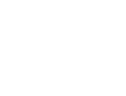
Water Transport Solutions
Spool base jetty in Dande, AO | 2006
Technip hired the Portuguese construction company Conduril to build this jetty located north of Luanda, near the mouth of the Dande River, for the service of barges and ships for spooling pipelines. It features a unique 600 m long jetty, with water depths of up to 11 m at the bulkheads. The quay is able to accommodate mooring vessels up to 100 m overall length and 4.9 m draft, as well as small craft boats. The larger spool ships are positioned in the open sea in a set of four mooring buoys.
Download the full case study
The geotechnical investigation showed that there was only a very thin soil layer over the bedrock. The initial design of the jetty considered a concrete structure, but the execution was a critical issue. AM CRPS’ engineering department worked out a few alternatives, including a cellular cofferdam, which is a cost effective solution for deep dredge levels in case of shallow bedrock elevation. Further alternatives and optimisations were evaluated before the contractor at the end decided to subdivide the jetty in two portions:
- the causeway to be built with a 10 m wide rock embankment;
- the 240 m long quay, which is 20 m wide, with a dredge level varying from EL. -6.0 m to EL. -10.8 m, executed with steel sheet piles.
The pavement is at EL. +5.5 m. Surcharge loads on the platform of the jetty are quite standard (20 kPa), and the foundation for the equipment for the spooling equipment of pipe is simple too. However, the design of the sheet pile wall itself turned into an exceptional challenge.
