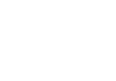
Hazard Protection Solutions
Rochester Riverside Regeneration, UK | 2009
The Medway area is located in Kent and includes the towns of Rochester, Gillingham, Rainham, Chatham and Strood. Medway has experienced sustained growth and diversification during the last two decades.
Download the full case study
Rochester Riverside is a flagship project within the Medway Council regeneration programme. It is a 32 hectare brownfield site with a 2.5 km frontage along the River Medway selected for the development of a mixed use complex including up to 2,000 new homes, shops, hotels and cafes, offices, educational, health and community facilities and recreational areas.
Since the 19th century the site has been home of large scale commercial and industrial activity, including gasworks which are no longer in existence leaving part of the land ripe for redevelopment. The historic use of the area left a legacy of contamination and old structures, requiring the utmost care and attention in this project.
The river frontage consisted of wharves, sheet piles, timber and concrete retaining walls, with some structures in a derelict state. The entire frontage was to be rebuilt as part of the scheme which aimed to protect against flooding risk, renew the river frontage and remediate the contaminants resulting from the old Gas Works site. The remediation of contaminated soil was processed through innovative methods, allowing treatment on site, including bioremediation.
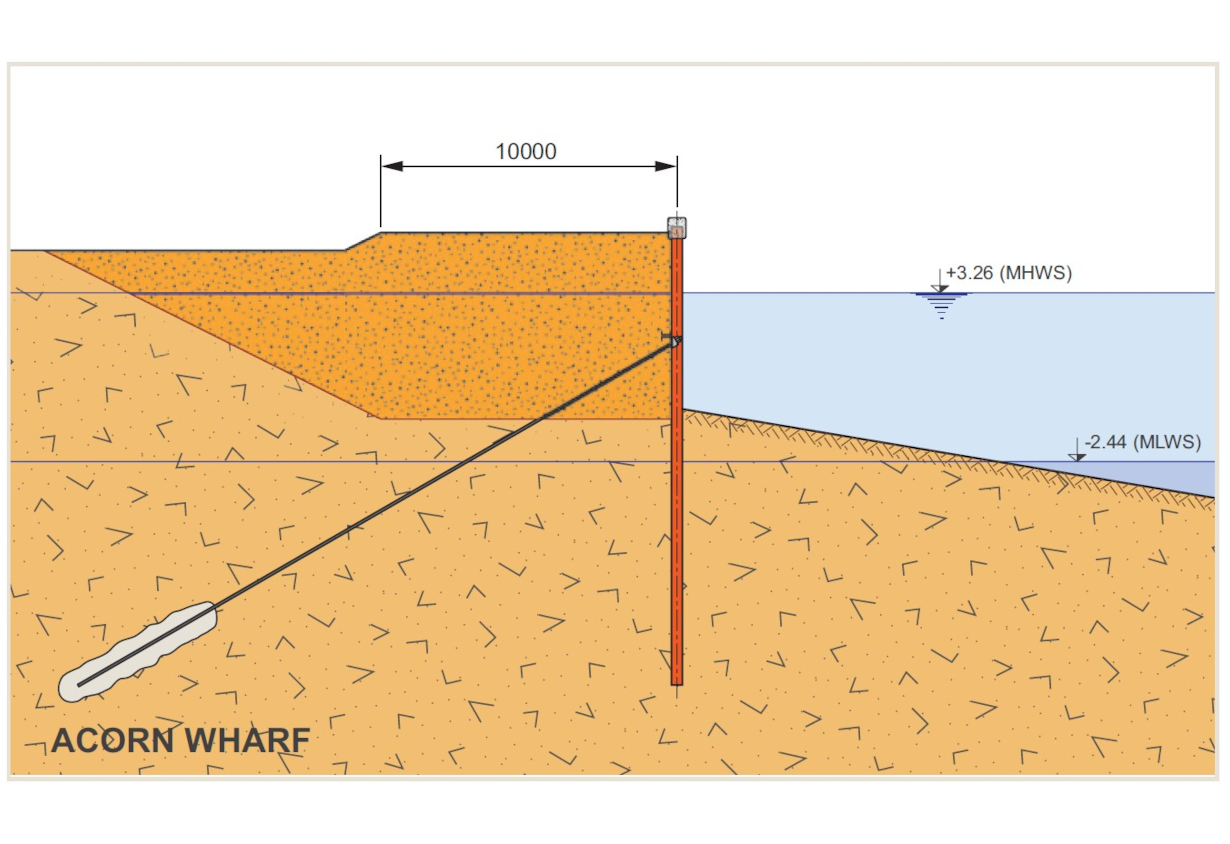
Increased ground levels were achieved by importing up to 400.000 m3 of sand, dredged from two locations in the Thames Estuary and transported by barge to the site. The contractor used extensive vertical band drains made of geotextile material, allowing to accelerate the settlement of ground below the newly placed fill.
