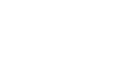
Mobility Infrastucture Solutions
Copenhagen-Ringsted Highspeed Rail (TP4), DK | 2014
Download the full case study
The proposed Copenhagen to Ringsted Railway Line covers a total distance of approximately 60 km and passes through 10 municipalities with the aim to provide extra capacity, faster trains and more flexible time tabling along this vital railway corridor. This new railway line will connect with the existing railway system in Copenhagen and Ringsted. It will run through densely populated and trafficked areas as well as historical, cultural and recreational locations.
The New Line Copenhagen-Ringsted assumes international importance as part of the Trans-European Network that will link Scandinavia and the rest of Europe. The railway is also a significant part of the freight corridor from Northern Sweden to Northern Italy. The opportunities to expand freight traffic – and to improve conditions for international travellers – will increase after the opening of the Fehmarnbelt Fixed Link and the associated upgrading and expansion of the line from Ringsted to Rødby.
The project was split into Tender Packages (TP). TP4 – tendered as a Design and Build contract - is one of the main civil works contracts. Among other infrastructure, it entails the constuction of two cut & cover tunnels of 1,270 m, 1,310 m of open trough, railway and pedestrian bridges, pumping stations and drainage installations. Sheet piles were used for the permanent tunnel walls of the Kulbane tunnel (abt. 15,100 m2) and for the retaining walls of the open trough sections (abt. 19,000 m2). The built up nature of the site provided a number of challenges and constraints for the proposed railway alignment which includes existing structures, highways, utilities and environmental requirements. As a result the railway alignment, in terms of both line and level, varies along the route and therefore required a combination of engineering solutions to provide an efficient and economical design.
In addition to the regular design requirements such as design life, durability, fire resistance and clearance profiles, the tunnels also needed to consider other requirements such as noise and vibrations, waterproofing below roads, excavation in contaminated soil, buoyancy/upthrust and future maintenance and operational requirements.
The deepest part of the Kulbane tunnel (length=700 m) resulted in excavations of up to 10.5 m below existing ground level. The Hvidorve tunnel (L=570 m in secant piles) is aligned adjacent to the existing Holbækmotorvejen highway and below the existing Vigerslev Alle and Allingvej roads. This required carefully planned traffic management and temporary works to ensure minimal disruption to traffic and to maintain access to properties around the site. The tunnel also had to be designed to resist traffic loadings and conditions. The deepest part of the tunnel resulted in excavations of up to 11 m below existing ground level.
