F.A.Q.
Frequently Asked Questions
Sustainability
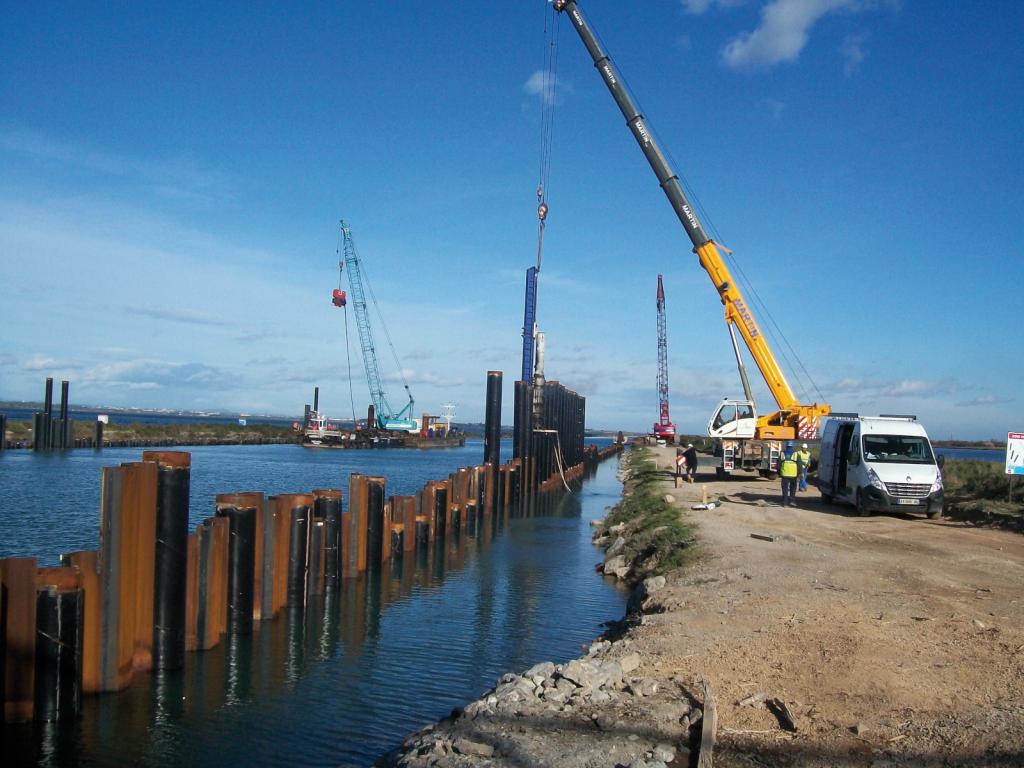
Depending on soil conditions and type of application, steel sheet piles can be re-used several times: generally speaking, they can be driven 5 to 10 times before being scraped. In case of damage to the head or the tip due to installation, affected parts can be simply cut off, and the rest of the pile can be re-used.
Notes
- when re-using sheet piles on the same project, we recommend to order slightly longer piles than required to take into account damage to the head or tip. Alternatively, for large projects, ordering a few spare piles allows for splicing of damaged piles,
- re-using reduces significantly the environmental impact of the steel sheet piles.
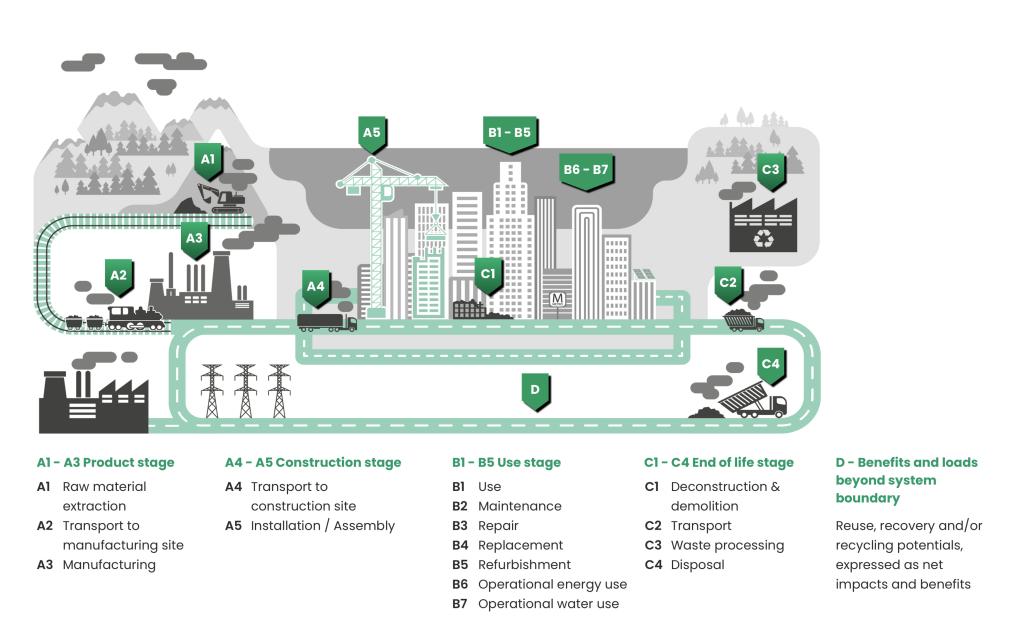
A Life Cycle Assessment (LCA) is a systematic analysis and evaluation of the environmental impacts of a product (or service) for its entire life cycle. The life cycle of a product in the construction industry includes the extraction of raw materials and their further processing, transport, manufacture, all further processing steps before installation at the construction site, the use phase, disassembly and finally the reuse or recycling of the product. These stages can be grouped in so-called ‘modules’ in order to standardize the life cycle of different products. The relevant standards for establishing a LCA are ISO 14040 and ISO 14044.