The determination of the most effective flood protection river wall was guided by technical, economic and environmental considerations, but took also into consideration important health and safety factors.
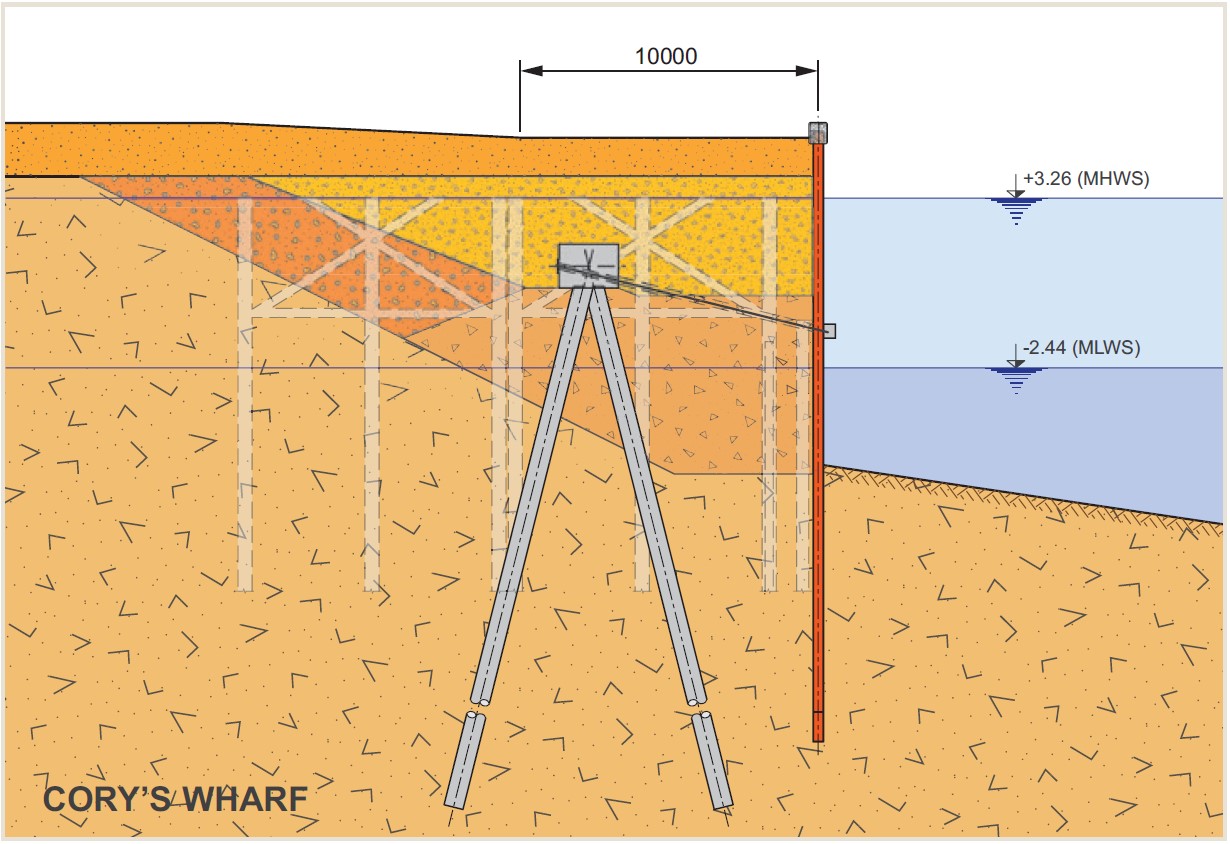
Several concepts have been evaluated, basing on different technical solutions, taking into account the removal of the existing frontage and hazards such as contaminated soil, tidal working conditions, unforeseen obstructions, differences in levels between existing and new walls.