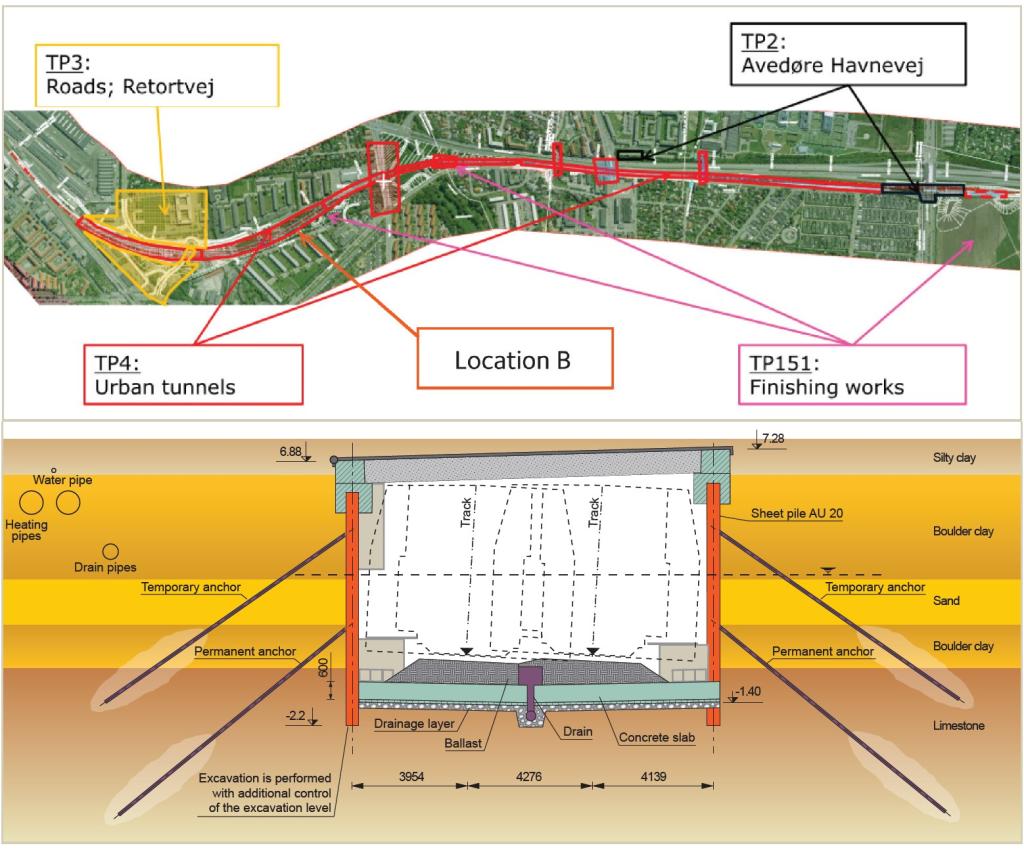
For the tunnel walls, the AU 20 section was chosen for driveability reasons - after successful driving tests - but also because of its increased width (1.5 m for a double pile) leading to economies in tonnage and construction resources. Expected stray current corrosion, at 3 to 4 mm for 120 years design life, was treated by accounting for sacrificial thickness in the section chosen. A further reason for this choice was that anchor plates in an AU section can be placed on a flat surface, hence making it easier for the welding to comply with stringent watertightness requirements. The anchors front assembly were enclosed in an accessible structure for maintenance requirements. Banedanmark requested that all seal-welding was executed in EXC3 (Execution Class 3) that is of a very high standard unusual for sealing for watertightness. The reasons for this were, that in the case of water infiltration, corrosion from stray currents may develop at a higher rate and also there could be a health and safety issue in case of the water freezing and detaching itself from the sheet piling surface. Impermeability of the bottom slab together with paticular care of the slab-sheet pile interface, will ensure watertightness of this tunnel part located below the water table. All seal-welded piles were tested 10% by Non- Destructive-Testing (magnetic testing) while 100% of the piles were visually tested.
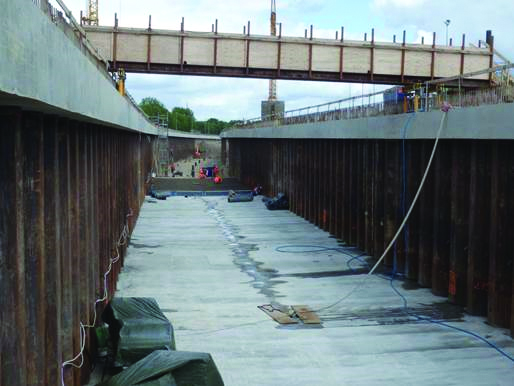
Fire protection for the sheet piles consisted of fire insulation material CAFCO® FENDOLITE® sprayed directly on the sheet piles. The system, used in Denmark for the first time, consists of 2 mm plastic net and two layers of 10 mm and 25 mm respectively of fire insulation material sprayed, after the sheet piles have been thoroughly cleaned with high pressure.
This innovative solution was tested by Banedanmark in order to verify compliance with current applicable legislation.
A further advantage of this solution is that as the insulation materials layers have a small thickness, more room is made available within the tunnel cross section for equipment installation. The sheet piles were driven with a PM26 piling rig and a Müller MS 40VM vibratory hammer. Timely delivery was also paramount for TP4 as for all TP projects, that proved to be a real logistics challenge due to the high tonnage that had to be delivered in a short period of time. In addition, orders for all TP projects often included various lengths of the same section in small steps, e.g. 10.1 m, 10.5 m, 10.9 m, hence adding to the challenge for the supply chain. This altered our ideas of ways of delivery. The bottleneck was solved by using a new hub in Køge from where part of the orders was delivered by truck directly on the site to avoid delays.
Construction started in 2014 and the project is expected to finish in 2016.