Underground car parks | The Netherlands
In the Netherlands, constructing underground car parks (UCP) demands a solution tailored to the region's soft soil and high groundwater conditions. Steel sheet pile (SSP) walls have emerged as the most sustainable and efficient choice for UCPs with 1 to 4 levels below ground.
Why Choose Steel Sheet Pile Walls?
- Dual Functionality: SSP walls serve both as retaining walls and foundations, minimizing the need for internal columns and optimizing space;
- Cost and Time Efficiency: SSP walls are up to 50% cheaper and can halve the construction time compared to other methods;
- Environmental Benefits: SSP walls significantly reduce the carbon footprint, with emissions up to 88% lower than concrete alternatives.
Here you will find detailed information why you should choose Steel Sheet Pile Walls for Underground car parks.
Underground car parks
Guide Book | The Netherlands
Comprehensive study of Steel Sheet Pile Walls
Steel sheet pile walls are the most sustainable alternative for underground car parks (UCP) with 1 to 4 levels below ground in the Netherlands: typical Dutch soft soil conditions, high groundwater table and the long-lasting experience of Dutch driving companies. The most efficient solution is to utilise the sheet pile walls for the temporary and for the permanent phase. Besides, sheet piles can transfer vertical loads to the soil, thus acting as a retaining wall and as a foundation, which reduces the number of columns inside the peripherical walls. The execution methods that can be envisaged are the classical bottom-up, and the unique top down.
Generally speaking, compared to alternative solutions, steel sheet piles are up to 50 % cheaper, and the execution of the retaining wall is up to 2 times faster.
In city centres, an additional advantage of steel sheet piles compared to alternative solutions is the reduced amount of trucks that deliver material to the job-site, as well as the little space required for storage and installation: less traffic congestion, less disturbance to neighbours.
Underground car parks
Part 1. Technical & Cost Analysis
Detailed Design | The Netherlands
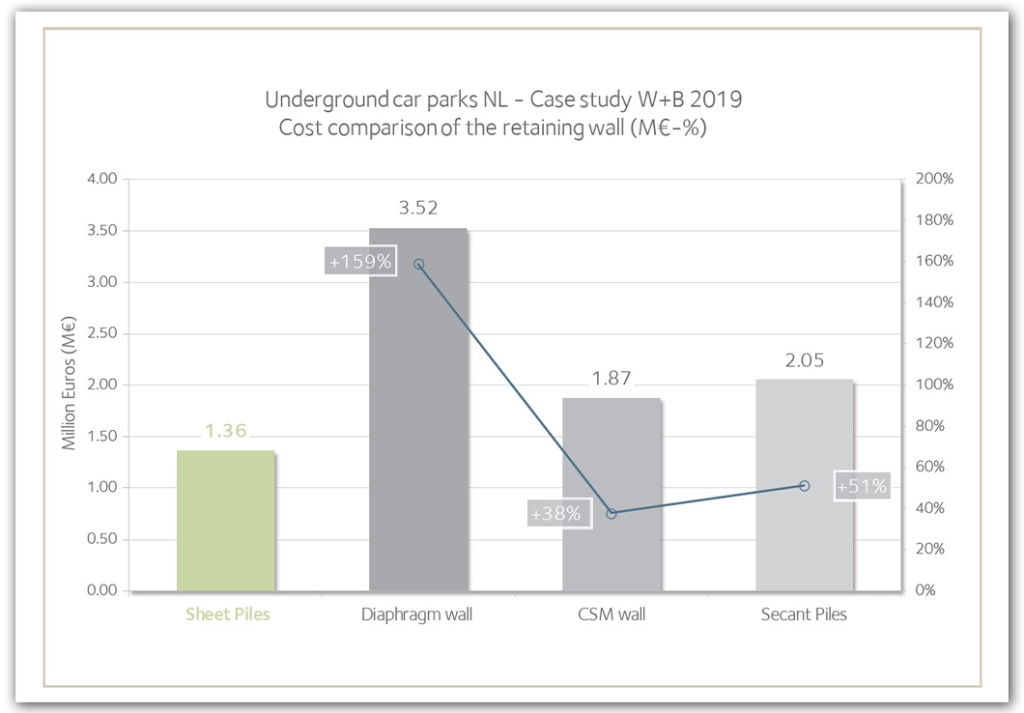
The impact of the wall type on the overall costs is significant, but within a bandwidth of less than 10 %. The walls themselves have a much bigger bandwidth in costs but will also bring additional costs later on in the construction process, such as fire safety protection and duration of construction. Since the installation of the wall is a basic requirement in order to proceed with the construction, the installation/curing of the wall is always on the critical path. This implies that any time saved on the wall construction has an immediate impact on total construction duration and the related investment, cashflow and duration of hinderance.