For every stage of the life cycle of a product, environmental impacts, resource consumption as well as waste flows are quantified.
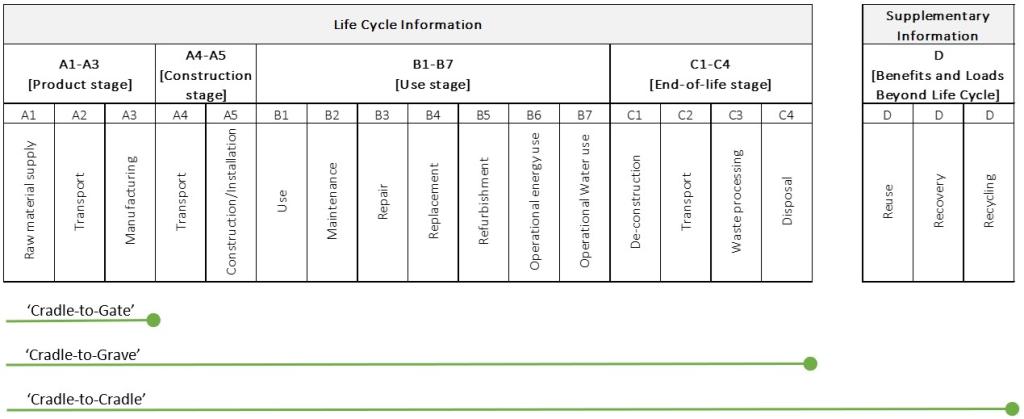
An Environmental Product Declaration (EPD) is a document that describes the environmental impacts of a product based on a life cycle assessment with quantitative data, from the moment the raw materials are extracted to the end of its useful life. EPDs are based on Product Category Rules called PCRs, which serve as a technical standard and define f.ex. the modules that need to be considered. For construction products, EN 15804 serves as core PCR. Wire solutions generally refer to the same PCR. An EPD is owned by the manufacturer and depicts the impacts for the finished product. The document is valid for 5 years, after being published and enables manufacturers to transparently communicate the environmental impacts of products. EPDs in turn form the basis for the ecological assessment of buildings and other construction projects.
ArcelorMittal Sheet Piling has published several EPDs that are verified by independent experts and published at different program operators (f.ex. EPD International, INIES, MRPI,..). A program operator (or publisher) is a national organization, that publishes EPDs under their name and specific rules. There are multiple program operators, and they all need to comply with the same standards (to a large extend). Have a look at our EPD EcoSheetPile™ Plus.
