Gründungslösungen für den Hafenbau
Innovative Stahlspundwandlösungen für moderne Häfen
ArcelorMittal verfügt über mehr als ein Jahrhundert an Erfahrung in der Bemessung und Herstellung von Stahlspundwänden. Dank der Innovationen seit 1911 stellen U- und Z-förmige Bohlen heute eine der fortschrittlichsten Lösungen für den Bau und die Vertiefung von Kaimauern dar.
Der weltweite Verkehr nimmt stetig zu und damit auch die Größe der Containerschiffe. Diese Expansion stellt eine erhebliche Belastung für die Infrastruktur der Häfen dar und diese müssen massiv investieren, um den Anforderungen der neuen Schiffsgenerationen gerecht zu werden. Stahlspundbohlen bieten eine nachhaltige und kosteneffiziente Lösung für moderne Häfen, sei es für die Vergrößerung der Ausbaggerungstiefe durch das einfache Einbringen einer Spundwand vor einem bestehenden Bauwerk oder für den Bau einer völlig neuen Kaimauer. Das unkomplizierte und schnelle Einbringen ermöglicht es, dass das neue Bauwerk innerhalb kurzer Zeit betriebsbereit ist. Darüber hinaus erfordern die Einbringarbeiten nur einen reduzierten Personal- und Geräteeinsatz.
Das Forschungsteam von ArcelorMittal entwickelt neue Spundbohlen und Zubehör, um die besten Produkte auf dem Markt anzubieten und die sich ständig ändernden Anforderungen der dynamischen Schifffahrts- und Logistikbranche zu erfüllen. Zu den neuesten Entwicklungen gehören die AZ-800 Profilreihe, die 750 mm breiten U-Bohlen und die unübertroffenen HZ-M Tragbohlen mit einer Profiltiefe von bis zu 1.100 mm, die speziell für Kaimauern mit einem Tiefgang von 20 m und mehr entwickelt wurden. Die Bauindustrie muss heute widerstandsfähiger und nachhaltiger werden. Neue Projekte müssen über ihren gesamten Lebenszyklus hinweg mit geringen Umwelteinflüssen konzipiert werden, wenn wir bis zum Jahr 2050 Kohlenstoffneutralität erreichen wollen – ein Ziel, das sich die Regierungen im Jahr 2015 gesetzt haben. Stahl ist ein ideales Material zur Veranschaulichung der „Kreislaufwirtschaft”: Er kann zu 100 % verwertet werden, wobei seine Eigenschaften erhalten bleiben, und er kann mehrmals wiederverwendet werden, bevor er zu 100 % recycelt wird.
Diese Seite gibt einen Überblick über Hafenprojekte, bei denen verschiedene Arten von Stahlspundwandlösungen zum Einsatz kommen. Aufgrund zahlreicher Vorteile wie ihrer intrinsischen Qualität, Nachhaltigkeit, Ausführungsgeschwindigkeit,... gewinnen Spundwandkonstruktionen weltweit zunehmend an Beliebtheit.
Möchten Sie weitere Beispiele finden?
Voisey's Bay | Labrador | Kanada
> Bau von dauerhaften Hafenanlagen
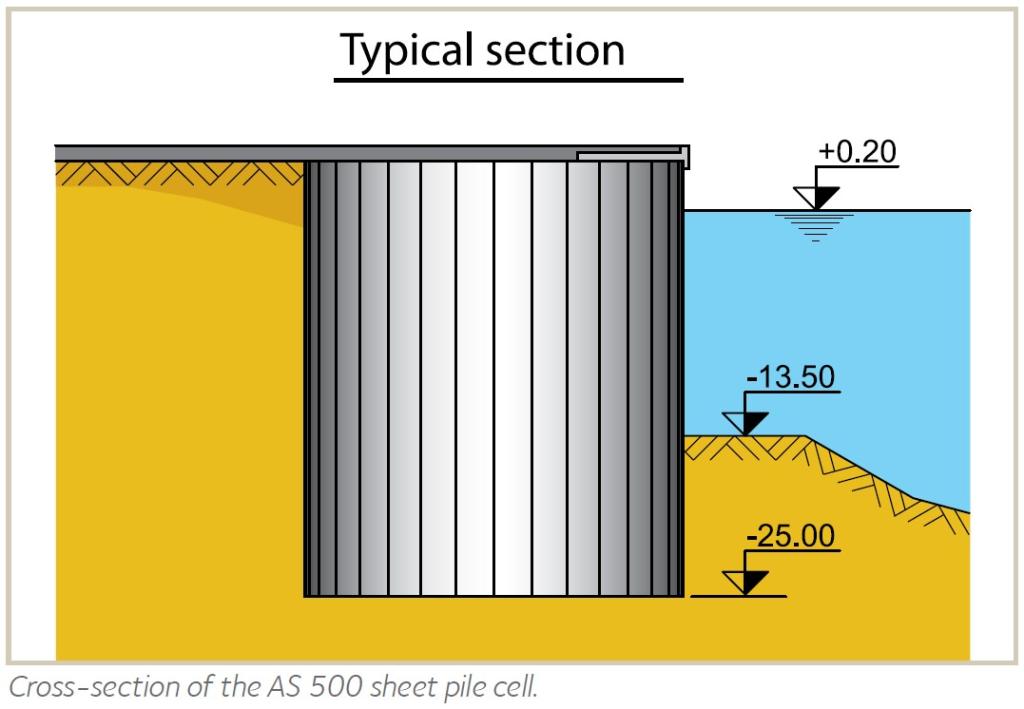
Das Dock hat eine Liegefläche von etwa 100 Metern und einen Mindesttiefgang von 13,5 Metern. Westmar Consultants Inc. (Bemessung von Meeresbauwerken) und Jacques Whitford (geotechnische Bemessung) legten gemeinsam den Entwurf für eine neue Tiefsee-Kaianlage in der Anaktalak-Bucht vor, die bis zu sechs Versorgungsschiffe und Konzentratfrachter pro Monat aufnehmen soll.
Als Hauptbauwerk wurde ein Kreiszellenfangedamm gewählt. Einzelne Spundwandzellen wurden in den überwiegend dichten Sand-/Kiesboden gerammt. Da das Spundwandsystem AS 500 aus statischen Gründen keine Einspannung in tiefere Bodenschichten erfordert, ist es eine Standardlösung für extrem harte Bodenverhältnisse. Die Planung der Kaianlage stellte eine besondere Herausforderung dar, da der Bau innerhalb einer kurzen eisfreien Saison abgeschlossen werden musste. Mehrere geotechnische Bohrungen wurden vor dem Einbringen der ersten Spundbohlen nicht abgeschlossen.
Die Geologie des Standorts Anaktalak-Bucht lässt sich vereinfacht in drei verschiedene Bodenschichten unterteilen, die über dem Grundgestein liegen. Die Oberfläche zeichnet sich durch eine bedeutende Zone aus weichem bis festem Ton aus, die eine Sandschicht mit Steinen und Geröll überlagert. Die Steinschüttung für die Zellen und die Wiederverfüllung bestehen aus feinkörnigem, kantigem Material. Das Ausbaggern der sehr weichen Sedimente musste vermieden werden. Dies führte zur Entwicklung eines hochmodernen Instrumentierungsplans zur kontinuierlichen Überwachung der Standsicherheit während der Bauarbeiten.
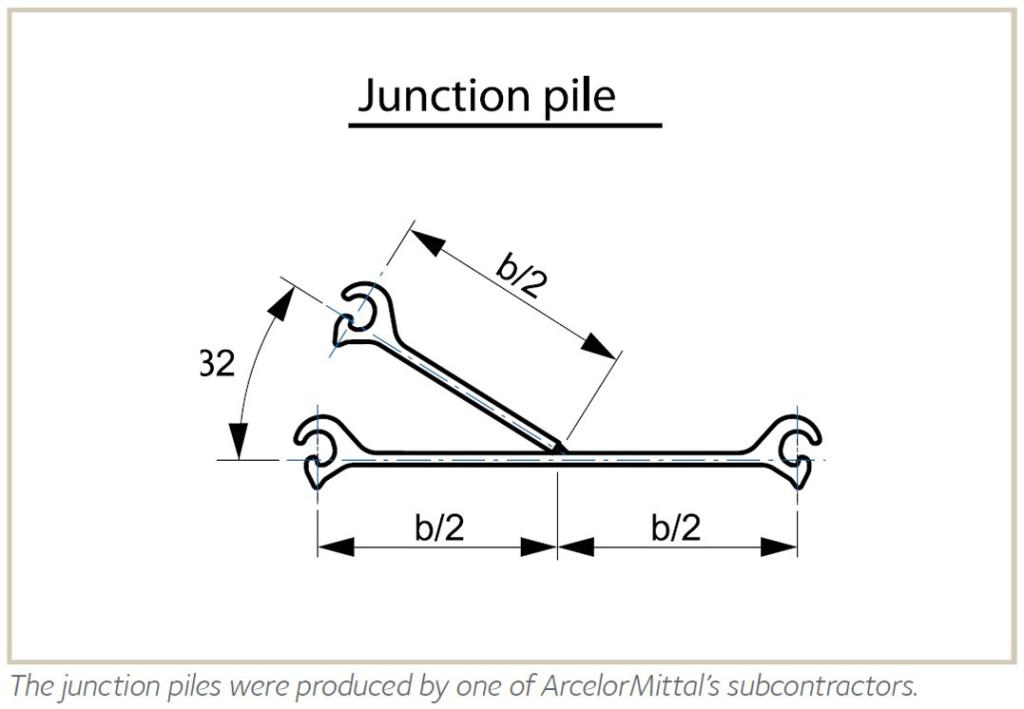
Eine Reihe von gekrümmten Betonfertigteil-Eisprallplatten mit einem verstärkten Oberbausystem ergänzte die Festigkeit des Hauptbauwerks. Während des Entwurfs der Spundwandkonstruktion wurden verschiedene Versagensmechanismen (Kippen, Gleiten, Schlossversagen sowie horizontales und vertikales Scherversagen) untersucht. Die Eislasten waren aufgrund der extremen Winter mit Temperaturen von bis zu -40 °C (-40 °F) ein wesentliches Bemessungskriterium.
