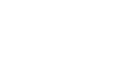
Mobility Infrastucture Solutions
Liefkenshoek rail link, Antwerp, BE | 2008
The 16.2 km long double-track railroad will contain two side by side single-track tunnels undercrossing the river Scheldt and the B1-B2 Canal Dock. The tunnels with an internal diameter of 7.3 m will be created by Tunnel Boring Machines (TBMs) over a distance of 6 km each.
Download the full case study
Once the TBMs will have passed underneath the Scheldt, they will go slowly upward towards the arrival shaft passing closely underneath the bottom of the Canal Dock. In the 270 m wide central zone of the dock, the soil overburden above the tunnel, consisting mainly of silt deposits, would only be 4.4 m thick, which could not provide sufficient resistance. Hence, the original design had foreseen to dredge 8 m of the silt and replace it with 138,000 m³ of compacted sand and a 26,000 m³ concrete deck on top of it. The compaction of the underwater sand layer to 17 MPa would have needed a 4 m thick temporary sand ballast of 38,000 m³, which would have reduced the dock’s draft by 2 m for a period of at least 6 months.
The contractor Locobouw consortium designed an alternative solution using steel sheet piles that enabled to reduce the construction time and to avoid the six months long hindrance for the shipping traffic in the dock. Locobouw proposed and executed a 270 m long and 32.5 m wide sheet pile wall excavation pit. As the silt has a very low natural slope, this permitted to reduce the dredging material substantially from the original 160,000 m³ down to 60,000 m³.