From this analysis it can be concluded that the pressed in sheet pile retaining wall is the most cost-effective solution: lowest cost, fastest execution and high quality in terms of watertightness and impact on surrounding structures. The D-Wall provides a robust solution but appears too expensive and too heavy for a 2-level car park solution. In sandy soil with a shallow groundwater table, the secant pile and the SoilMix retaining walls should not be used because of the risk of the lack of watertightness.
Underground car parks
Part 2 | Life Cycle Assessment
Detailed Design | The Netherlands
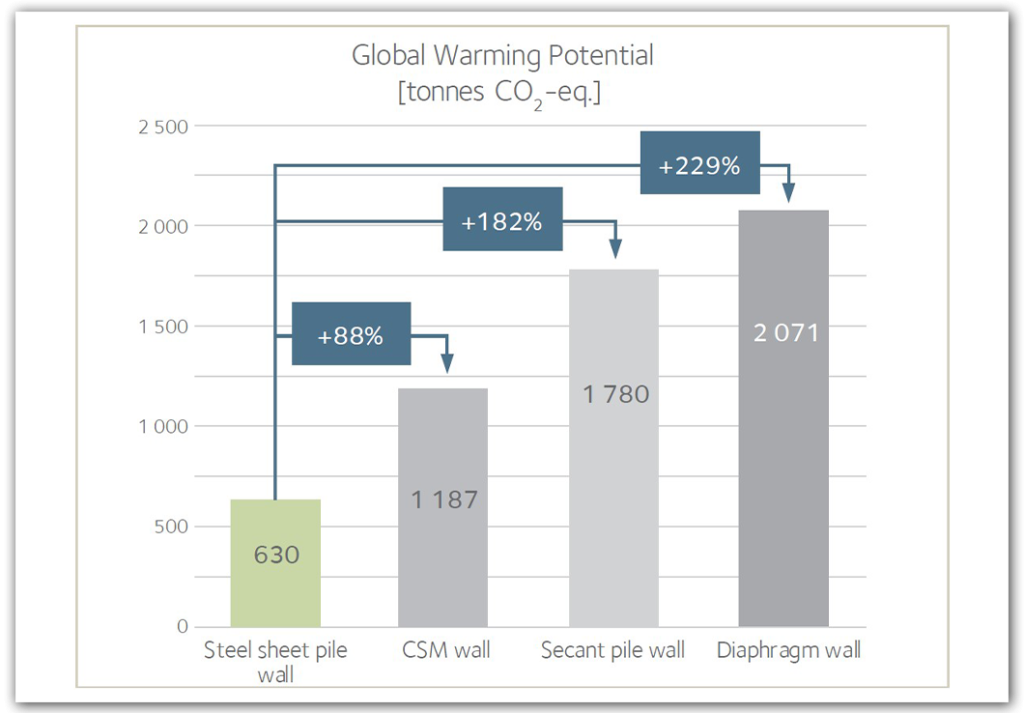
The key conclusions of this LCA for this specific case study is that the underground car park executed with a steel sheet pile retaining wall has a much lower carbon footprint (expressed in emissions of CO2-eq.) than equivalent alternatives in concrete (diaphragm wall, secant pile wall) and a deep soil mix wall (cutter soil mix). In the basic scenario the minimum difference is 88 % and varies for additional scenarios from +35 % up to +325 %.
Compared to the concrete solutions (D-Wall, secant pile wall) and to a cutter soil mix wall, the carbon footprint of the EcoSheetPile™ solution (SSP) is by far lower. In the basic scenario the minimum difference is 88 %