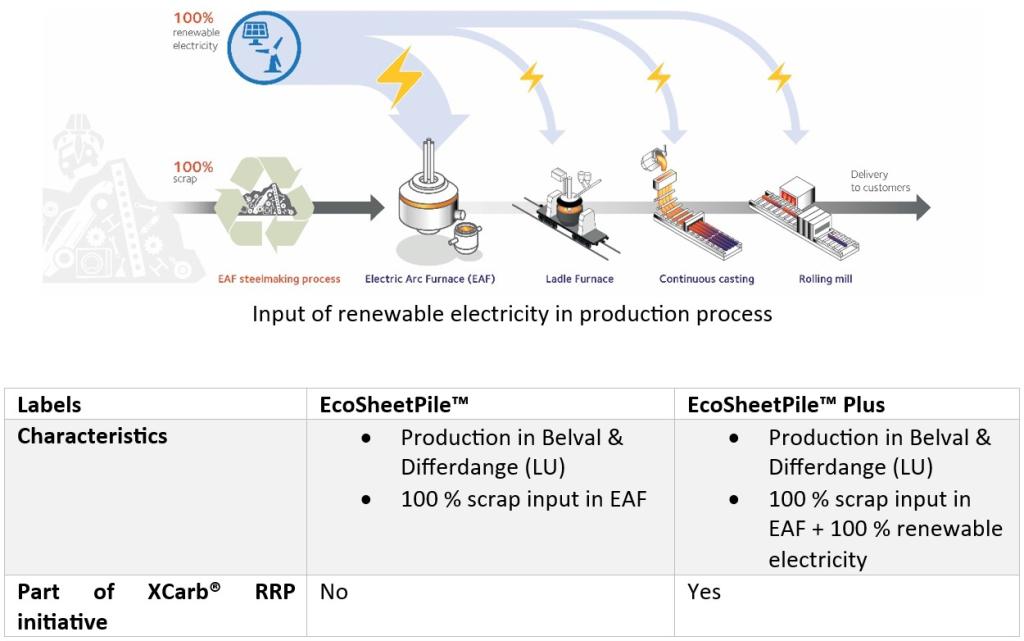
XCarb® is the brand name for ArcelorMittal’s ongoing global program of steelmaking innovation targeted at carbon-neutral steel by 2050. The initiatives that are part of XCarb® aim to reduce the carbon footprint of ArcelorMittal and of its customers. XCarb® Recycled and Renewably Produced applies to products made via the Electric Arc Furnace route using up to 100% steel scrap and 100% renewable energy from solar or wind sources. Their environmental impact is also quantified by specific EPDs. By using higher than average steel scrap and renewable energy, XCarb® Recycled and Renewably Produced products have a lower than global average CO2 footprint per tonne of finished steel. The electricity used in the steelmaking process is independently verified, with a ‘Guarantee of Origin’ certifying that it is from renewable sources. This is ensured by purchasing of ‘Renewable Energy Certificates’ (RECs), a market-based offering that certifies the bearer owns a specific amount (in megawatt-hours) of electricity generated from a renewable energy resource. EcoSheetPile™ Plus is part of ArcelorMittal’s XCarb® Recycled and Renewably Produced initiative and is produced with 100% scrap input and 100% renewable electricity.
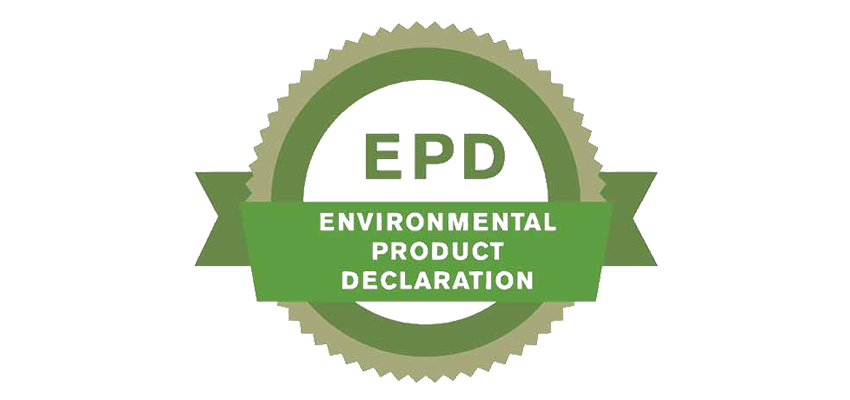
An EPD should always be analyzed in detail. However, you should not forget to check:
- Owner of the Declaration: Which manufacturer is it?
- Program operator/Publisher: IBU, INIES, EPD International etc.
- Issue date and validity of the EPD
- Declared unit: 1 tonne or 1 kg of the product? Metric or imperial?
- Product description: Is the product in question explicitly named in the product description?
- Implemented End-of-Life scenario
Indicators that should be checked in any case:
- Global Warming Potential
- Renewable primary energy as energy carrier
- Non-renewable primary energy as energy carrier
- Use of secondary material
The Global Warming Potential (GWP) indicator is for sure the most important one to check and the most commonly used, due to the importance for the climate change and public focus. GWP is measured in CO2-equivalents (CO2e), hence CO2 is the reference gas. The CO2e provides a common scale for measuring the climate effects of different greenhouse gases (carbon dioxide, methane, nitrous oxide a.o.).