Die Stirnseite der am Rand befindlichen Kaianlage besteht aus vier AS 500 Zellen, die durch sechs Bögen miteinander verbunden sind. Die Spundwandzellen, die die Stirnseite der Kaianlage bilden, dienen auch als Stützkonstruktionen für das Verfüllmaterial. Vor den Zellen wurde ein Kolkschutz angebracht, in den die Spundbohlen eingerammt wurden. Nach dem Aufstellen der Zellen wurde der Bereich hinter der Kaianlage mit Baggergut verfüllt.
Für den Bau der vier Zellen und sechs Bögen wurden von ArcelorMittals kanadischem Vertreter, Skyline Canada, folgende Mengen an Spundbohlen geliefert:
- 680 Flachbohlen;
- 72 Flachbohlen, die um 7° geknickt wurden;
- 12 Abzweigbohlen mit Flachprofil.
Jede Hauptzelle, die aus 150 geraden AS 500 Flachbohlen und 4 Abzweigbohlen besteht, hat einen Durchmesser von 24,7 m. Jeder der sechs Bögen besteht abwechselnd aus 14 normalen AS 500 Bohlen und 12 geknickten Bohlen. Secometal, ein Subunternehmer von ArcelorMittal, stellte die geknickten Bohlen her. Alle AS 500 Spundbohlen sind 26,7 m lang und 12,7 mm dick. Die Bohlen haben eine garantierte Mindestschlossfestigkeit von 5.500 kN pro laufendem Meter Schloss. Skyline Canada lieferte außerdem 19 Ersatzbohlen, darunter Einzel-, geknickte und Abzweigbohlen. Die neue Kaianlage wurde 2006 von den Consulting Engineers of British Columbia mit einem Award of Engineering Excellence ausgezeichnet.
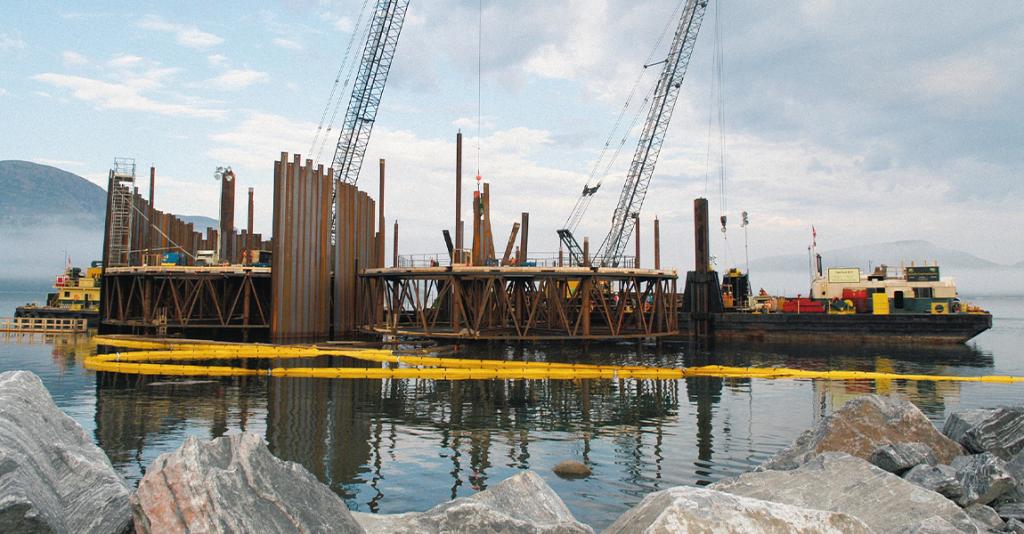
Allgemeine Einbringverfahren für AS 500 Zellen
Hamburg | Deutschland
> Erweiterungsprojekt Predöhlkai – Liegeplatz 1
Als einer der wichtigsten Häfen der Welt plant Hamburg, bis 2010 voraussichtlich 14 Mio. TEU umzuschlagen. Dies bedeutet eine erhebliche Steigerung gegenüber der heutigen Containerumschlagskapazität von 8,5 Mio. TEU. Der europäische Megahafen sah sich mit einem jährlichen Anstieg des Containeraufkommens um 15 % und einem Wachstum des Gesamtgüterumschlags um fast 10 % konfrontiert. Daher wurde beschlossen, die Investitionsmittel für die Erweiterung der folgenden vier Anlagen auf rund 1.000 Mio. Euro zu erhöhen.
Containerterminal Burchardkai:
Derzeitige Kailänge: 2.850 m. Derzeitige Kaitiefe: 16,5 m.
Erhöhung der Kapazität von 2,6 Mio. TEU auf 5 Mio. TEU durch Flächenumbau und Modernisierung des Lagersystems.
Containerterminal Altenwerder:
Derzeitige Kailänge: 1.400 m. Derzeitige Kaitiefe: 16,7 m.
Es war geplant, die Kapazität des neuen, mit Stahlspundbohlen gebauten Containerterminals von 1,9 auf 3 Mio. TEU zu erhöhen.
Tollerort Containerterminal:
Aktuelle Kailänge: 395 m.
Durch den Ausbau der Umschlagfläche wurde die Containerumschlagskapazität um 0,8 Mio. TEU erhöht und erreichte 2011 über 2 Mio. TEU.
Eurogate Containerterminal – Predöhlkai:
Aktuelle Kailänge: 2.100 m. Aktuelle Kaitiefe: 18,8 m.
Die Erweiterung des Liegeplatzes 1 wurde gerade abgeschlossen, der Ausbau der Liegeplätze 2 bis 3 ist in Arbeit. Das Ausbauprogramm sollte bis 2008 abgeschlossen sein und die Gesamtkailänge des Predöhlkais um 1.035 m erweitern.

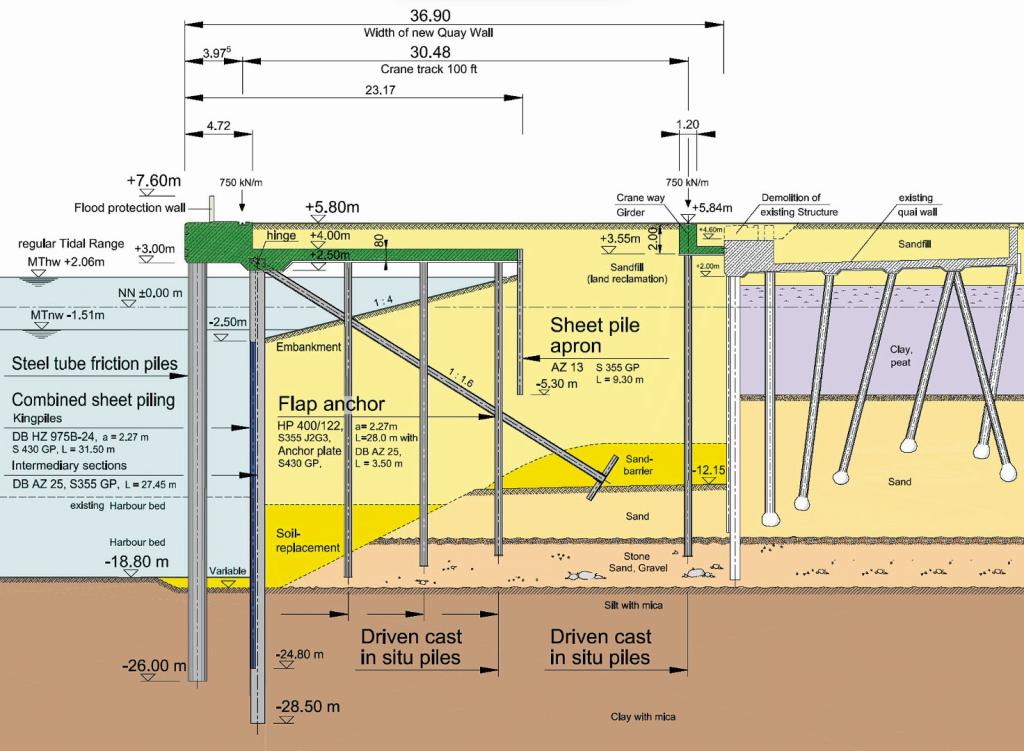
Es gab weitere Pläne für eine Erweiterung nach Westen in Richtung Elbe, um die Kapazität von 2,6 auf über 4 Mio. TEU bis 2010 zu erhöhen. Das Budget des Eurogate-Projekts beträgt 350 Mio. Euro.
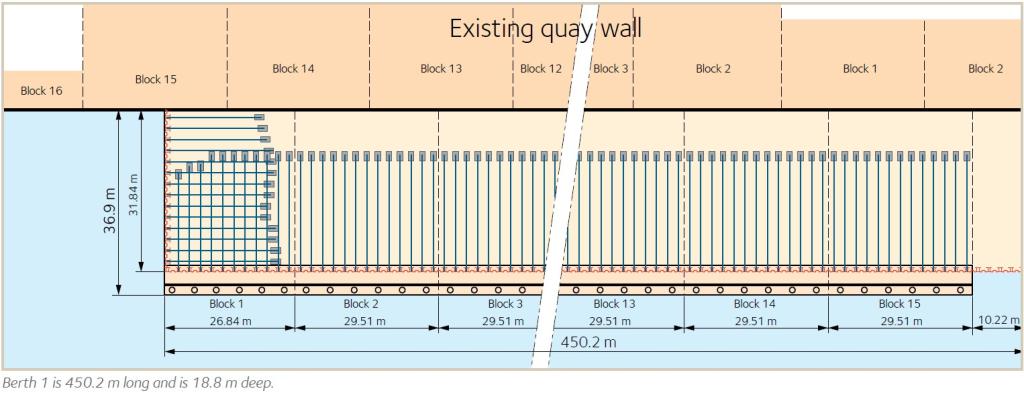
Der Eurogate-Terminal wurde im November 2005 offiziell wiedereröffnet, als der erste Teil des Modernisierungsprogramms nach einer Bauzeit von 18 Monaten abgeschlossen wurde. Der Terminal verfügt über einige der größten Containerkräne Europas und ist nun bereit, die größten Containerschiffe der Welt aufzunehmen. Die Modernisierung des 450 m langen Liegeplatzes 1 umfasste den Bau einer neuen 24,6 m hohen Kaimauer, die 37 m vor die bestehende Kaimauer gesetzt wurde. Der Bau der Spundwand wurde in 29,51 m lange Abschnitte unterteilt. Der erste Bauteil am östlichen Ende des Kais war 26,84 m lang und schloss rechtwinklig an die alte Konstruktion an. Das westliche Ende des Kais ist vorübergehend mit dem Liegeplatz 2 verbunden, der derzeit ausgebaut wird. Für die temporäre Wand wurde eine kombinierte Spundwandlösung verwendet.
