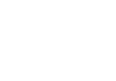
Hazard Protection Solutions
Dyke reinforcement, Saint-Laurent-du-Var, FR | 2016
Download the full case study
The work concerns nearly 2,000 inhabitants, an industrial park, sports and cultural infrastructures and the town centre. The reinforcement of the Saint-Laurent-du-Var dyke is part of the complementary embankment system on both banks. On the left bank, the raising of the dyke of the A8 motorway under the supervision of ESCOTA (motorway manager) and the reinforcement of the MINCADAM dyke under the supervision of CD06, were completed in 2010.
The works to reinforce the dyke materialized by the metropolitan road number 95 are 1.6 km long. Reinforcement is carried out by means of a double sheet pile wall for the bank sectors with sufficient space: AZ 23-800 from 12.7 m to 14.5 m in the main wall and AZ 18-800 from 2.5 m to 7.5 m in the anchor wall, in steel grade S 355 GP, for a total of 2,315 tonnes. The distance between the two walls is 12 m, the tie rods are installed every 1.6 m (at centreline).
The reinforcement extends from the parking lot of the Jean Aicard roundabout, at the upstream limit, to the Pierre de Coubertin roundabout, at the downstream limit, and must guarantee the stability of the protective structures against the hazards of failure (external erosion, internal erosion, overflow and overall instability) for an exceptional flood Q = 5,000 m3/s.
The riverbank reinforcement started in July 2016. It also included the installation of riprap and gabion mattress protection, the redesign of the outlets of the stormwater structures and landscaping, creating a vegetized area all along the dyke.