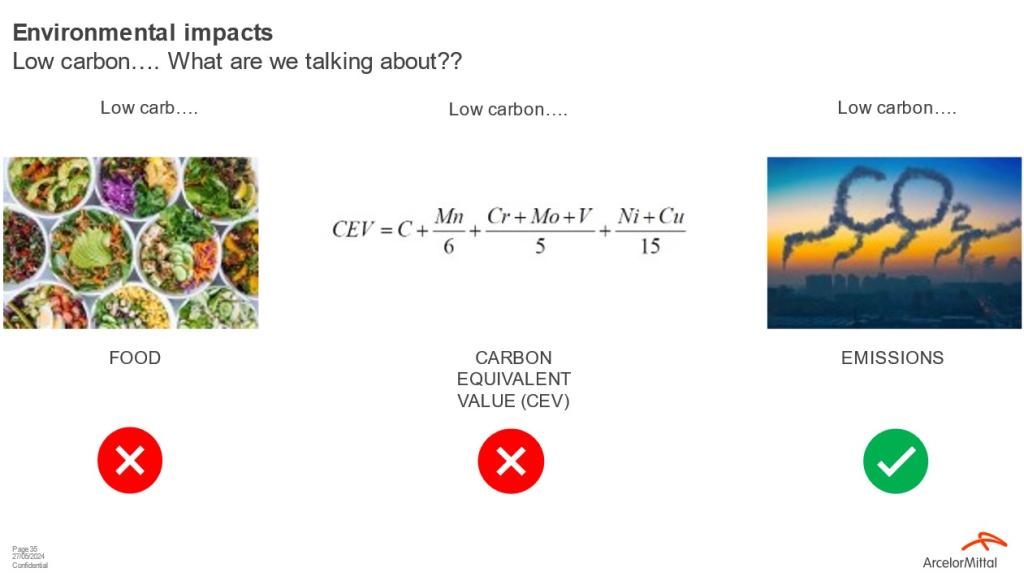
Low carbon emissions steel is not related to a low carbon content in the chemical composition of steel, namely the carbon equivalent value CEV. This means that the production of low carbon emissions steel, such as that from our XCarb®/ EcoSheetPile™ Plus range, has no impact on welding properties.
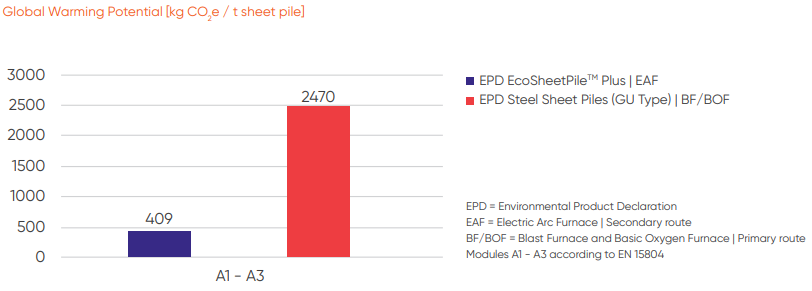
Yes. Steel can be produced via the primary route (blast furnace and converter) or via the secondary route (electric arc furnace). Scrap-based production via the secondary route is far more environmentally friendly as no iron ore or coal is used, and only steel scrap is melted down and reprocessed in the electric arc furnace. This is closed-loop recycling. Scrap-based steel production thus conserves natural resources while emitting significantly less greenhouse gases. If we focus on the production stage of steel (Modules A1-A3 according to EN 15804), the scrap‑based production emits 5-7 times less CO2e emissions than a conventional blast furnace route based on iron ore and coke.
In below graph, you can find average emissions of CO2 emissions per tonne of crude steel. Emissions do not take into account rolling or finishing works, so the values that can be found in EPDs, are generally higher.
Note:
CO2 emissions per tonne of finished steel. Vast majority of GHG emissions in steel production are CO2 emissions.
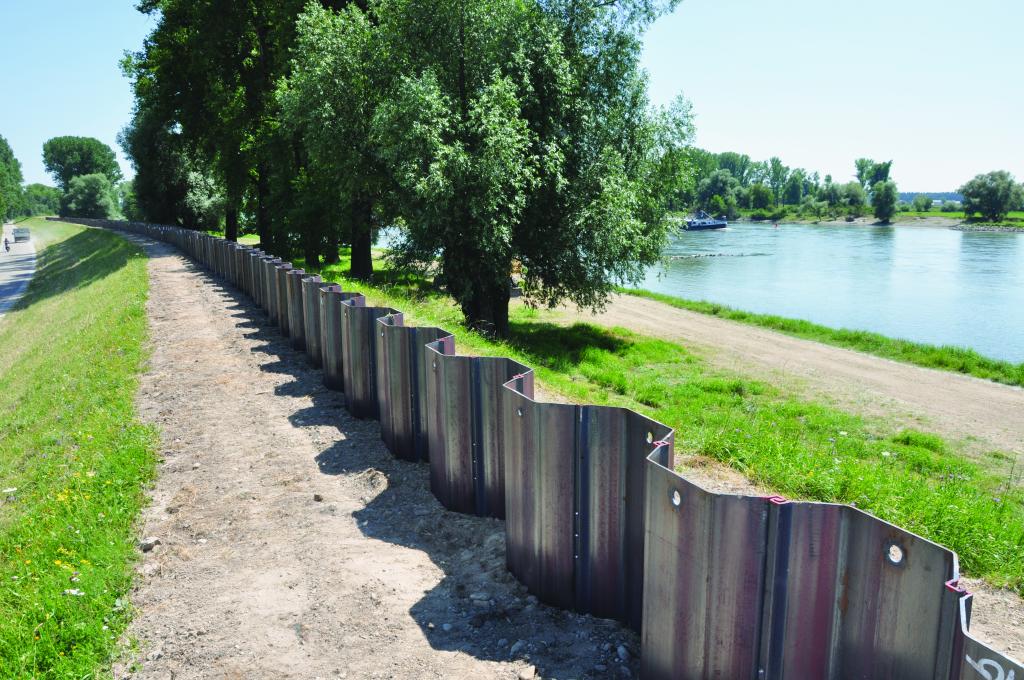
The Global Warming Potential (GWP) is measured in carbon-equivalents (CO2e). Carbon dioxide, Methane, Nitrous oxide and other greenhouse gases contribute to the Global Warming Potential.