Sowohl die HZ-Tragbohlen als auch die AZ-Zwischenbohlen wurden am Fußende verstärkt, um dem harten Boden gerecht zu werden. Die Stege der Doppeltragbohlen HZ 975 wurden mit 15 mm starken Verstärkungsplatten und einem konkaven Ausschnitt versehen. Die gestuften Ausschnitte der Flansche verringerten den Einbringwiderstand zusätzlich. Beide Seiten der Doppelbohlen AZ 25 wurden mit 15 mm dicken Stahlplatten verstärkt. Sie wurden bis zu einer Tiefe von 24,8 m zwischen den zuvor eingebrachten HZ-Tragbohlen gerammt. Aufgrund der schwierigen Einbringbedingungen wurde beschlossen, den Boden durch Vorbohren zu lockern, um das Einbringen der leichteren Zwischenprofile zu erleichtern. Die AZ-Spundbohlen wurden mit einem Vibrationshammer bis zum Einbringwiderstand eingebracht und anschließend mit einer Schlagramme bis zur geplanten Tiefe eingetrieben. Der obere Teil jeder zweiten AZ-Zwischenbohle wurde abgeschnitten, damit sich durch die natürliche Erosion des Bodens unter dem Überbau eine Wellenkammer bilden konnte. Die oberen 2,5 m der Schlösser der betroffenen AZ-Bohlen wurden im Werk abgeschnitten. Dadurch konnte das Schneiden mit dem Schweißbrenner auf der Baustelle auf ein Minimum reduziert werden.
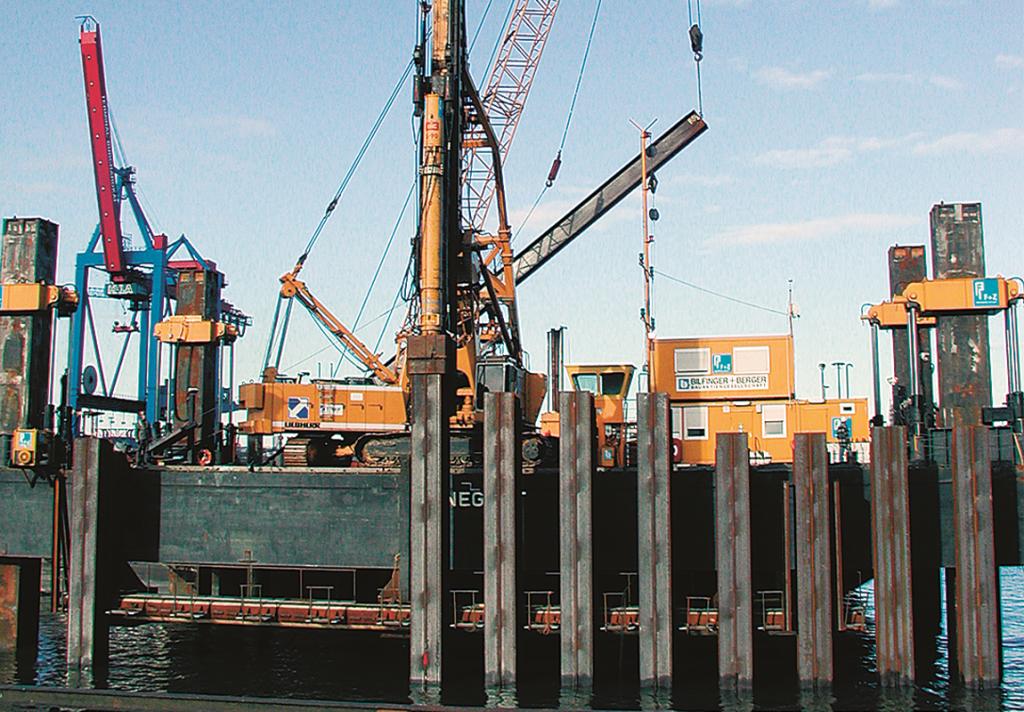
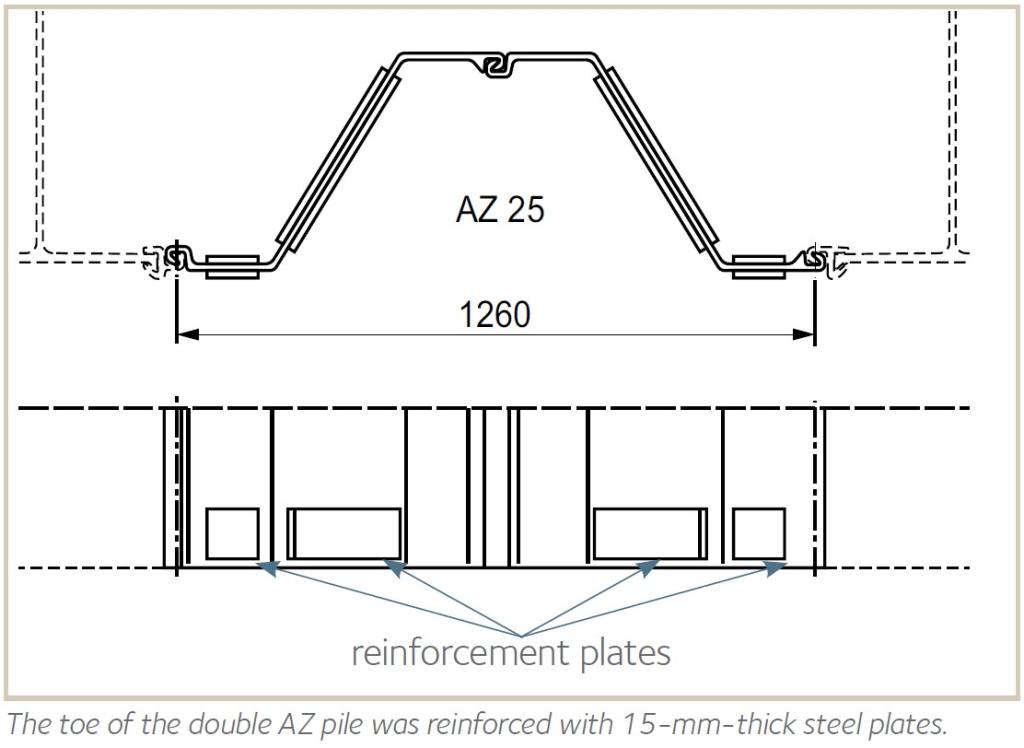
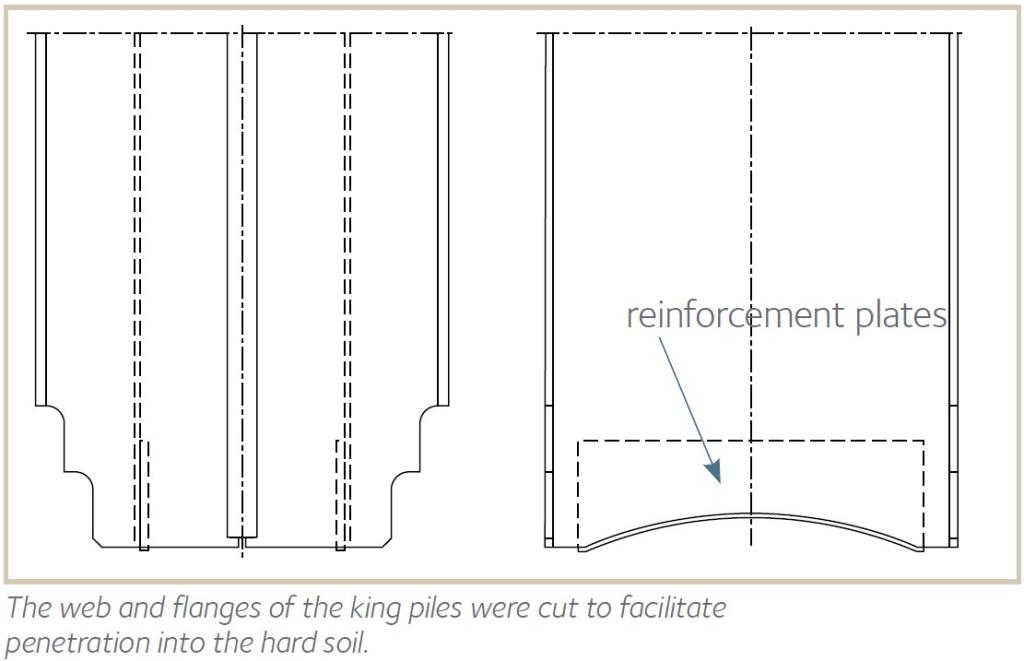
Das geniale Ankersystem des Predöhlkais besteht aus drehbar gelagerten 28 bis 34 Meter langen HP Pfählen, die an kurzen AZ-Doppelbohlen befestigt sind. Dieses System ist nicht nur in der Lage, hohe Zugkräfte aufzunehmen, sondern es kann auch dort eingebaut werden, wo sehr schwierige Einbringbedingungen zu erwarten sind. Die vormontierten Anker, bestehend aus HP 400/122 Pfählen (Stahlgüte S 355 J2G3) und ausgesteiften AZ 25 Doppelbohlen (Stahlgüte S 430 GP), wurden per Lastkahn zur Baustelle geliefert. Ein Kran hob den Anker in eine horizontale Position hinter der Kaimauer. Das drehbar gelagerte System wurde mit einer Gelenkverbindung an der Wand befestigt. Der Vibrationshammer wurde an den Ankerpfählen befestigt, bevor das System auf den Hafengrund abgesenkt wurde. Sobald der Anker einen Winkel von 32° erreicht hatte, wurde der Vibrationshammer eingeschaltet, um die Spundbohle in den Boden zu treiben, damit sie sich während der Wiederverfüllung nicht bewegt.