The rectangular shape of the pit allowed the contractor to pour 26,000 m³ of lowstrength mortar (≤ 5 MPa) instead of a much larger amount of sand backfill. Although more expensive, this mortar was preferred due to its higher performances. Indeed it has the ability to develop a vaulting effect after being drilled by the TBM, thus increasing the safety level of the TBM’s work when undercrossing the Canal Dock. In addition, the sheet piles and mortar are used as anchors for the 2 m thick slab of steel fibre reinforced concrete (16,500 m³ instead of initially 26,000 m³). Hence the necessary temporary ballast that would have disturbed the shipping traffic can be skipped.
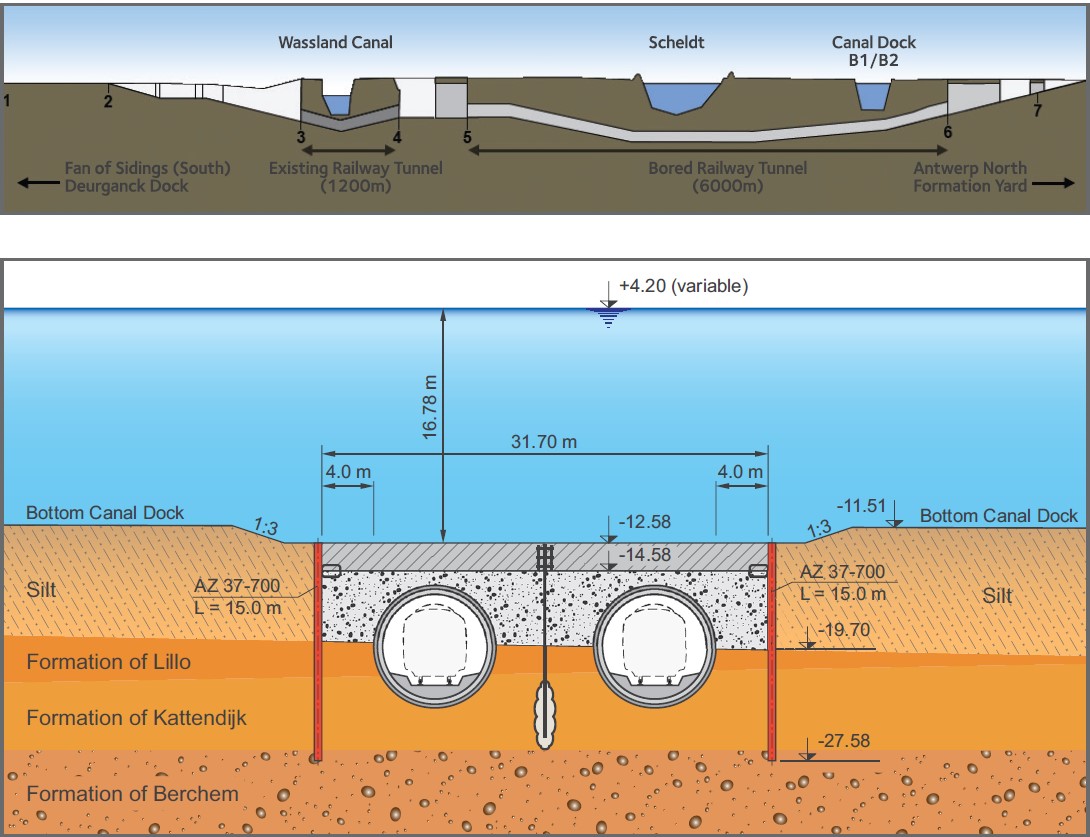
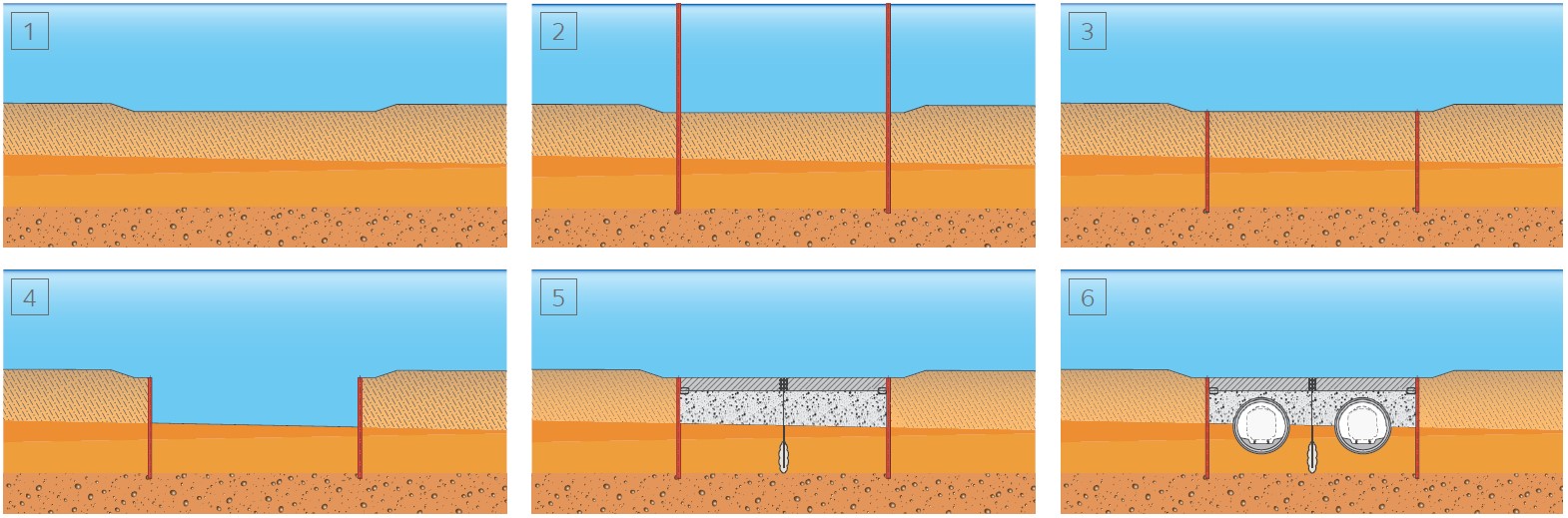
A driving test was performed in August 2009 with AZ 26 and AZ 37-700 sheet piles, including water jetting for the deepest parts of the wall, in order to confirm the choice of the sheet pile sections and the installation method. The actual driving of the sheet piles started in December 2009.
The excavation pit was designed as a cantilever retaining wall and was created by driving 2,212 tonnes of sheet piles with lengths between 23 m and 31 m.