The GWP is a measure used to assess the relative potency of various greenhouse gases, taking into account how long they remain active in the atmosphere. CO2 is the reference gas.
Due to climate change and related impacts, industry is in public focus. The steel industry contributes to 7-9 % of global CO2 emissions. ArcelorMittal knows about this responsibility and has set ambitious goals to decarbonize its production activities. Hence, the quantification of greenhouse gas emissions plays a crucial role on site but also product level.
Our Environmental Product Declarations (EPDs) reference several environmental indicators according to EN 15804+A2, such as the GWP. These documents depict the environmental impacts from the production stage (Modules A1-A3) and other life cycle stages of the product. Have a look at our recently published EPD EcoSheetPile™ Plus.
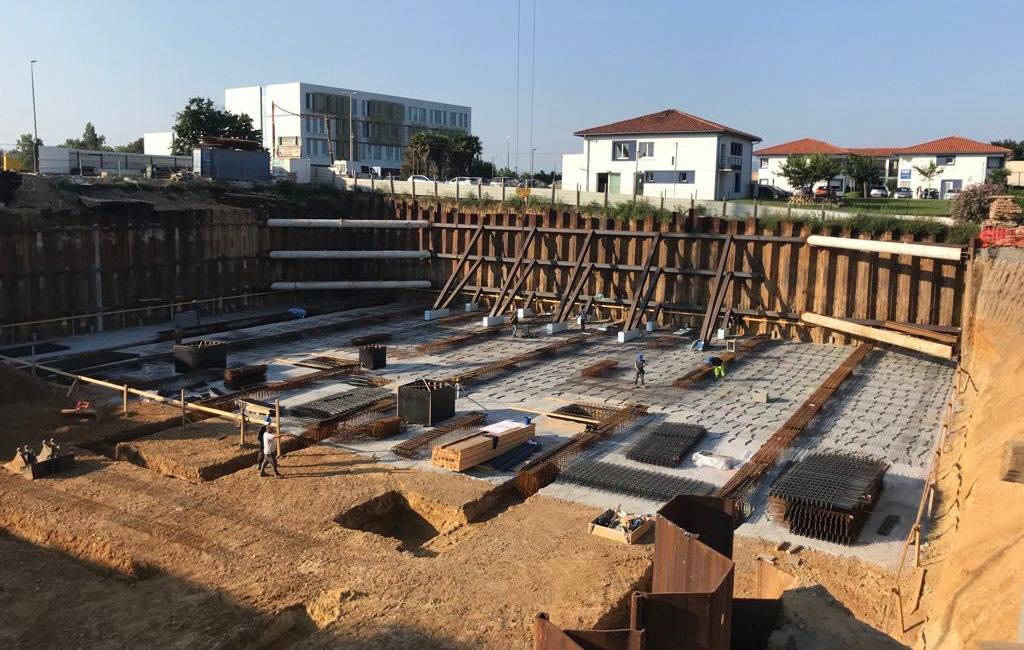
There are several ways to incentivize contractors to bid with sustainable alternatives. Some of them are:
- Set minimum threshold for recycled content in steel;
- Set maximum threshold for GWP of steel in production phase;
- CO2 shadow pricing;
- Monetization method (holistic approach considering multiple environmental impacts).
Environmental requirements in tenders should always require product specific EPDs elaborated according to EN 15804+A2 and ISO 14025 standards.
If you want to know more about the monetization method you can contact us.
Technical aspects
Question
For underground car parks (UCPs) below the groundwater level, do we need to drive the steel sheet piles down to an impervious layer (clay) to avoid problems with buoyancy and/or watertight connections between the sheet piles and the bottom slab?