Um die Einbringung der Anker zu erleichtern und ein Verklemmen des Vibrationshammers zu verhindern, wurde die Oberseite der AZ-Bohlen mit zwei Schlitzen versehen. Das geneigte Ankersystem funktionierte sogar in der östlichen Ecke der Kaimauer perfekt, wo sich die Anker der Haupt- und der Seitenwand kreuzten.
Um Kolkprobleme durch Schiffsschrauben zu minimieren, wurden Stahlrohre mit einem Durchmesser von 1.220 mm vor die Kaimauer gesetzt. Der gesamte Bereich hinter der neuen Kaimauer wurde in späteren Bauphasen mit Sand verfüllt. Der von Baggern angelieferte Flusssand aus der Elbe wurde hinter der Ankerwand aufgeschüttet, um das Ankersystem zu sichern und die Betonarbeiten auf der Oberseite der Kaimauer im Trockenen durchführen zu können.
Die Vertikallasten des Liegeplatzes 1 am Predöhlkai werden zum Teil von Stahlsystemen – Rohren und Spundwänden – und zum Teil von Betonpfählen im hinteren Teil des Kais getragen. Drei Reihen von Betonpfählen mit einem Durchmesser von 510 mm nehmen die Lasten des Betonüberbaus auf. Der Überbau erfüllt eine lastabtragende Funktion und ermöglicht eine wirtschaftliche Gestaltung der vorderen Spundwand. Am hinteren Ende des Betonüberbaus wurden Spundbohlen AZ 13-10/10 in der Stahlgüte S 355 GP auf -5,3 m gerammt. Diese Spundbohlen haben eine bodenstützende Funktion. Eine Reihe von Betonpfählen trägt die Lasten der hinteren Kranschiene, die sich direkt vor der ehemaligen Kaimauer befindet.
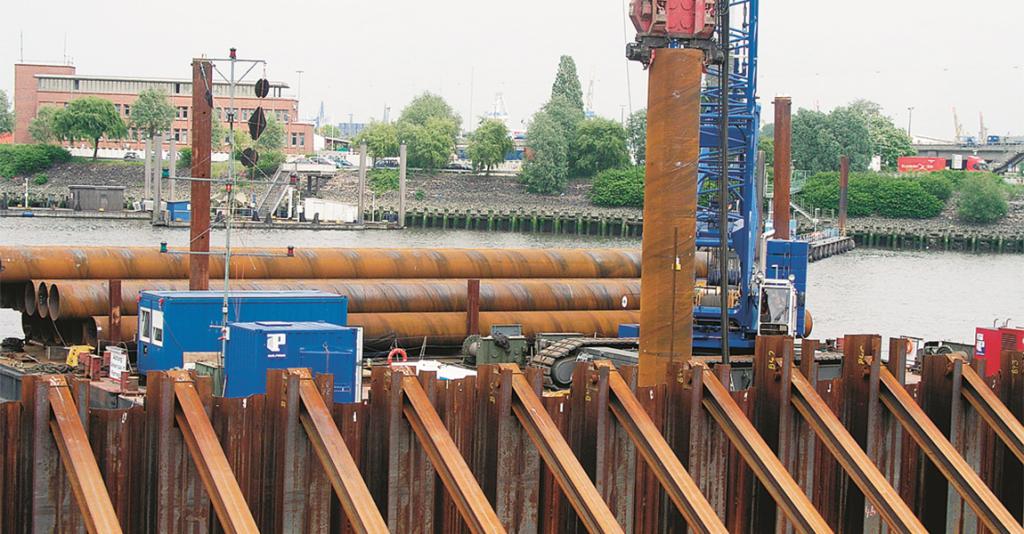
Überblick: Bauphasen 1 bis 8 für Liegeplatz 1
La Spezia | Italien
> Hafenausbauprojekte
Die Stadt La Spezia liegt etwa auf halber Strecke zwischen Genua und Pisa, dem Teil des Landes mit der größten Konzentration von Häfen. Zu diesen Häfen gehören die Häfen von Genua, Savona, Livorno und La Spezia, die zusammen eine jährliche Frachtumschlagskapazität von mehr als 100 Mio. Tonnen haben. Von hier aus exportiert der industrielle Norden Italiens seine Produkte.
Die Ursprünge der Kais Malaspina und Garibaldi gehen auf das Ende des 19. Jahrhunderts zurück. Die Kaianlagen des Hafens haben während des Zweiten Weltkriegs erheblich gelitten. Die Hafenbehörde von La Spezia musste daher erhebliche Investitionen tätigen, um die beschädigten Bauwerke wieder aufzubauen.
Heute bietet der Hafen eine kombinierte Kailänge von 5.300 m mit einem Tiefgang von bis zu 14,5 m, um Containerschiffe der neuesten Generation aufzunehmen. Die verschiedenen Terminals in La Spezia schlagen alle Arten von Produkten um: Container, Kohle, Öl, Zement, Getreide, Lebensmittelöle usw. Die Containerkais des Hafens verfügen über eine Anlegelänge von insgesamt 1.500 m. Die Gottwald-Kräne mit ihrer 100-Tonnen-Hubkraft bedienen die 260.000 m² großen Containerplätze.
Nach einer Studie, die einen Anstieg des Frachtverkehrs über die derzeitigen Kapazitäten hinaus vorhersagte, wurde 1995 ein Modernisierungsprogramm mit dem Ziel der Erweiterung der Terminals Ravano, Malaspina und Garibaldi eingeleitet. Im Jahr 2004 wurden im Hafen von La Spezia etwas mehr als 1 Mio. TEU umgeschlagen, was einem Anstieg von 3,4 % gegenüber dem Vorjahr entspricht. Im Rahmen des Modernisierungsprogramms wurden insgesamt 27.500 t Spundbohlen in den folgenden Bereichen des Hafens eingebracht:
1. GARIBALDI PIER: 9.000 t HZ/AZ kombinierte Spundwand
Die Effektivität des Piers wird durch drei Anlegestellen mit einer Gesamtlänge von 510 m auf der Westseite und zwei Anlegestellen mit einer Länge von 360 m auf der Ostseite gewährleistet. Der Garibaldi Pier bietet einen Tiefgang von bis zu zwölf Metern. Der Kranpark ist die größte Anlegestelle im Hafen von La Spezia und umfasst mehrere Kaikräne mit einer Kapazität von 12 t sowie vier mobile 100-t-Kräne. Zusammen mit den großen Getreide- und Zementsilos werden auf der 4.300 m² großen überdachten Lagerfläche verschiedene Güter wie Forstprodukte, Kohle, Eisen- und Stahlprodukte umgeschlagen.
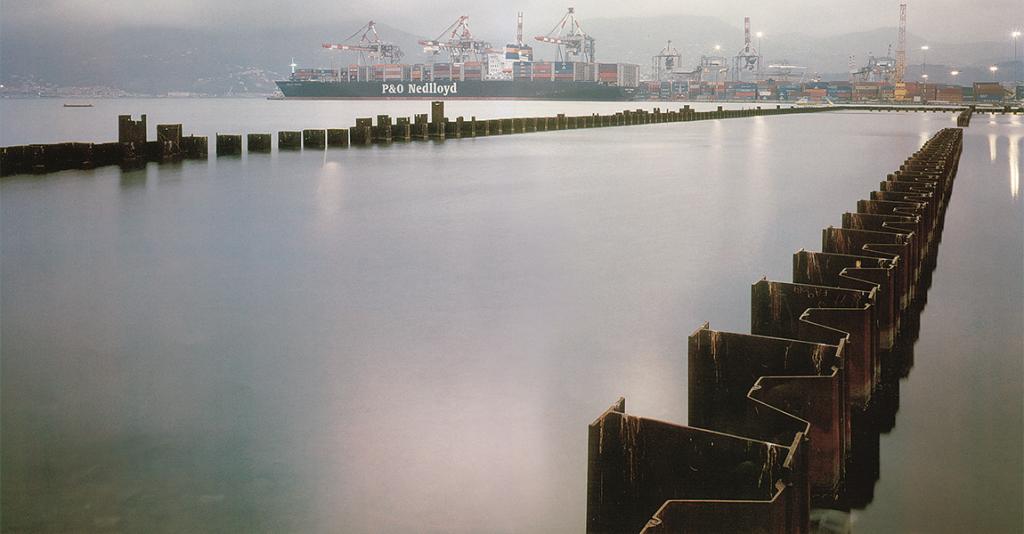
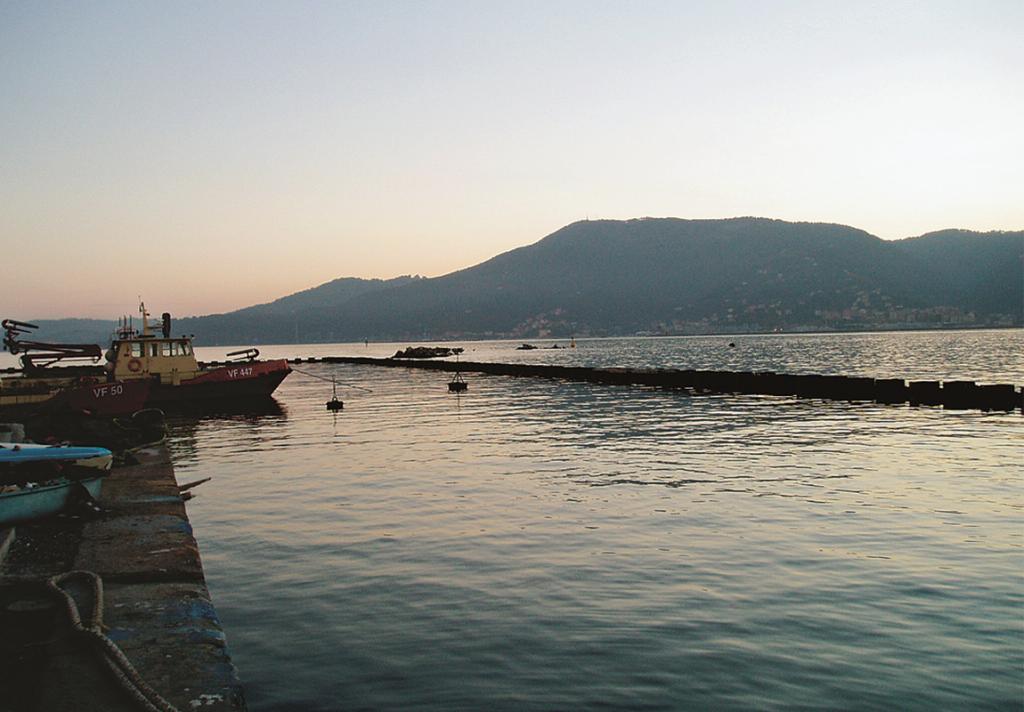
Der Tiefgang von 12 m wurde erreicht, indem eine neue Kaimauer aus Spundbohlen 40 m vor die bestehende Schwergewichtswand gesetzt wurde. Die kombinierte Stahlspundwand ist U-förmig und besteht somit aus drei Teilen.
