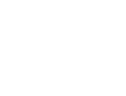
Water Transport Solutions
North Quay & South Quay - Port of Piombino, IT | 2012
Download the full case study
The investment of the Port of Piombino for the project in question amounts to 31 million €. The contract encompasses different projects, mainly:
- creation of functional berths “West quay of the Small Harbour” and “South quay of the Large Harbour” and the consequent adjustment of the yards behind;
- upgrading of existing sedimentation basins;
- reconstruction of the sewer system and industrial water discharge to the sea of existing plants (Lucchini and Magona);
- remediation of sediments of the sea area within the perimeter of the new quay walls, including two sedimentation basins for the discharge system of industrial water to the sea;
- emergency protection measures of the groundwater along the new quay walls;
- creation of a temporary jetty to protect the Magona dock;
- demolition of the pier Ex-Ilva. The demolition material will be reused for the execution of ecological islands in the sea;
One of the criteria for the choice of the deep retaining structure of the quay walls of the North and South Docks was to guarantee its imperviousness during its service life of 100 years. A cost-effective solution, with low maintenance costs that fulfils the criteria is a steel wall system HZ®-M/AZ® in combination with a sealing system.
The quay wall for the functional berths of the South, West and South Quay is 495 m long. The original tender specified an old HZ/AZ combined steel sheet pile wall HZ 975D-12 / AZ 26 in S 270 GP steel grade, tied back to an HZ 775A anchor pile with a pair of Gewi bars (Ø = 40mm), placed at intervals of 1.79 m.
In order to improve the performance and durability of the sheet pile wall the joint venture CMC-SALES proposed an alternative design during the tender period for the main quay wall: the new HZ 1080MC-14 / AZ 28-700, where the length of the RH connectors on the back flange covered only the segment with maximum stresses. Additionally, as the 34.0 m long HZ-M king piles exceeded slightly the maximum rolling length of the Luxemburgish mill, ArcelorMittal’s technical support team proposed to optimize the king pile over the depth by splicing a lighter HZ 1080MB beam on the bottom part of the king pile, where the bending moments are smaller.
Consequently, the king pile can be subdivided into four different sections, from

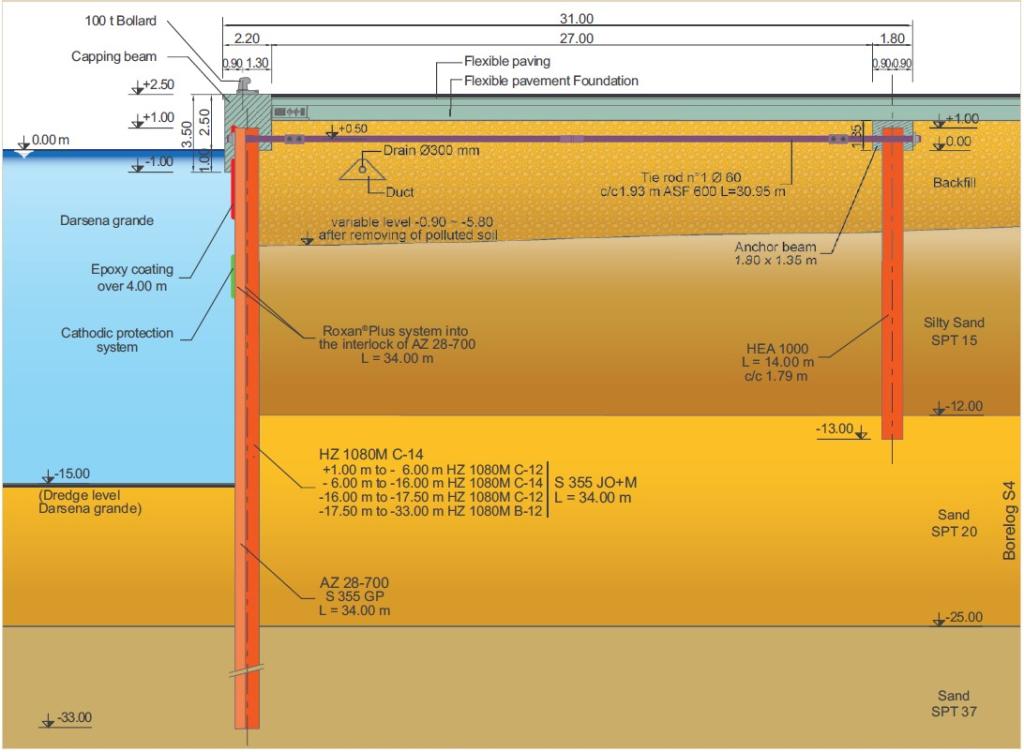
The sheet piles were shipped by rail to ArcelorMittal’s mill in Piombino, which is located directly next to the construction site. The RZD/RZU connectors were seal-welded and the sealing system Roxan®Plus was applied into the interlocks of the AZ infill sheet piles (water-swelling product in the free interlocks) in this premises. Furthermore, the splicing of the HZ-M king piles was also carried out there.