A short embedment of steel sheet piles driven into the bedrock was not expected to be sufficient for a conventional single anchored wall. The challenge consisted in designing and building a double-wall cofferdam that would call for at least two levels of anchors, with the lowest tie-rods placed way below the lowest seawater level.
A detailed analysis of all the different construction phases was performed in order to provide a safe working environment during installation and construction of the quay walls. A close collaboration between the design engineers in Portugal and AM CRPS’ in Luxembourg finally lead to an outstanding solution:
- a double wall cofferdam with three anchor levels;
- sheet piles ranging from AU 14 to PU 32 (depending on the water depth), in steel grades S 355 GP.
The final layout of this relatively complex structure was optimised by AM CRPS technical department. The design did not consider any supplemental protection measures of the steel in order to achieve the peculiarly short required service life of 15 years. Loss of steel thickness was estimated based on the European standard EN 1993-Part 5. The tie-rods were designed in high strength steel, with a minimum yield strength of 500 MPa, and up-set ends with diameters up to 85 mm.
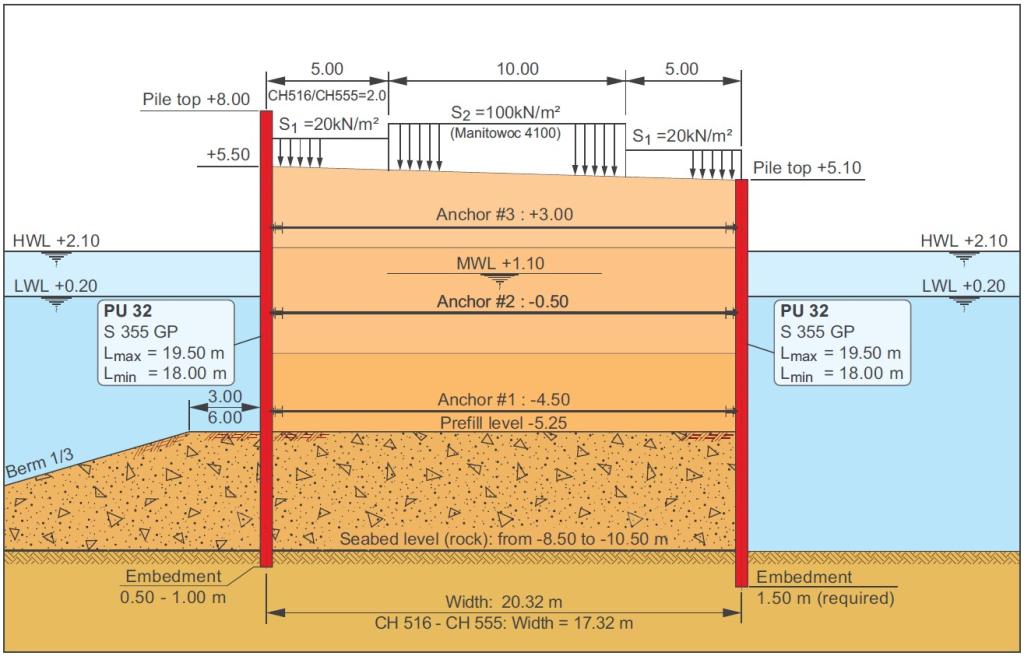
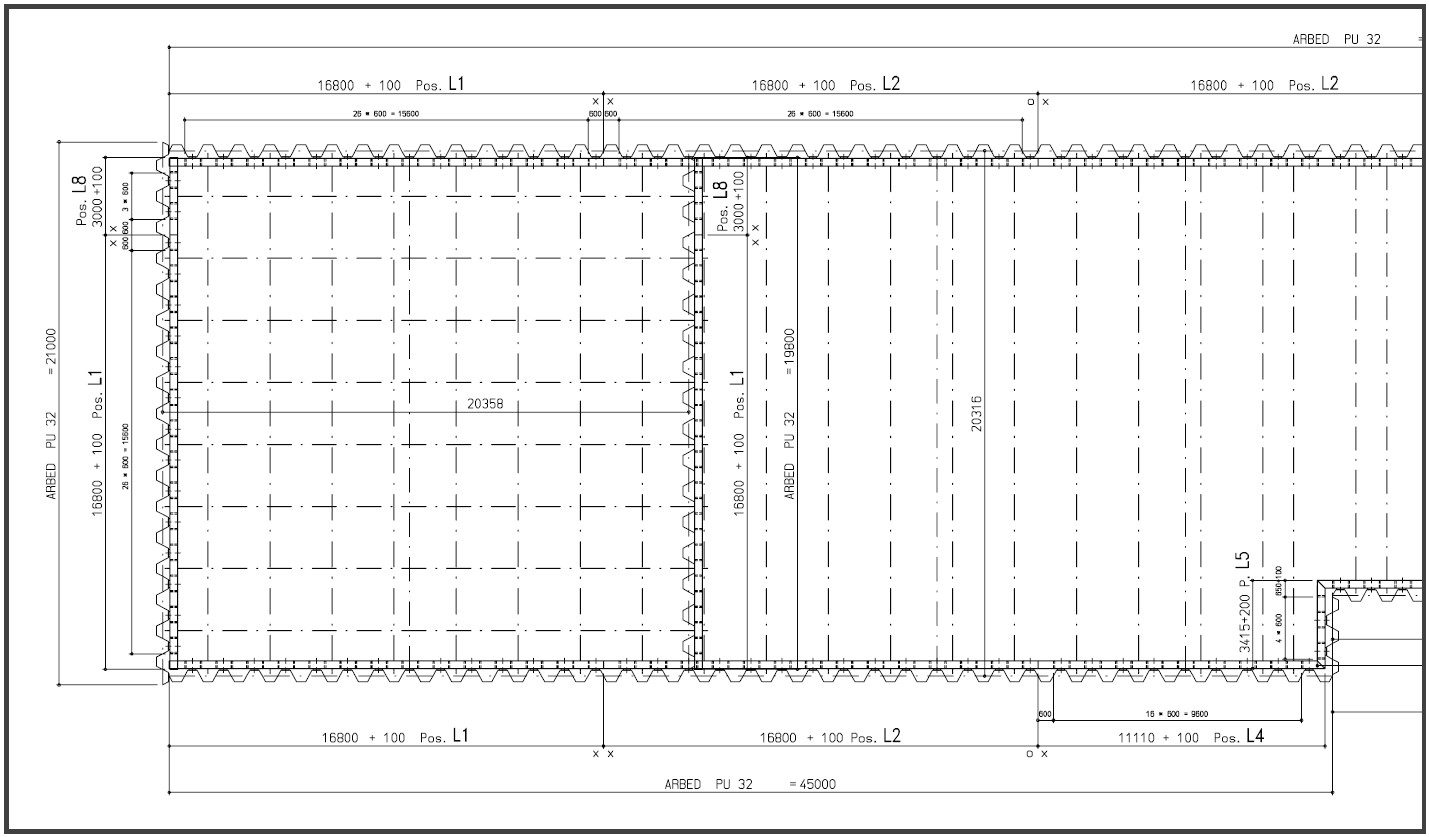
In order to prevent structural damages due to wave overtopping, the top level of the south portion of the quay wall needed to reach EL. +8.0 m. The worst case scenario is a combination of high water at EL. +2.1 m with a wave height HS of 3.7 m. The waves were also a threat to the stability of the berms and of the structure before the final backfill.