Für den ersten küstennahen Teil wurde als Ankerwand ein System HZ 975 C - 12/ AZ 18 mit einem elastischen Widerstandsmoment von 7.360 cm³/m gewählt. Die HZ-Tragbohlen und die AZ-Zwischenbohlen wurden in Längen von 24 m und 18 m geliefert.

Nach dem Einbringen der Stahlspundbohlen musste in der nächsten Bauphase der Bereich zwischen neuen und bestehenden Kaimauern verfüllt werden. Entlang der Rückwand musste das Verfüllmaterial vom Hafengrund bis zu einem Punkt ansteigen, der mit der Oberkante der zuvor errichteten Ankerwand übereinstimmte. Näher an der Ankerwand brachte der Bagger das Verfüllmaterial nur bis zur Hälfte der Oberkante der kombinierten Spundwand ein. Dadurch wurden die Kräfte und Verformungen der kombinierten Spundwand minimiert, die vor dem Einbau des Ankersystems als freitragende Wand fungierte.
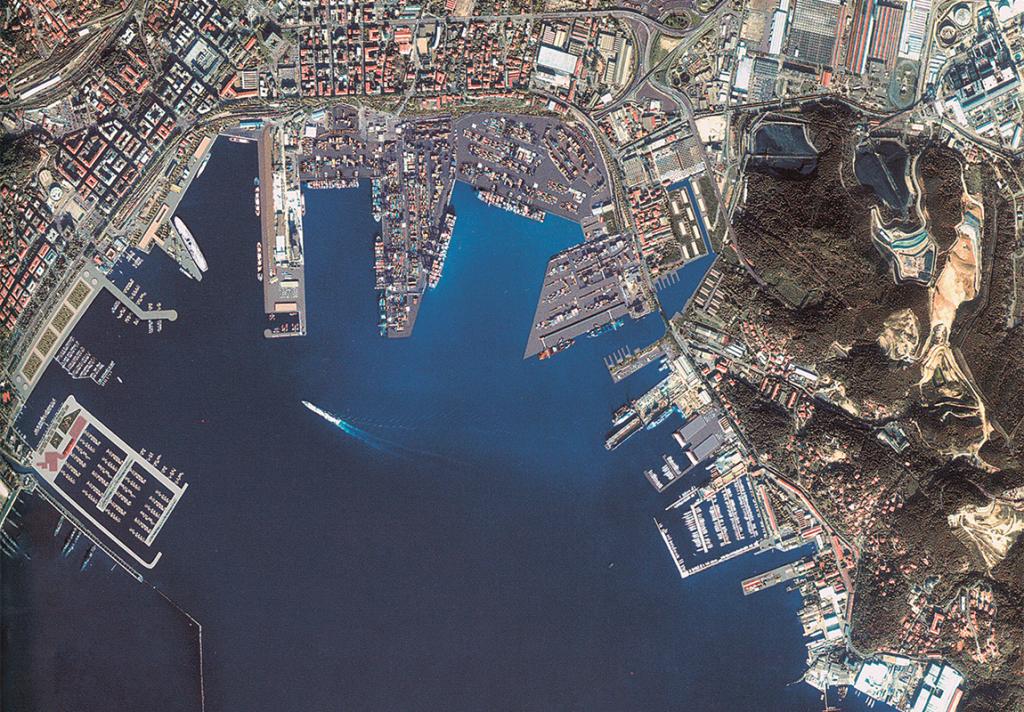
In der folgenden Bauphase wurden die 8 m langen AZ 26 Spundbohlen eingebracht, die die hintere Ankerwand bilden. Alle für das Garibaldi-Pier-Projekt verwendeten Spundbohlen sind aus hochfestem Stahl (S 390 GP) gefertigt. Als Nächstes wurden die gestauchten Anker von Anker Schroeder aus Dortmund, Deutschland, eingebaut. Die Anker haben ein Gewinde von 3,75", einen Durchmesser von 75 mm, eine Länge von 25 m und sind alle 1,79 m an einem Ende mit dem HZ-Träger und am anderen Ende mit einem UPN 400 Gurt verbunden. Sie waren für eine Arbeitslast von 839 kN ausgelegt.
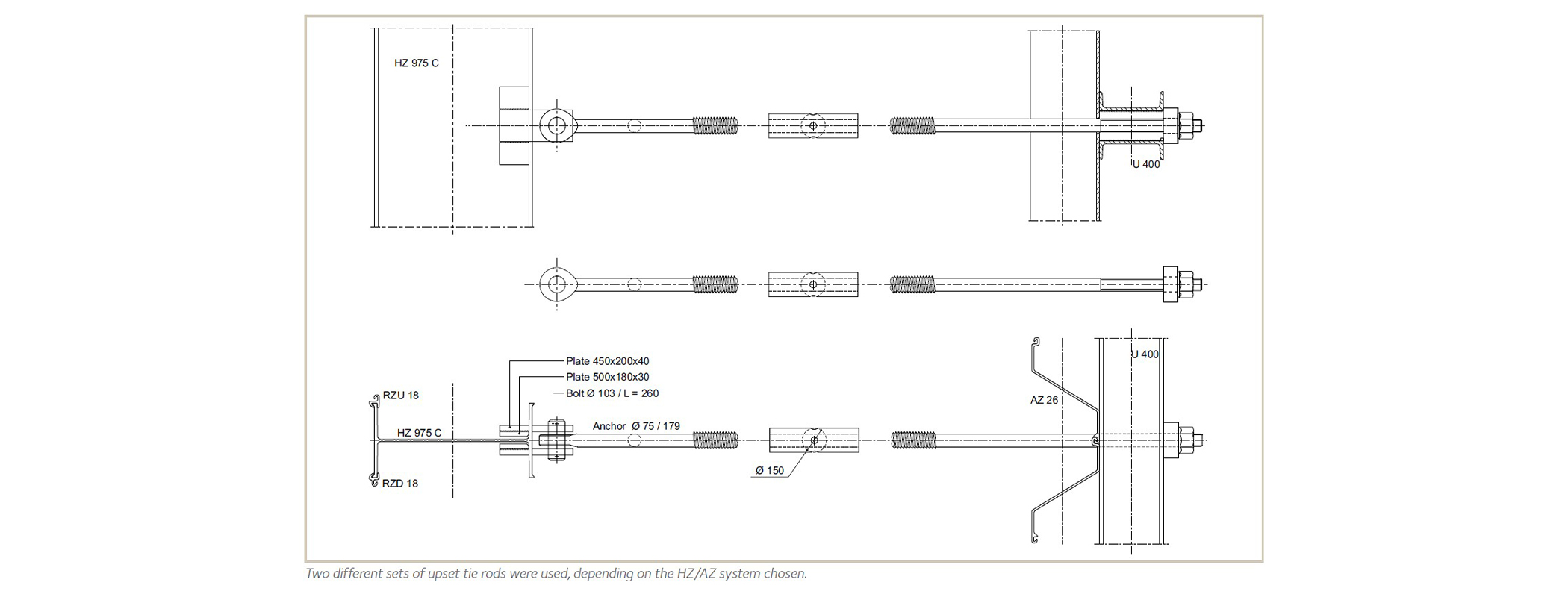
2. MALASPINA KAI: 1.800 t HZ/AZ kombinierte Spundwand
Die 200 m lange Mehrzweck-Kaianlage mit einer Tiefe von zehn Metern ist mit vier Kränen ausgestattet und wird für die Abfertigung von RoRo-Schiffen genutzt. Die von der Compagnia Lavoratori Portuali verwaltete Kaianlage verfügt über eine Lagerfläche von 2.500 m².
3. RAVANO PIER: 4.000 t HZ/AZ kombinierte Spundwand
Dieser Containerterminal wird von La Spezia Container Terminal (Contship Italy Group) und Terrestre Marittima betrieben. Der Terminal verfügt über eine 300 m lange Anlegelinie, eine Tiefe von 11 m, drei Gleisanlagen und einen 40.000 m² großen Lagerplatz.
4. CANTIERI DEL GOLFO TERMINAL: 4.000 t HZ/AZ kombinierte Spundwand
TARROS KAI: 500 t HZ/AZ kombinierte Spundwand
Das 310 m lange Golfo-Terminal mit einer Tiefe von 12 m liegt in der Nähe des Ravano Kais und ist auf RoRo- und Containerschiffe spezialisiert. Das Tarros-Terminal dient der Abwicklung des Passagierverkehrs. Die Kais sind mit sieben RoRo-Liegeplätzen ausgestattet.