These lengths made it possible to pitch the sheet piles above the water level and to use normal driving equipment. An ICE 36 RFts vibrator was used in combination with a D30 Delmag impact hammer in order to penetrate into the dense sand layers and reach the design level. The sheet piles were cut off under water by divers at the upper level of the silt immediately after driving. The top portions were recovered and bought back by ArcelorMittal (1,192 tonnes). The 540 m of wall were driven in 8 weeks time only.
The project is on track, and the first train is scheduled to undercross the Canal Dock by mid 2014. Even though the steel sheet pile alternative induced some challenges, like cutting the sheet piles under water, dredging in-between the sheet pile walls and concreting below water, these challenges were mastered by Locobouw in a very professional way.
The result is a safer solution for all stakeholders: project owner, TBM workers and Canal Dock users.
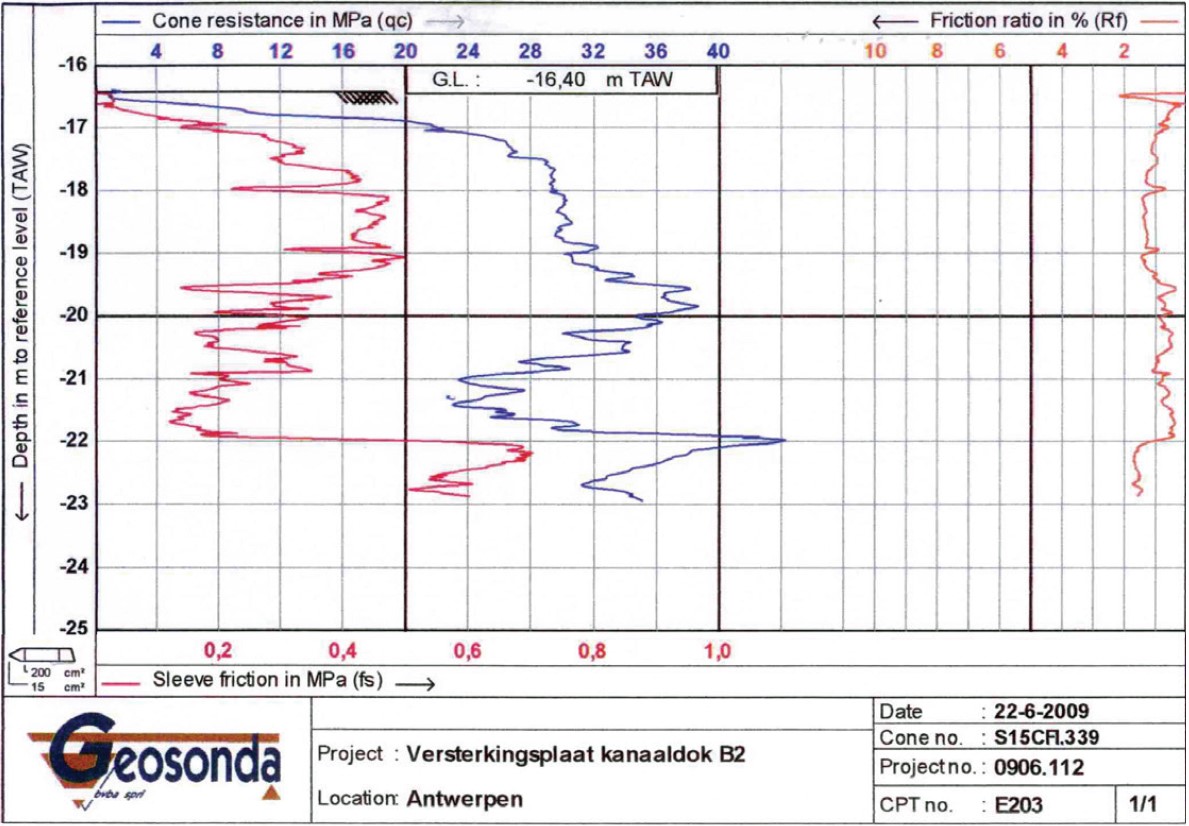