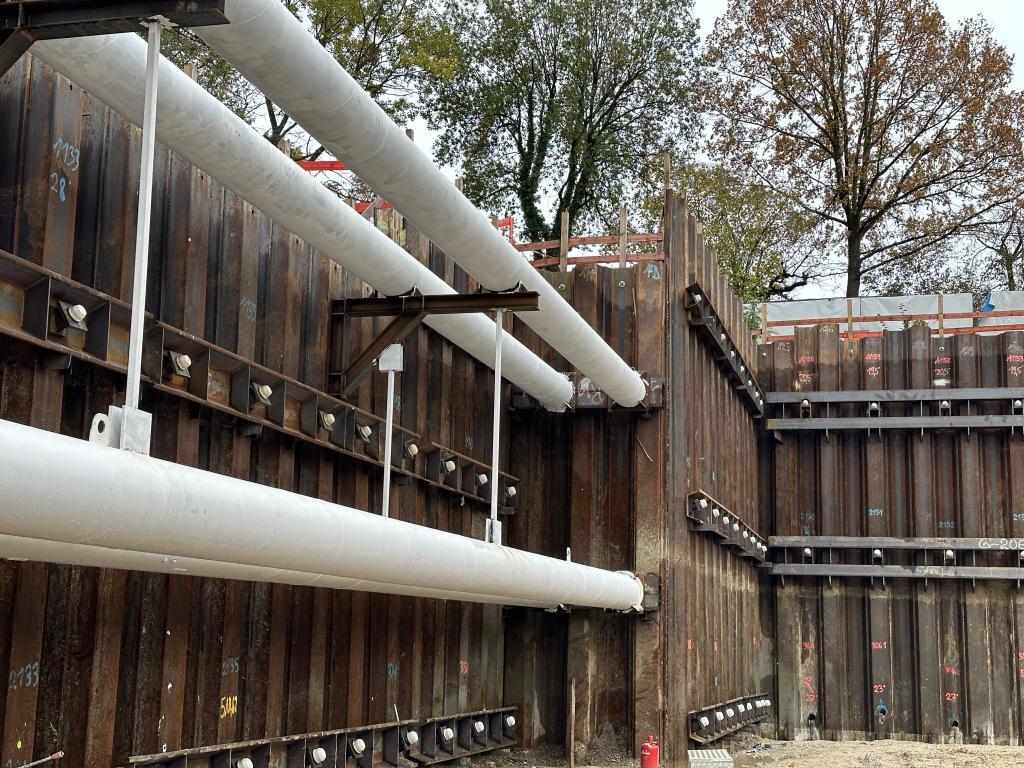
Sustainable excavation pit
The RS76 excavation pit was awarded the DGNB system for sustainable construction sites. As the “Special foundation engineering” system was not yet available from the German Sustainable Building Council at the time, certification was carried out according to the similar catalogue of criteria for building construction. In addition to initiatives such as extensive noise protection, the continued use of demolition material and tree protection, sheet piling is a key component of the excavation pit’s sustainability concept.
First of all, the sheet piles are only rented and are therefore transferred back to ArcelorMittal’s rental stock after use. Temporarily used sheet piles are typically used between 5-10 times before being fully recycled at the end of their life cycle. The sheet piles used on site are from the EcoSheetPile™ Plus (XCarb®) range. These sheet piles are manufactured in Luxembourg using 100 % recycled scrap and 100 % electricity from renewable sources. In the 4th quarter of 2022, ArcelorMittal Träger und Spundwand GmbH began systematically converting all its sheet piling rental stock to EcoSheetPile™ Plus. The use of EcoSheetPile™ Plus sheet piles on the RS76 construction site saved around 1,652 tonnes of CO2 equivalents (CO2e) in the production of the steel (modules A1-A3).
This corresponds to a reduction of 85 % compared to conventionally produced sheet piles.