5. IMMA maritimer Standort: 500 t AZ-Spundbohlen
6. PORTO LOTTI Marina: 3.500 t AZ-Spundbohlen
7. FERRARI maritime Baustelle: 250 t AZ Spundbohlen
8. FINCANTIERI: 600 t AZ-Spundbohlen
9. VALDEMARO maritime Baustelle: 250 t AZ Spundbohlen
10. GRAZIE Kai: 500 t AZ-Spundbohlen
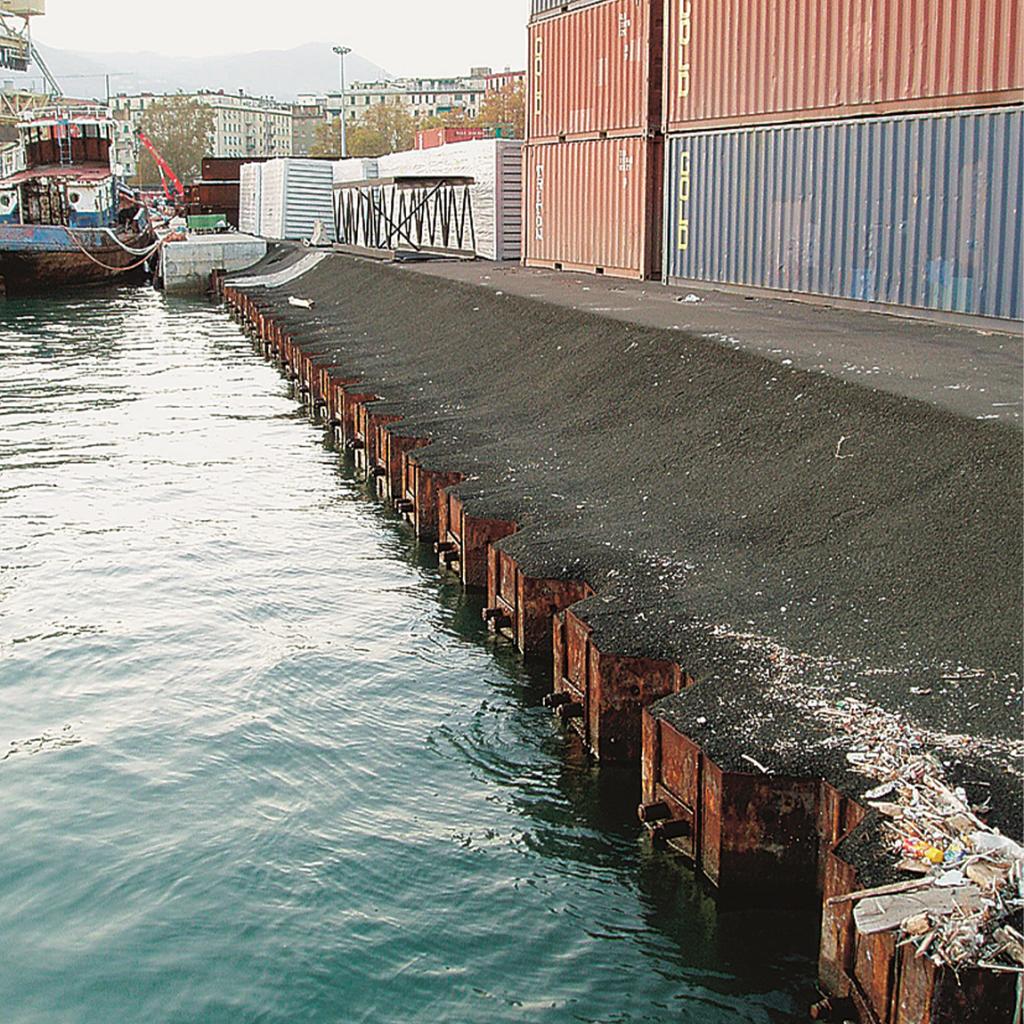
11. FERRETTI Kai: 2.600 t AZ-Spundbohlen
Die Ferretti-Gruppe ist weltweit führend im Design und Bau von Luxus-Motoryachten und Sportbooten. Die Gruppe hat 26 Mio. Euro in den Bau einer Werft für das nördliche Tyrrhenische Meer mit Sitz im Hafen von La Spezia investiert. Die Arbeiten an der neuen Werft begannen im Mai 2003 und sollen im Jahr 2006 abgeschlossen werden. Mehrere bestehende Gebäude wurden abgerissen, um Platz für neue Hangars, Büros und einen 400 m langen Pier zu schaffen. Die 15.000 m² große Bootswerft im östlichen Teil des Hafens ist derzeit in Betrieb. Die neue Bootswerft wurde mit Z-Spundbohlen in der Stahlgüte S 390 GP gebaut. Die Hauptwand besteht aus AZ 36 Bohlen, deren Länge zwischen 19 und 24 m liegt.
Als Ankerwand wurden AZ 18 Bohlen mit einer Länge von acht Metern eingebracht. Zum Einbringen der Spundbohlen wurde ein PTC-Vibrationshammer in Kombination mit einem Führungsgestell verwendet. Die 21 Ecken des komplexen Kais bestehen aus C9-, C14- und Omega-18-Schlossprofilen, die an Spezialbohlen geschweißt sind. Einige der Kaimauern sind 92 m lang, während andere nur 7,5 m lang sind.
Alle Doppelbohlen AZ 36 und AZ 18, einschließlich der Spezialbohlen für die Ecken, wurden per Zug vom Werk in Luxemburg zum Hafen von La Spezia geliefert. Für den Ferretti Kai wurde eine Dichtungsmaßnahme angewandt. Das angewandte Roxan-System besteht aus einem wasserquellenden Produkt, das in einem Werk in Luxemburg in die Schlösser der Bohlen eingebracht wird. Das Roxan-System auf Urethan-Prepolymer-Basis ist extrem haltbar und kann einem Wasserdruck von bis zu 25 m standhalten.
Beim Einbringen von Spundbohlen mit dem Roxan-Abdichtungsprodukt muss der Bauunternehmer darauf achten, dass das System vor dem Einbringen nicht aufquillt. Der Kontakt von mit Roxan gefüllten Schlössern mit Wasser muss während des Transports und der Lagerung vermieden werden. Durch die Verlegung des behandelten Schlosses nach unten wird ein unerwünschtes Aufquellen in der Regel vermieden.
Beim Einbringen der Bohle mit dem Abdichtungsprodukt im vorderen Schloss sollte das Einbringen nicht länger als zwei Stunden unterbrochen werden. Andernfalls kann das sich ausdehnende Abdichtungsmaterial bei der Wiederaufnahme des Einbringens abgerissen werden.
Mersin | Türkei
> Hafenerweiterungsprojekt
Mersin liegt am Mittelmeer, an der Südostküste der Türkei. Mehrere internationale Bauunternehmen wurden aufgefordert, ein Angebot für die Modernisierung des Mersin-Entladehafens abzugeben. Einsendeschluss für die Ausschreibung war September 2002. Das gesamte Projekt wurde Ende 2005 nach einer Bauzeit von zwei Jahren abgeschlossen. Um das Anlegen großer Schiffe und die Installation neuer Containerkräne zu ermöglichen, wurden sowohl der bestehende Kai aus schweren Unterwasserbetonblöcken als auch der Rangierbereich modernisiert. Die Wassertiefe wurde auf zwölf Meter verdoppelt. Eine Stahlspundwand mit einer Gesamtlänge von 624 m wurde 12,2 m vor der bestehenden Kaianlage errichtet. Der Bereich zwischen dem alten und dem neuen Teil der Kaianlage wurde mit Felsen verfüllt. Die Stahlspundbohlen wurden in Lehmboden gerammt, der sich durch Kohäsionswerte zwischen 5 und 10 kN/m² auszeichnet.
Die Entscheidung für eine Stahllösung als Ersatz für die bestehende Betonlösung fiel unter anderem deshalb, weil das Projekt in einer erdbebengefährdeten Region errichtet wurde. Stahl bietet als duktiles Material höhere Lastreserven bei Erdbeben.
Kauf und Einbringen der Stahlspundbohlen machen etwa 15 % der gesamten Projektkosten aus. Das folgende Material wurde benötigt (Ausschreibungsmengen):
- Wandfläche: 14.968 m²;
- Materialqualität: ASTM A690;
- Widerstandsmoment: 6.000 cm³/m;
- Dicke: 10 mm;
- Anstrich: 3 Schichten verstärkte Epoxidharzbeschichtung.
Das erforderliche Widerstandsmoment übersteigt die Kapazität von U- oder Z-Spundbohlen. Solche hochbelastbaren Kaimauern können mit einer kombinierten oder einer Jagged Wand gebaut werden. Für das aktuelle Projekt schlug ArcelorMittal eine Jagged Wand aus AU 20 Spundbohlen mit folgenden Eigenschaften vor:
- AU 20 Jagged Wand;
- Gewicht: 186,7 kg/m²;
- Materialqualität: ASTM A690, alternativ in S 355 GP;
- Widerstandsmoment: min. 6.365 cm³/m;
- Dicke: 10 mm;
- Gesamtmenge der Spundbohlen: 2.770 t.
Die AU 20 Stahlspundbohlen für das Projekt Mersin wurden in einer speziellen Anordnung, der so genannten Jagged Wand, eingebracht. Eine Anordnung von U-Spundbohlen zu einer Jagged Wand bietet wirtschaftliche Lösungen, wenn eine hohe Trägheit und ein hohes Widerstandsmoment erforderlich sind. Die AU 20 Elemente wurden im Werk verpresst und als Doppelelemente geliefert. Verpresste Doppelbohlen ermöglichen die volle Schubkraftübertragung in den auf der zentralen Wandachse liegenden „entscheidenden” Schlössern. Die Standardverpressung von AU-Spundbohlen besteht aus drei Presspunkten alle 0,75 m mit einer zulässigen Schubkraftübertragung von 75 kN pro Presspunkt. Die von ArcelorMittal durchgeführten Zugversuche haben gezeigt, dass jeder Verpresspunkt Lasten von bis zu 130 kN übertragen kann.
