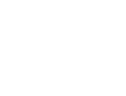
Water Transport Solutions
Port of Piombino, Livorno, IT | 2014
The Port Master Plan includes the construction of a new dock with a 350 m long and 50 m wide East Quay. The dock will be dredged to 20 m below average sea level (l.m.m.).
Download the full case study
The East Quay’s original tender documents specified a tube combined wall solution, where the primary elements were 38 m long steel tubular piles, Ø 2060 mm, steel grade S420 MH, with a variable thickness of 26 and 32 mm in function of the design draught; the tendered intermediary sheet piles were 29 m long Z sections with an elastic modulus of 3 870 cm3/ double element in steel grade S430 GP.
The combined wall was planned to be anchored at -0.50 m below l.m.m. with steel tie rods Ø 120 mm, one each primary element, to a reinforced concrete beam positioned in the vicinity of the breakwater at the sea-side of the quay platform (see «Typical cross section»). The distance between the main wall and the anchor beam was approximately 38 m.
In order to provide a more economical solution and a faster delivery, ArcelorMittal, in collaboration with CMC, proposed an alternative design using spirally welded tubes with a constant wall thickness of 26 mm (locally reinforced when needed), a higher anchoring level and a more economical intermediary sheet pile.
The alternative solution consisted of steel tubular piles, Ø 2060 mm, reinforced with two internal stiffener steel plates (600 x 26 mm), shaped to fit the tube curvature, welded both parallel and perpendicular to the tube’s longitudinal axis. They are placed in the positions of the highest stresses: 90° from the clutches from elevation -4.50 m to -25.00 m below l.m.m. The intermediary sheet pile section selected was an AZ 28-700 in S430 GP, with an elastic modulus of 3 865 cm3/double element.
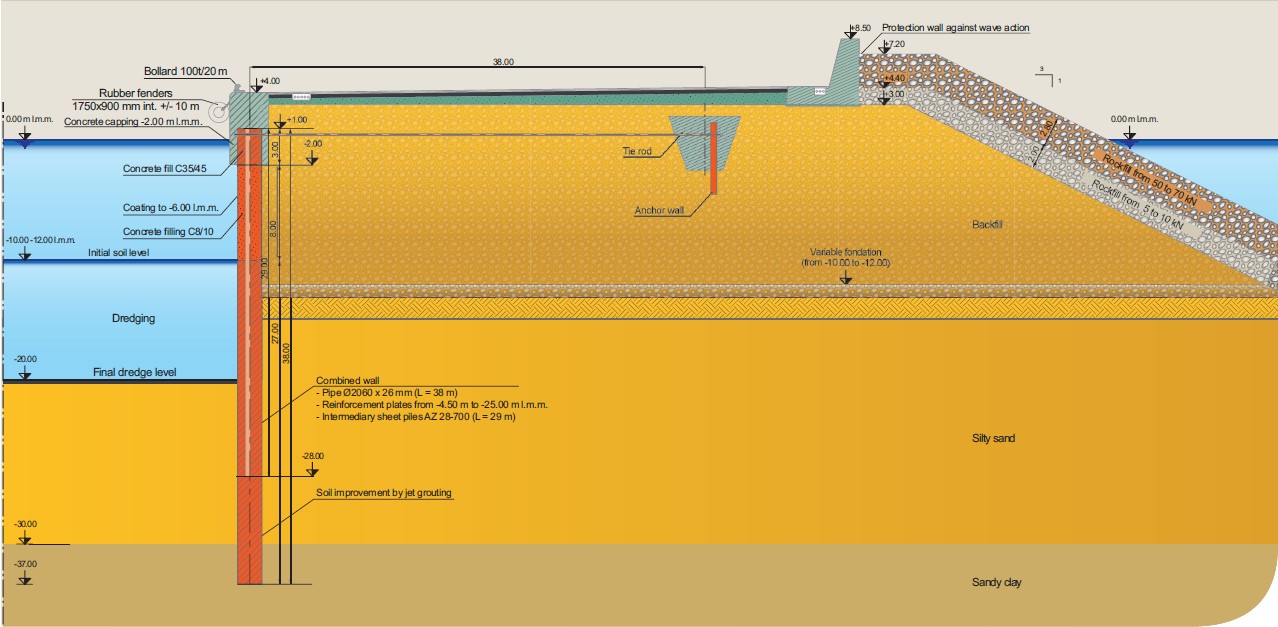
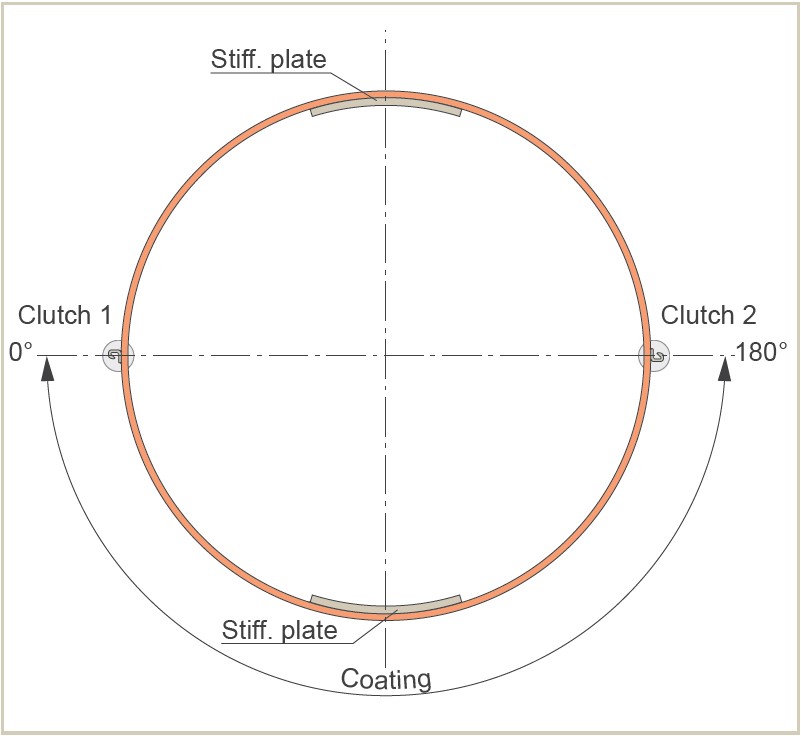