Repeated use in subsequent construction projects has a further positive impact, as this avoids the production of new steel, thus saving natural resources and energy (Module D). The Global Warming Potential for the entire life cycle of the sheet piles is shown below, with the modules broken down according to the EN 15804 and ISO 14025 standards. For the end-of-life scenario (Module D), a conservative assumption is made that the sheet piles will be used 5 times. The calculations are based on published Environmental Product Declarations from ArcelorMittal.
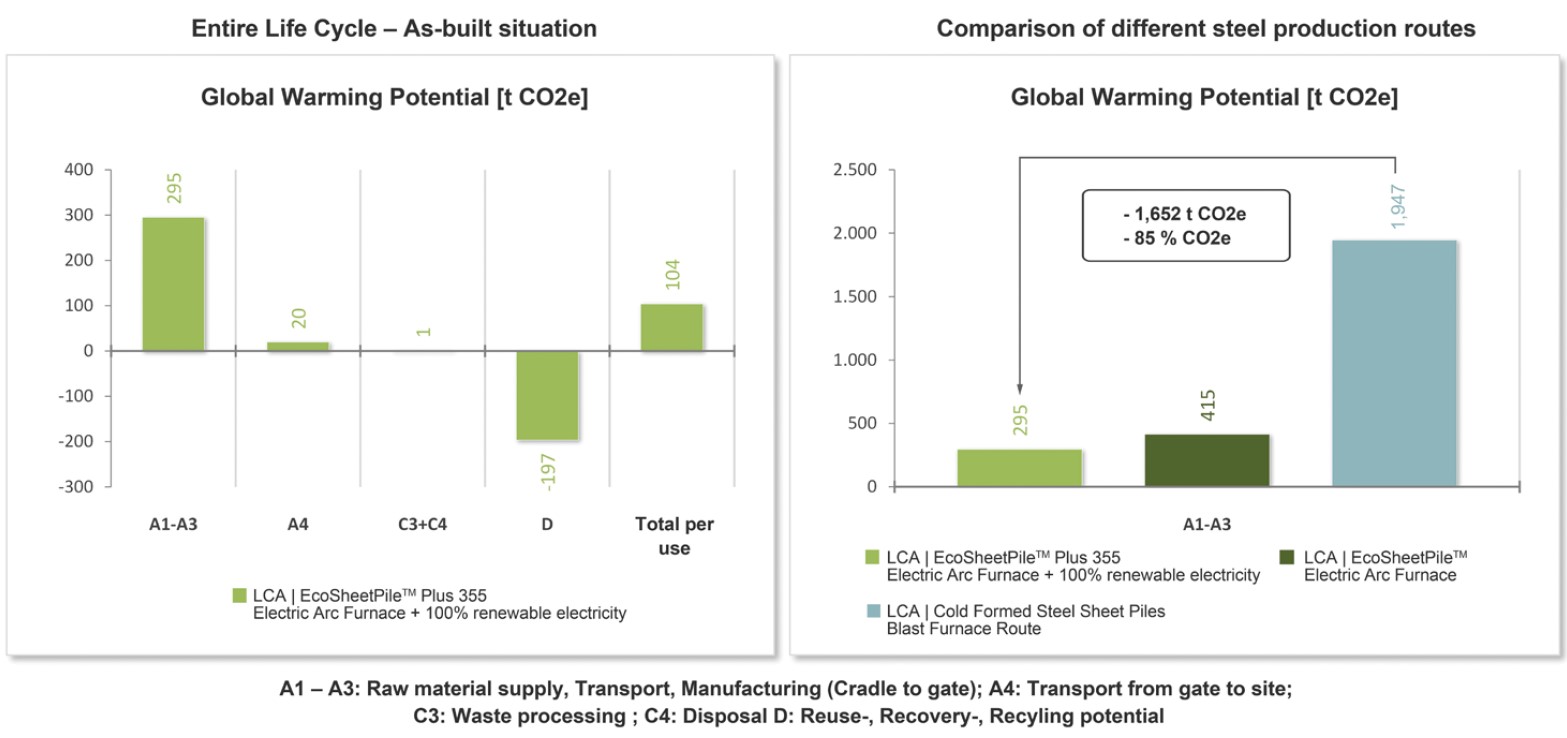