The main quay wall was realized by driving the steel sheet piles with a length of 34.0 m, and tied back at elevation +0.50 m above water level, by steel tie-rods connected to an anchor pile installed about 30.5 m behind the main wall. The HEA 1000 beams used as anchor piles are 14 m long, extending between the levels +1.00 above and -13.00 m below water level.
The next step in the optimization process of the original specification was to increase the steel grade: the king piles HZ-M were supplied in S 355 JO + M, and the AZ infill sheets in S 355 GP, thus enhancing the bending moment capacity of the wall.
Moreover, a temporary jetty to protect the Magona Dock was created with a row of re-used PU 25, 13.50 m long, taken from the contractor’s own stock. A perpendicular wall made of sheet piles at the back stiffened the main wall.
The soil is made up of layers of silty sand and sandy silt to a depth of -21.0 m below medium sea level, and lenses of “calcarenite” (limestone), or more commonly referred to as “panchina” (bench), with a thickness varying from 50 cm to 120 cm traced in different levels in depth.
The driving of the main quay wall was carried from the sea through a motor barge crane, a vibratory hammer PTC 100 HFV and hydraulic hammer IHC S70 to drive to the final level. A specific driving template enabled the correct positioning of the king piles. The anchor piles were driven from land with a vibratory hammer PTC 50 HFV hanging on a Linkbelt type crane.
Due to the quite unfavourable surrounding environmental conditions (salinity and brackish water), a cathodic protection system with impressed current was installed, as well as an epoxy coating on the water side, in order to limit the corrosion of the sheet piles and tie rods.
The system of sedimentation and sea discharge of water coming from the surrounding plant involved the construction of two small basins (7 x 40 m, resp. 42 x 40 m). In both constructions the bottom level of the basin is equal to -2.50 m below medium sea level. The perimeter walls and partitions of the basins were built with a combined wall using Ø 800 mm steel tubes, 10 mm thick, and AZ 13-770 intermediate sheet piles.
The works were performed by the joint venture CMC Cooperativa Muratori e Cementisti (CMC) of Ravenna and Sales SpA.
The fruitful collaboration with ArcelorMittal allowed optimizing the productivity of the work and ensuring the quality of the product offered on following aspects:
- reduction of lead times optimized by the proximity of the ArcelorMittal Piombino premises to the construction site;
- no interference with the port traffic guaranteed through the supply of the sheet piles by rail directly from the plant of ArcelorMittal Piombino;
- technical assistance with the design of the anchor piles, and the driving template for the HZ-M king piles.
The construction works started in March 2012 and the civil works are still running.
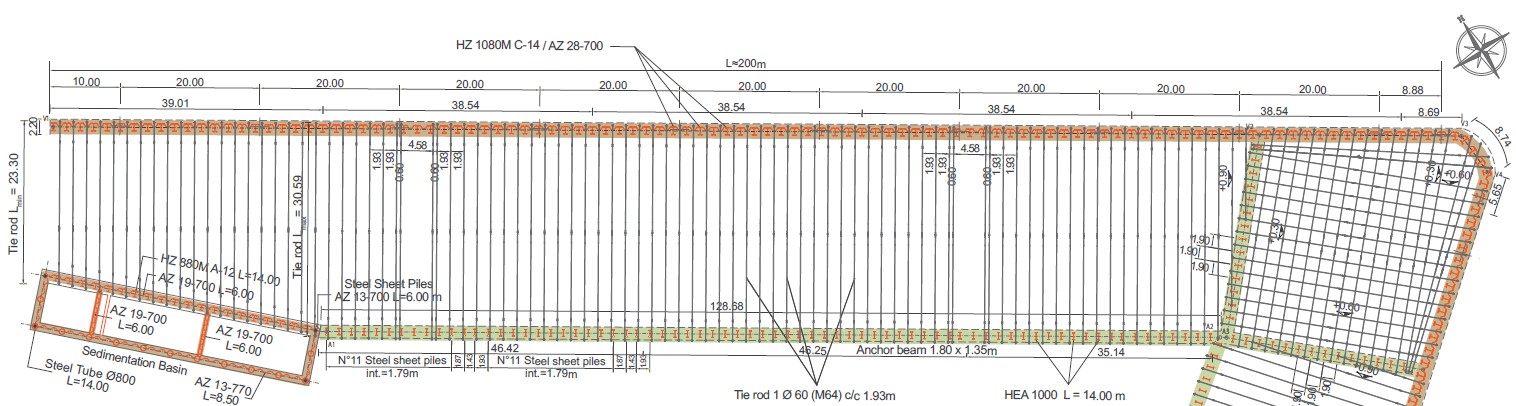