The two sheet pile walls were built in different ways with two dedicated driving crews. The main wall was installed using the panel driving method. The first pile-driving equipment consisted of a free-hanging PTC 32HFV vibratory hammer equipped with a 2 × 55t Duplex double clamp, an ICE 28 RF hydraulic vibrator with a single clamp 200TU, as well as a Delmag D 19-52 diesel hammer with adapted driving cap provided by ArcelorMittal. The anchor wall was installed with the pitch-and-drive method using a Movax SPH80 hydraulic vibratory hammer mounted on a 27 tonne excavator. The second driving equipment consisted of a vibratory hammer PTC 23HFV and a Delmag D 30 diesel hammer for driving the main wall, and a Dawson hydraulic vibratory hammer mounted on an excavator for the installation of the anchor wall.
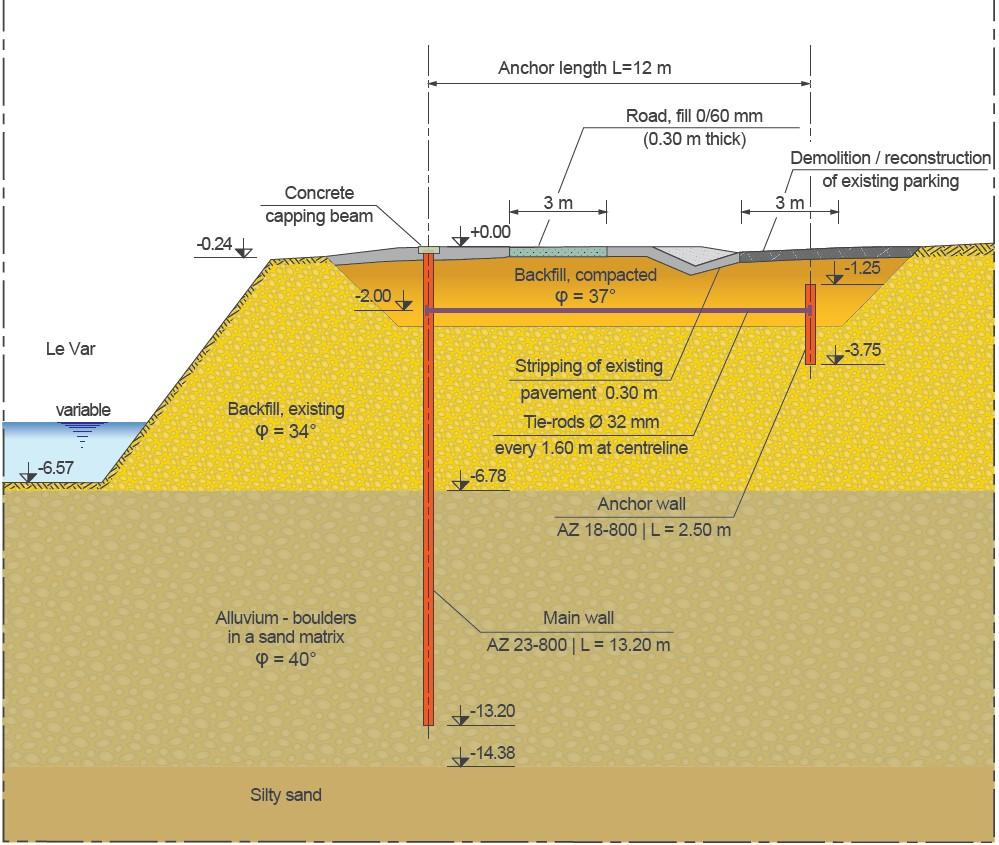
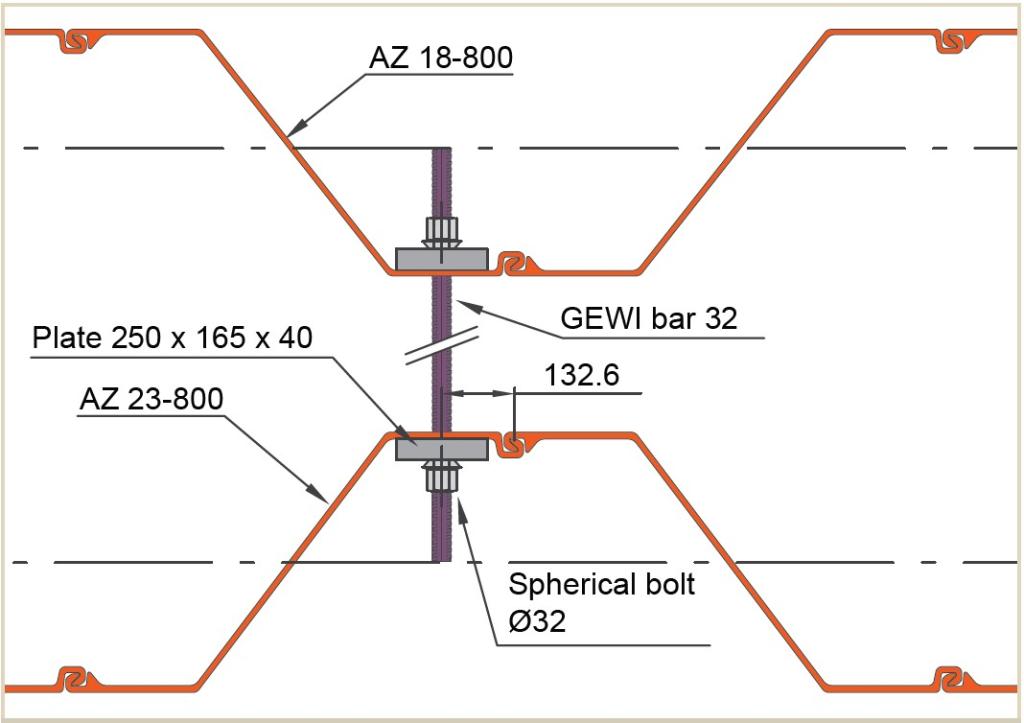
Vibration monitoring was carried out throughout the entire sheet pile installation process.
Pressuremeter tests showed a layer of backfill with low to medium mechanical properties followed by a layer of alluvium with gravel and pebbles in a sandy matrix. The limit pressures P, for this layer were above 3 MPa and exceeded 5 MPa in some elevations.
The project was tendered with AZ 24-700 profiles, but the contractor proposed to perform driving tests with AZ 20-800-0.5, AZ 23-800 and AZ 25-800 sheet piles to confirm the good behaviour of the newly developed AZ®-800 range in compact soils. The driving tests were carried out in June 2016. Savings of around 14% were achieved by replacing the planned AZ 24-700 with the AZ 23-800, an equivalent but much lighter profile.
Another specific feature of the site was the installation of an eccentric anchor made of GEWI bars with a diameter of 32 mm. The design is based on a method developed by ArcelorMittal in collaboration with the Institute of Steel Construction of the Civil Engineering Department of the Aachen Polytechnic University (RWTH) in Germany. Work began in 2016 and was completed in 2017.
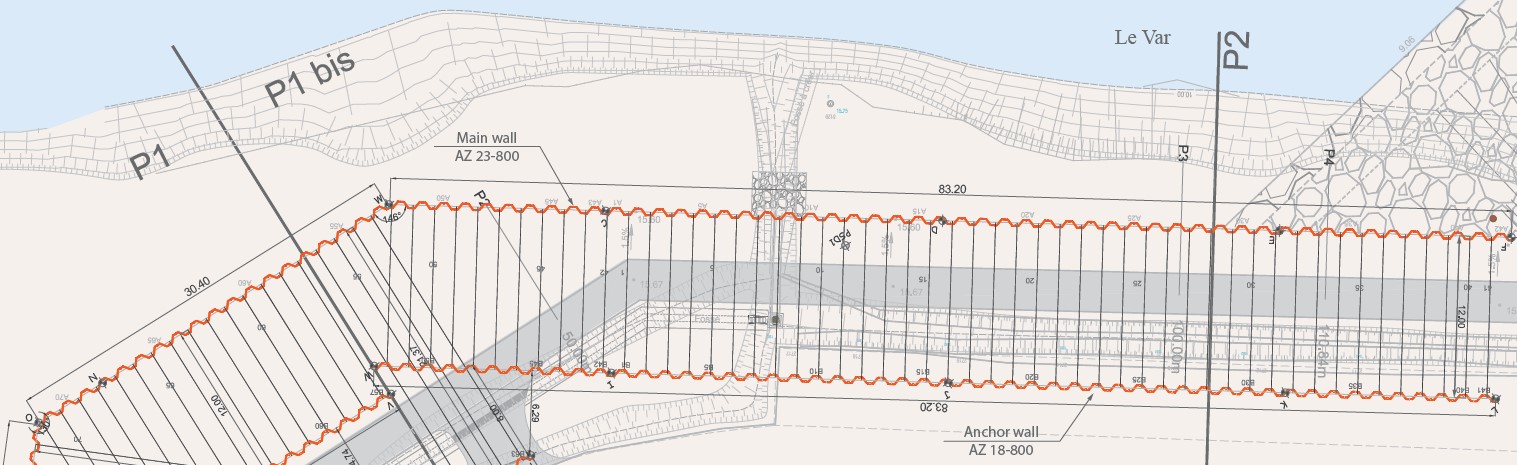