The actual tie rod position was raised from level -0.50 m to +0.50 m above water level, outside the usual tidal movements, in order to lower the corrosion influence. The rise in the anchoring level causes a different distribution of the acting forces, causing a modest increase in the stresses on the tube at a slightly higher elevation, while reducing the anchoring forces. This reduction in the forces acting on the tie rod prolongs its service live while maintaining its diameter (Ø 120 mm). The higher stresses in the tubular pile, however, are countered by the positioning of the reinforcement plates inside.
The design of this tube combined wall was performed according to Eurocode 3 (Part 4 and Part 5) and Eurocode 8 (seismic design).
The minimum quay wall design life time is 100 years, without considering the additional measures that can extend the design life time up to 300 years, which are:
- steel stress verification performed assuming a corrosion loss for 100 years;
- coating over the 7 upper meters of the combined wall;
- cathodic protection (the anchoring system, the combined wall and the concrete reinforcement);
- filling of the steel tubes with concrete and jet grouting (this also helps to avoid ovalisation and increase the pile inertia).
Due to the soil conditions, consisting of an upper medium-dense silty sand layer (ϕ =30°~34°) up to -30.00 m below l.m.m, and a lower sandy clay layer (cu=110-150 kPa) up to -50.00 m below l.m.m, a normal frequency vibratory hammer could be used for the installation. Also, as a part of ArcelorMittal’s services, a complete custom-made driving template was delivered to the jobsite to enable the accurate driving of the 111 tubular piles. The driving was carried out between June and October 2014.
The Piombino Port project showcases perfectly the advantages of collaborating with ArcelorMittal’s technical services. Thanks to this collaboration among designers, contractors and supplier, a more simplified and cost efficient solution has been installed. The different technical modifications explained resulted in an easier execution and significant savings in steel weight (the installed intermediary piles are 20% lighter than the tendered ones).
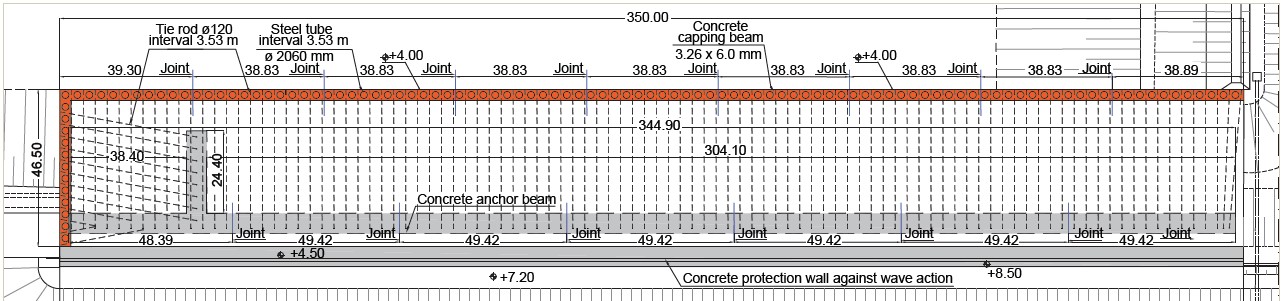