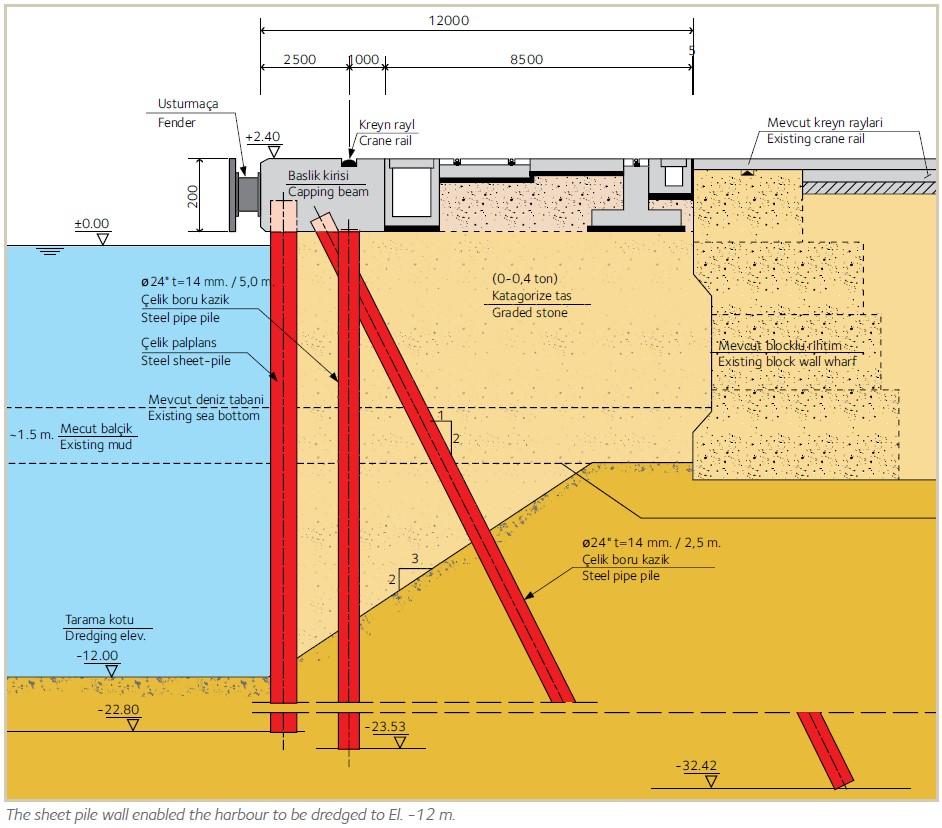
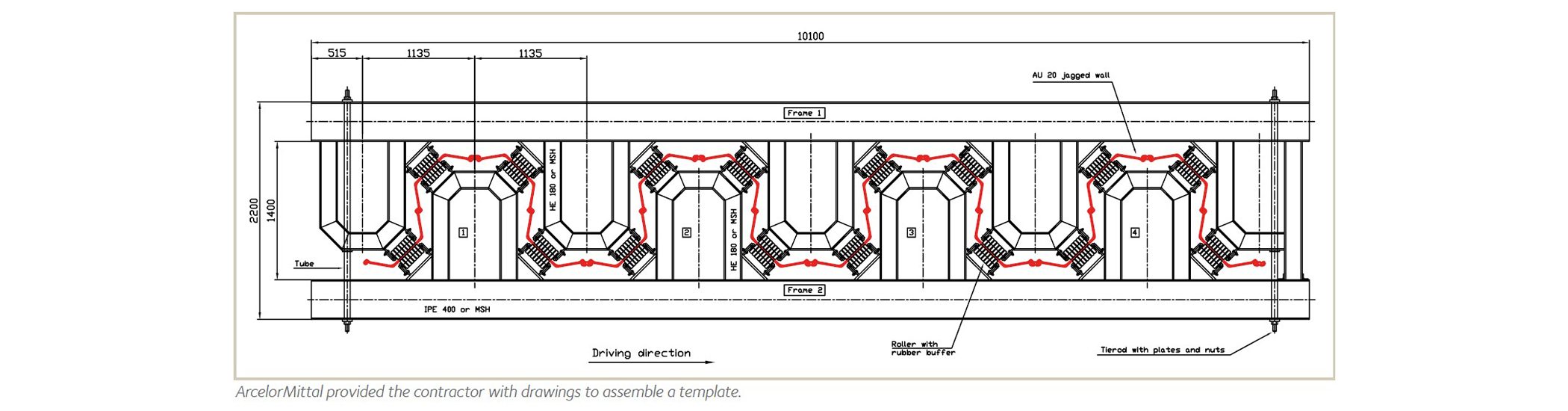
Für das Einbringen der Stahlspundbohlen und der 24-Zoll-Stahlrohre (61 cm) wurde ein speziell entwickeltes schienengebundenes Bohrsystem verwendet. Die vertikalen Bohlen wurden alle 5 m eingebracht und erreichten eine Tiefe von 23,53 m. Die geneigten Rammpfähle, die in Abständen von 2,5 m angeordnet waren, wurden bis zu einer Tiefe von 32,42 m gerammt.
Als Einbringgeräte wurden ein Vibrationshammer und eine Schlagramme eingesetzt. Die Einbringung erfolgte konventionell: Zunächst trieb der Vibrationshammer die Bohlen so weit wie möglich in den Boden ein, dann trieb der Schlaghammer die Stahlspundbohlen bis zur geplanten Tiefe von 22,8 m ein. Um die Vertikalität und die Ausrichtung der Spundbohlen zu gewährleisten, wurde das Verfahren des Einbringens von Platten angewandt. Durch das Einbringen einer Gruppe oder einer „Platte“ von Bohlen können einzelne Bohlen im Falle von Hindernissen im Boden oberhalb der geplanten Tiefe verbleiben, ohne dass die Einbringarbeiten unterbrochen werden müssen. Der Einbringwiderstand wurde durch das Erreichen eines Einbringfortschritts von nur 2 bis 3 mm pro Schlag definiert. Ein weiteres Einbringen mit dieser Eindringtiefe könnte zu Schäden an den Bohlen und der Rammausrüstung führen.
Es wurde ein japanischer TVM-50 Toyoda Vibrationshammer mit folgenden Eigenschaften verwendet:
- Gewicht: 3 t;
- Maximale Zentrifugalkraft: 420 kN;
- Maximales exzentrisches Moment: 205 Nm;
- Frequenz: 1.355 min -1.
Şener Arda standen auf der Baustelle zwei deutsche Dieselschlagrammen zur Verfügung: ein Delmag D30 und ein Delmag D46, die mit Rammen von 3.000 und 4.600 kg ausgestattet waren. Ihr maximaler Explosionsdruck liegt zwischen 1.050 und 1.650 kN, bei einer Schlagfrequenz von 37 bis 52 Schlägen pro Minute. Mit einem Gewicht von sechs Tonnen ist der Delmag D30 auf Bohlen bis zu acht Tonnen beschränkt, während der D46 Bohlen bis zu 15 Tonnen einbringen kann. Das optimale Gewicht des Einbringmaterials liegt bei der D30 zwischen zwei und neun Tonnen. Die erforderliche Rammhaube wurde dem Bauunternehmen als Teil der Dienstleistungen von ArcelorMittal für das Mersin-Projekt geliefert. Am hinteren Ende der Wand musste das Bauunternehmen das Einbringen vor Erreichen der Zieltiefe von 22,8 m abbrechen, da der steife Lehm den Einbringfortschritt unter die vorgegebene Grenze verlangsamte. Die Bemessung der Jagged Wand wurde überarbeitet, um der extrem steifen Bodenschicht Rechnung zu tragen. Untersuchungen ergaben, dass die Sohltiefe um bis zu 3 m reduziert werden konnte, da die unerwartet günstigen Bodenwerte am Ende des Ausbaus eine höhere Tragfähigkeit aufwiesen.
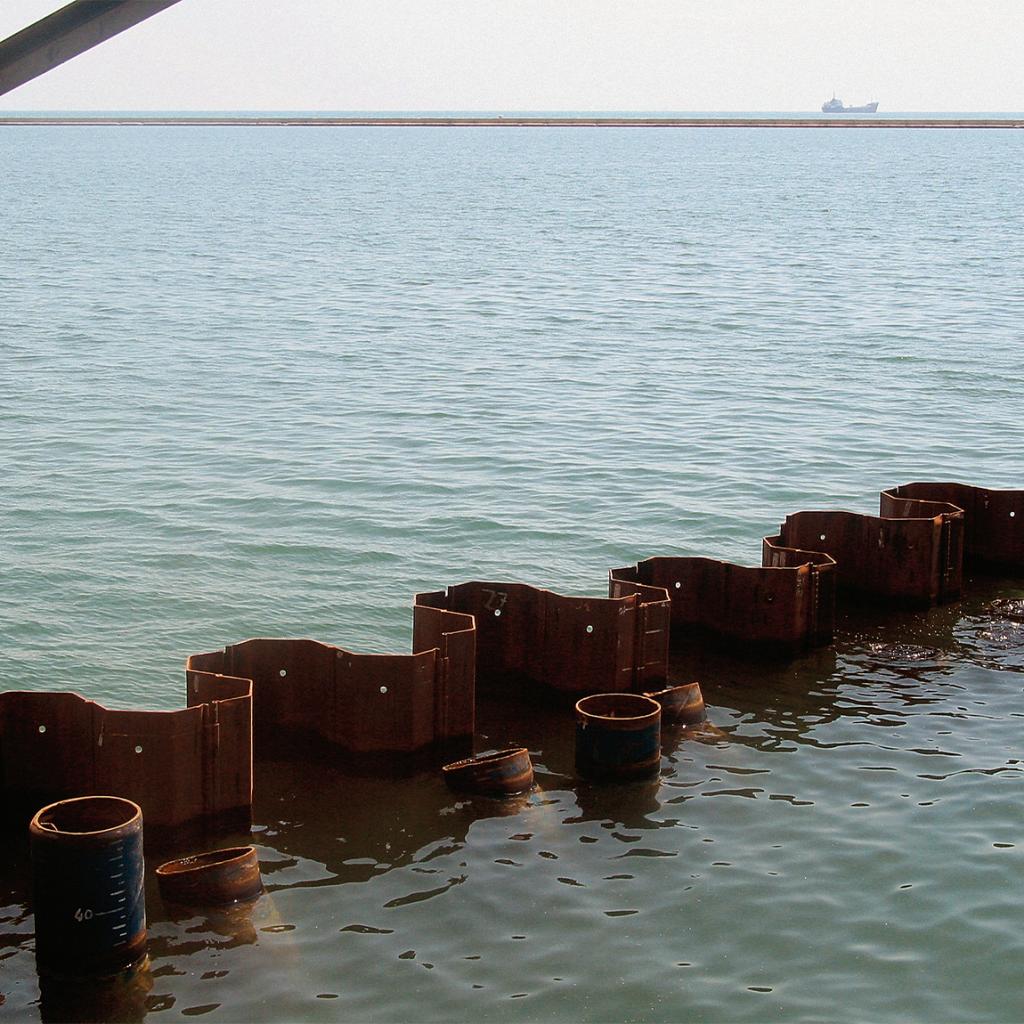
Marsden Point | Neuseeland
> Bau eines neuen Tiefseehafens
Marsden Point befindet sich an der Nordostküste der neuseeländischen Nordinsel. Hier wurde der modernste und tiefste Hafen des Landes gebaut. Der Hafen bietet einen ständigen Zugang für die Schifffahrt und garantiert einen kontinuierlichen Anstieg des Verkehrsaufkommens und ist damit zweifellos ein Schlüsselfaktor für die Entwicklung der neuseeländischen Wirtschaft.