Answer
Steel sheetpile wall does not always need to be driven down to an impervious clay layer. It depends on the soil and groundwater flow conditions. If the soil is too pervious, and the contractor cannot cope with the water ingress suing a standard pumping system, then a thick concrete bottom slab poured under water can be an alternative (cf. brochure 'Underground car parks - Guide book - NL - 2018'). In that case, in the final stage, one may have to anchor the bottom slab against buoyancy (Archimède) using vertical anchors / micropiles.
For the horizontal water seapage through the interlocks, seal welding of the interlocks can be done after excavation (without any sealing system inside the interlocks before installation). Seal-welding is quite expensive, so in some UCPs, the owner decided to accept a little bit of water passing through the interlocks. However, water flow through the interlocks should be prevented if the sheet pile wall is coated on its visible face for aesthetical reasons.
Basic details of a connection ssp / bottom slab are shown in our ‘Impervious steel sheet pile wall brochure’, on page 43. In general, a horizontal membrane is fixed to a horizontal steel plate that is welded onto the sheet piles. Alternatively, an expansive joint fixed on the sheet pile backed up with a special injection hose can be as effective (and cheaper). Small cracks in the slab can be filled with the injected grout (if necessary afterwards), and the expansion of the joint should be sufficient to fill any small gaps between the sheet piles and the slab. Studs fixed to the sheet pile wall can replace the welding of rebars to the sheet piles.
Design software
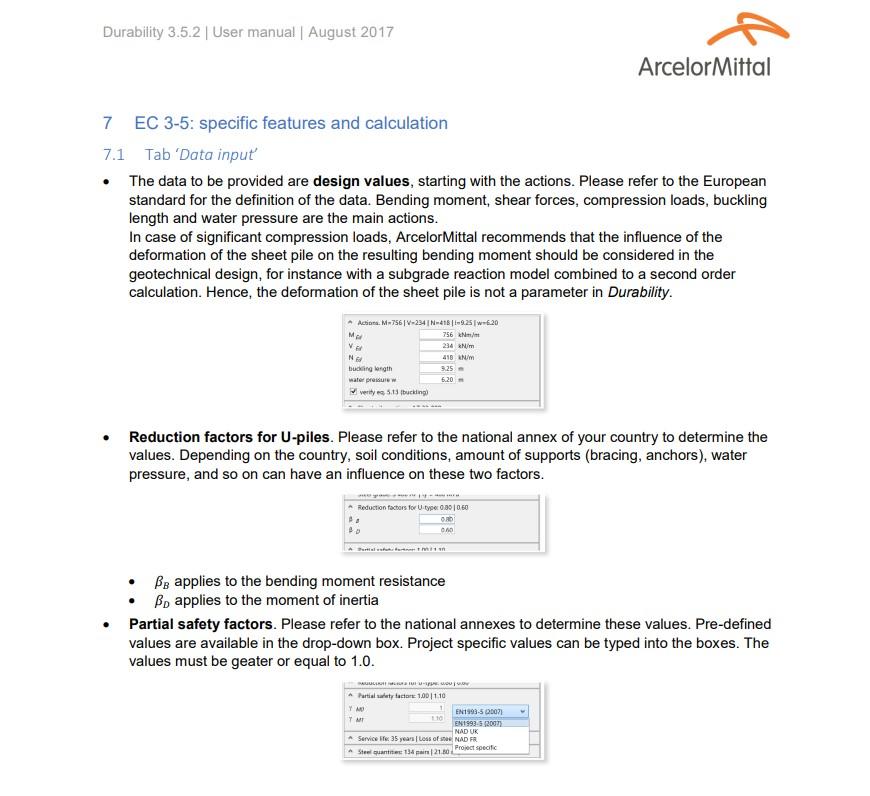
Question
I have installed the software and when I launched it the first time, it asked me for the serial code. I found it in on the webpage where I downloaded the installation file, entered it in the field, but I got a message stating the activation failed. What shall I do?
Answer
The automatic activation process is done over internet, but even when you have access to the internet, it unfortunately does not always work. The main reason is that nowadays computers are protected by a firewall that closes the ports required for the automatic activation.
The manual activation procedure, described on page 10 of the installation manual of the software, which is normally provided with the installation package, takes less than 10 minutes and works in almost all the cases.
However, should this manual activation fail too, please contact our technical department and we will do our best to solve the problem quickly: sheetpiling@arcelormittal.com.