The execution of the structure comprised twelve different stages, and each had to be strictly followed to prevent the collapse of the structure during its erection. A backfill with berms was made before the installation of the sheet piles which were driven with an impact hammer into the bedrock (minimum penetration of 1.0 m).
Then, struts were installed in different phases inside the cofferdam, to allow the progressive dewatering down to the third anchor level. After that step, the installation of the tie-rods and walings started upwards: steel struts were removed before the next anchor was installed. Two intermediary sheet pile walls were foreseen at both ends of the quay structure. Furthermore, the contractor preferred to work from land in small stretches, which required the additional installation of temporary perpendicular sheet pile walls each 10 m.
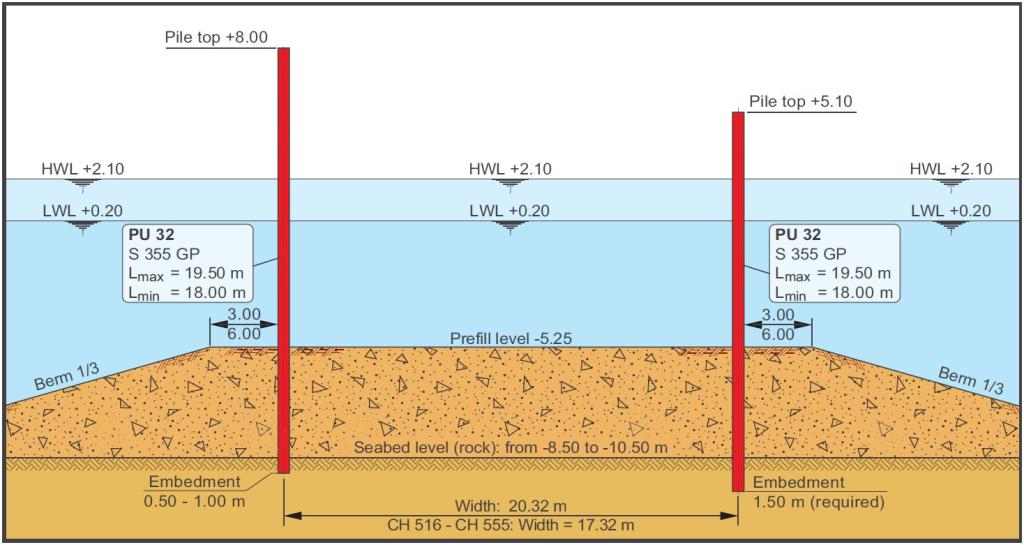
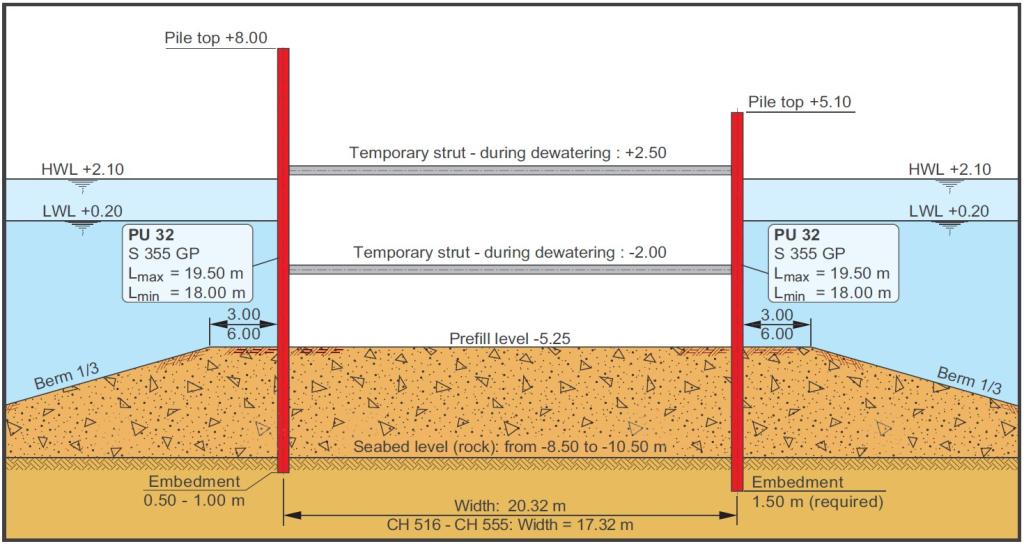
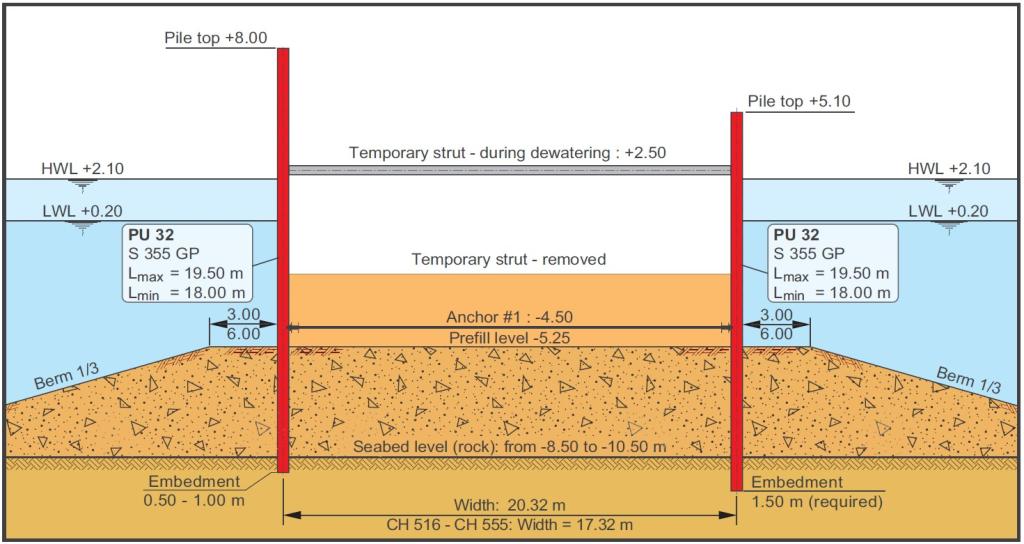
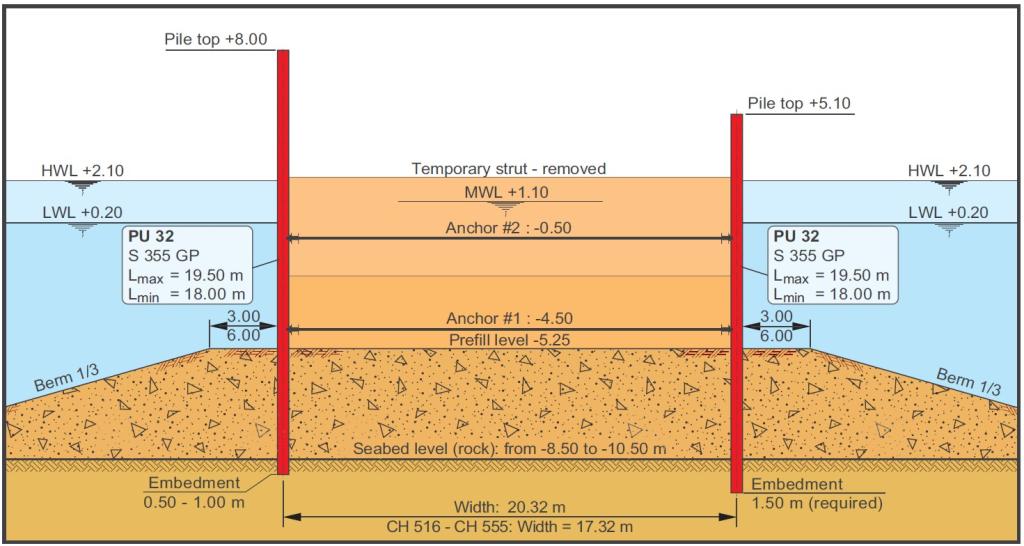
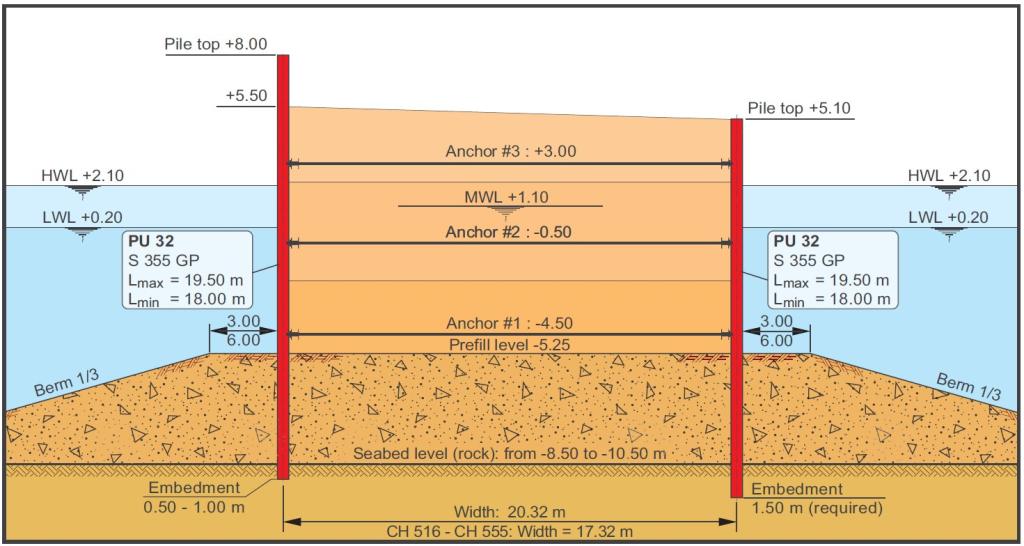

An undeniable advantage of the steel sheet pile solution is the fact that after the short service life, the sheet piles can be extracted with a vibratory hammer, and reused or recycled.
This exceptional port infrastructure was completed in a very short time. The steel sheet piles were produced in the Belval mill in Luxembourg, and delivered just-in-time at the job site. Furthermore, AM CRPS teamed up with Anker Schroeder, a German manufacturer of anchor material (tie-rods, bollards, walers,…), and offered a complete package which includes all the steel elements required for the foundations.
This successful project corroborates the fact that building cost effective steel sheet pile foundation solutions is in fact possible in countries where this construction method is not yet well known, even under very complex and unfavourable local soil and hydraulic conditions.