Based on this evaluation, a front / flood protection wall in hot rolled steel sheet piles, offering the best technical and cost-effective solution, was chosen. The site utilised steel sheet piling for virtually the entire river frontage, creeks and wharves. The 2.5 km long sheet pile walls are approximately 15 m deep, and are topped with a concrete capping beam.
In some segments of the wall the sheet piles are placed in front of the existing structure with the void filled with crushed concrete. Due to the close location of future buildings to the walls, a full range of wall support systems were employed, including existing raking pile anchors with relieving platforms, raking “A-Frame” concrete piles, ground anchors, raking steel tubular piles and double steel sheet pile wall gravity structures.
The wider AZ sheet pile sections have been selected primarily because they offered the best cost / strength combination but also because their width facilitated faster installation and increased water tightness. Similar flange and web thickness also offered an enhanced design life in combination with Glass Flake Epoxy coating applied at the mill. ArcelorMittal supplied a total of 4,220 tonnes steel sheet piles.
Contractors programme required that deliveries were spread over nearly half a year, basing on just in time supplies by ship.
On site the good performance of the AZ sections during the driving process were confirmed by BAM Nuttall: at frontages, using panel driving techniques, 40 linear meters of wall per week were constructed, and on land, creek walls progressed at over 100 linear meters per week. All the steel sheet piles were supplied in S 430 GP high strength steel grade, giving the contractor extra safety margin if the driving got difficult at obstructions, and also facilitated a longer design life for the structure. Installation was primarily achieved with vibratory drivers (ICE 815 and Hf 12) crane suspended with 18 m leader rigs for the Creeks.
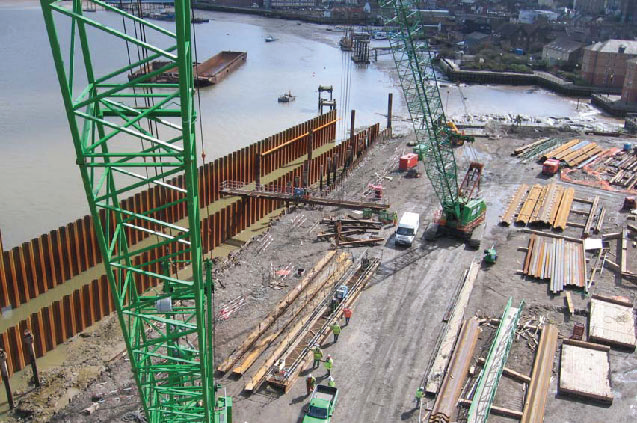
Supplies were handled in close and efficient co-ordination with the contractor BAM Nuttall / Van Oord Joint Venture. A particular challenge was to minimise the chances of any handling damage to the coating in transit. The material was shipped in special vessels from Luxembourg’s inland port in Mertert to Rochester, UK. Materials were swiftly and efficiently handled by the contractor’s Kobeko 7100 crane, using protective lifting gear for unloading and loading onto trailers for transfer to the nearby storage area.
As amply emphasized through press releases, Rochester Riverside is a flagship project with many challenges, both in terms of concept and execution, which have been met with innovative and integrated approaches, always putting the focus on highest quality standards. It is a reference for excellence in performance by all involved.