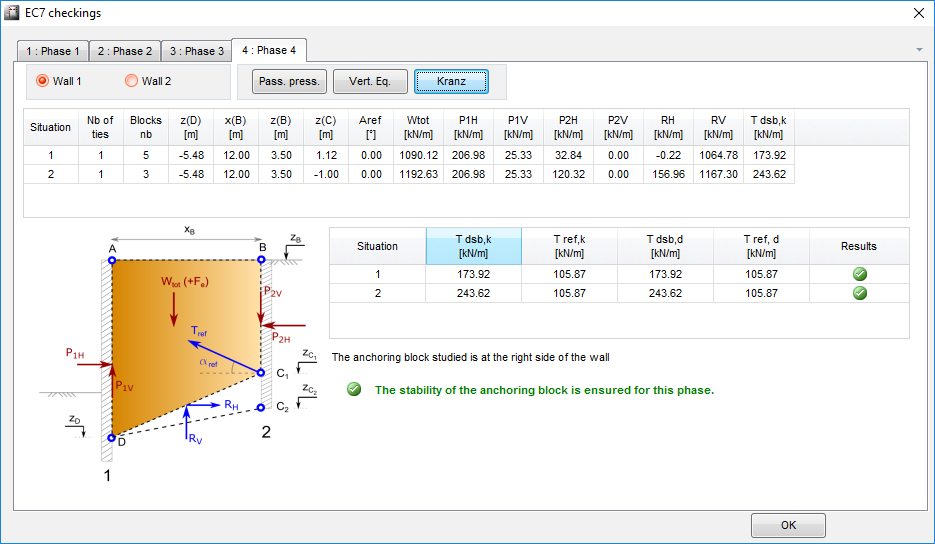
Question
Do you have a demo version of the software AMRetain? If not, how can I test the software before purchasing it?
Answer
AMRetain is a quite sophisticated and powerful software for the design of steel sheet piles. We do not supply a demo version, but in case of interest, an engineer from our technical department can schedule a physical meeting / webconference to present all the features of the software.
Notes
- AMRetain was developed to be used by experienced engineers,
- the price of the software is very attractive. Our goal is to promote the use of advanced design methods, but we do not intend to compete with commercial software.
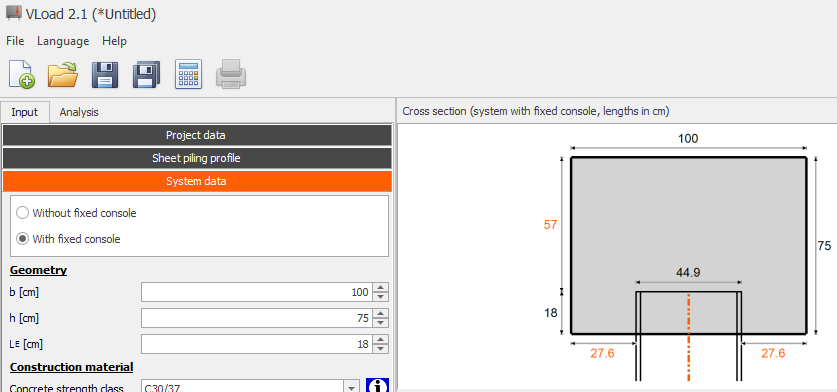
Question
I downloaded your VLoad free software, the lateral loading function doesn't work. Is there any particular reason why? We are predominately designing capping beams to transfer lateral loading from bollard pulls, this would be a useful function.
Answer
To use a lateral load (horizontal load), you need to select the option ‘With fixed console’ in the ‘System data’, with a minimum embedment depth of 18 cm. See printscreen below.
If you selected this option, added a horizontal load, and it does not work, your loading might be out of the scope of the design software capabilities, or there might be a bug in the software. In any of these cases, just send us a sketch with the geometry and loadings and we will analyse your problem more in detail.
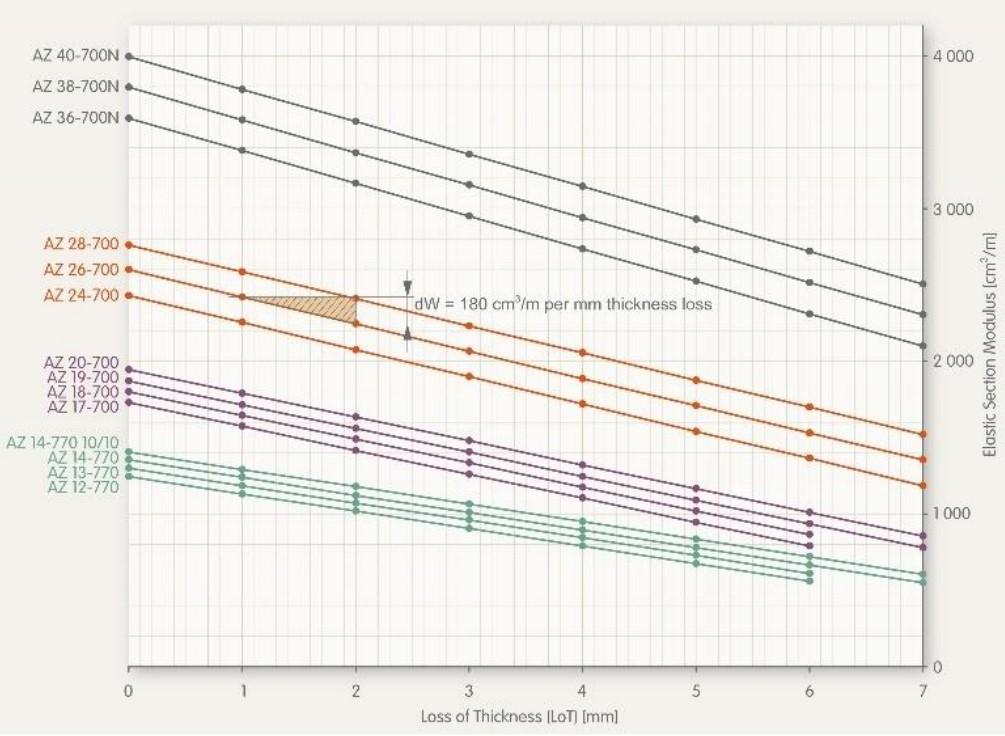
Question
The handbook of the software states that the maximum allowed loss of steel thickness of a sheet pile section is 7.0 mm. Why this limitation?
Answer
The software Durability uses a database with reduced section properties (section modulus, …). These properties were calculated based on simplified assumptions: uniform corrosion on one side of the sheet pile,...
Some sheet pile sections are still fit for purpose for losses of steel thickness above 7.0 mm, but our engineers believe that in such cases, a more rigorous calculation of the reduced section properties should be used. Please contact us for more information.
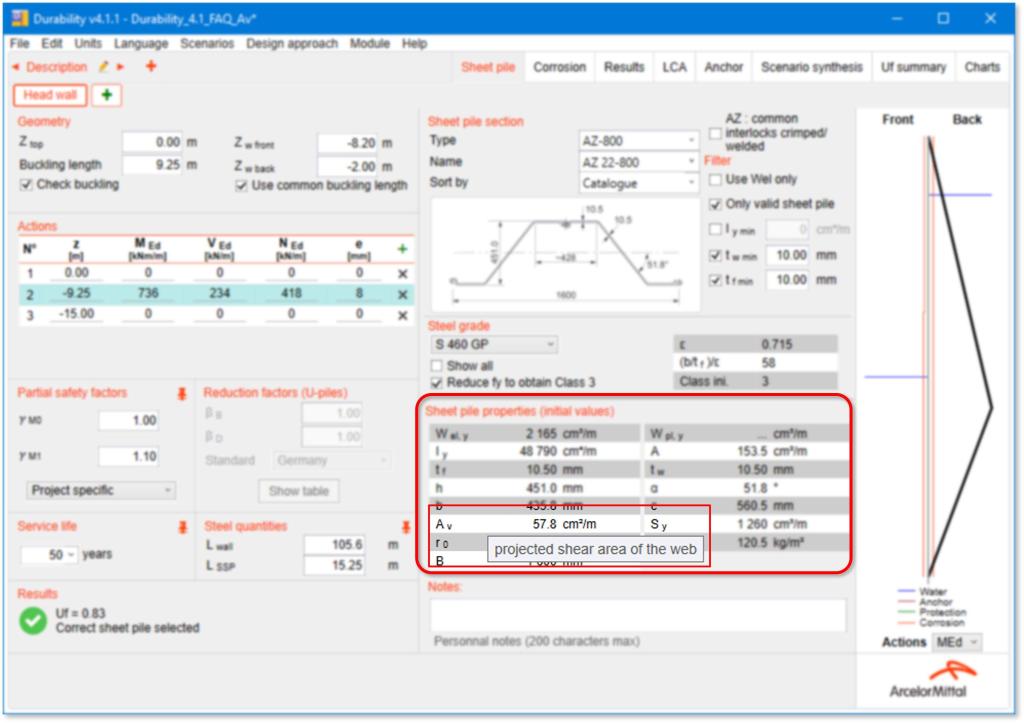
Question
The calculation of the projected shear area AV does not correspond to the formula (5.6) of Eurocode 3 - Part 5 (EC3-5).
Answer
The value of the shear area AV in the software is given in cm2/m, therefore per linear metre of wall, as are the values of Wel, M, V, etc.
The formulas in EC3-5 are expressed per element / per sectional area. The Durability software values per linear metre are found by dividing the Eurocode formula by the sheet pile width, for example by dividing by 0.8 m for an AZ-800 sheet pile.