Die Idee, in dieser Region einen neuen Hafen zu bauen, reicht mehrere Jahrzehnte zurück. Die Northland Port Corporation, die den nahe gelegenen Hafen von Whangarei betreibt, erwarb das Gelände in den 1960er Jahren, als die Forstwirtschaft in Neuseeland noch in den Kinderschuhen steckte. Im Laufe der Jahre erreichten rund 190.000 ha Kiefernwald ihren Reifegrad, was zu einem anhaltenden Wachstum der Exporte von Forstprodukten aus Whangarei führte. Für den Zeitraum 2000 bis 2004 wurde eine Vervierfachung der Exporte prognostiziert. Der Hafen von Whangarei, dessen Kaianlagen nicht für die heutigen schweren Umschlaggeräte ausgelegt sind, ist nicht in der Lage, dieses Wachstum zu bewältigen.
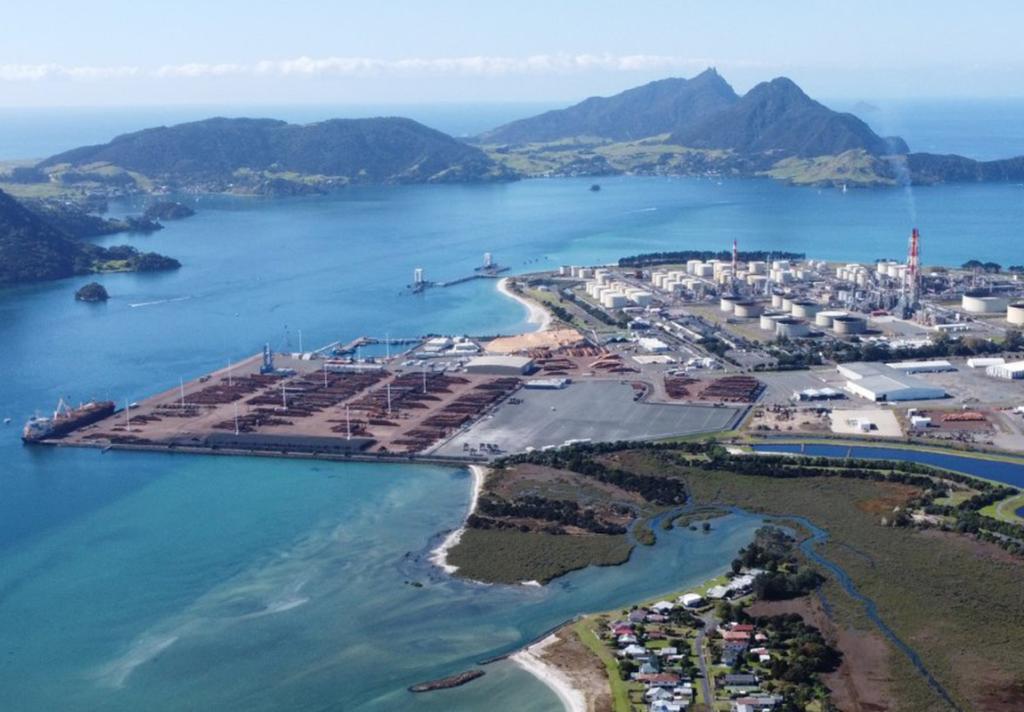
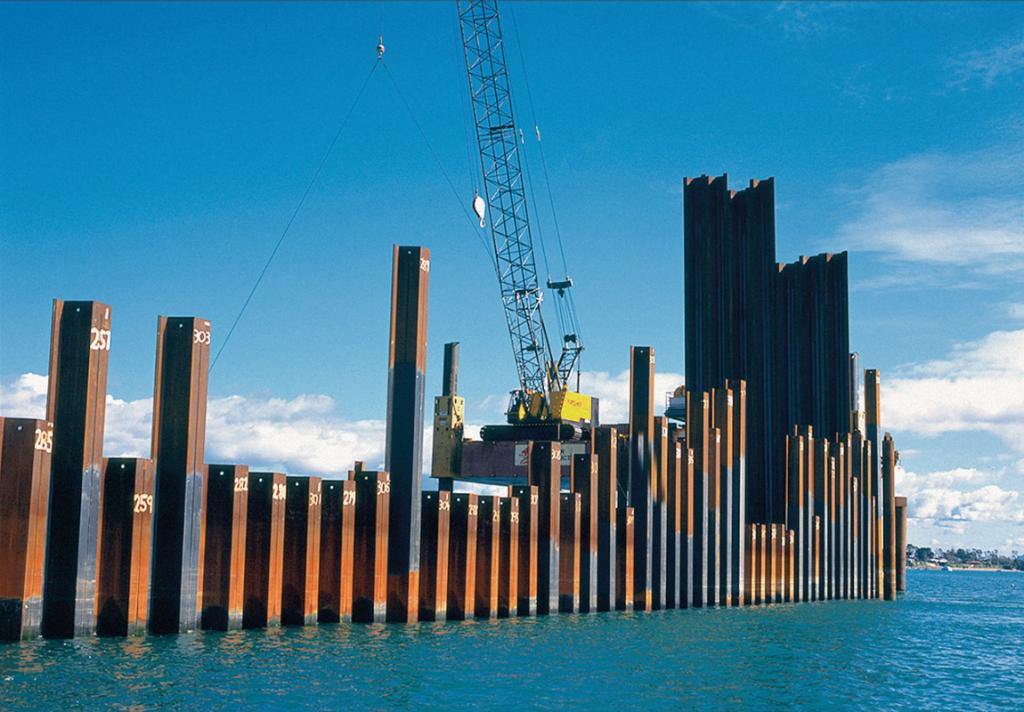
Northport, ein Joint Venture der Northland Port Corporation und des Hafens von Tauranga, hat sich mit Australasiens größtem Unternehmen für Forstprodukte, Carter Holt Harvey, zusammengetan, um den Landbetrieb im geplanten neuen Hafen durchzuführen. Nach dem nahe gelegenen Bau eines sehr großen Furnierschichtholzwerks, das hauptsächlich für den Exportmarkt bestimmt ist, verpflichtete sich Carter Holt Harvey, in den ersten fünf Betriebsjahren 1 Mio. Tonnen Holz und daraus hergestellte Produkte vom neuen Hafen aus zu versenden. Bald wurde eine wachsende Zahl anderer Exporte über den Hafen abgewickelt. Das jährliche Frachtvolumen erreichte 2005 2,8 Mio. Tonnen, darunter landwirtschaftliche Erzeugnisse, Düngemittel, Zement und Container sowie Holz.
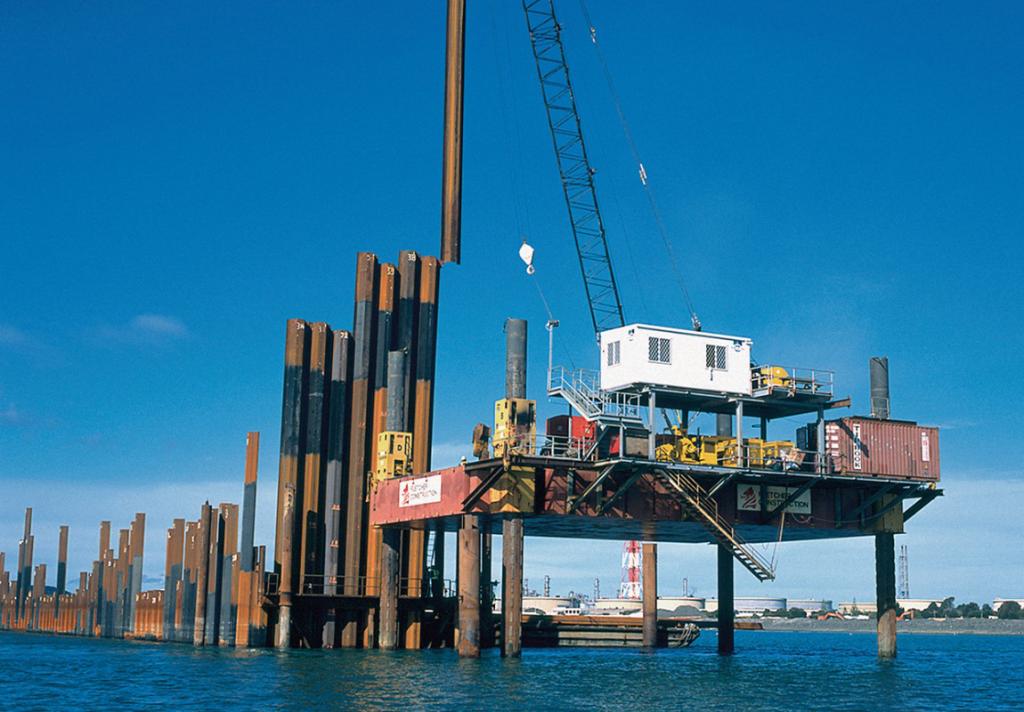
Bereits in den 1970er Jahren wurden gründliche Studien zu hydrografischen und ökologischen Aspekten des Standorts durchgeführt. Das Gebiet, in dem der neue Hafen gebaut wurde, liegt zwischen zwei inaktiven Verwerfungen; seine günstigen geologischen Bedingungen erleichterten die Bauarbeiten. Der Boden besteht aus Schwemmland, im Wesentlichen Sand, mit seltenen torfigen Bereichen, die alle über tiefem Grauwacke- und Argillit-Grundgestein liegen. Dies bedeutete nicht nur, dass die Rekultivierung ohne vorbereitende Baggerarbeiten durchgeführt werden konnte, sondern auch, dass das gebaggerte Erdreich aus dem Wendebecken als Verfüllmaterial verwendet werden konnte: mehrere Millionen Kubikmeter Sand wurden hinter einer 1.700 m hohen Böschung mit einer Höhe von 3 bis 16 m eingebaut. Die Böschung wurde ebenfalls aus leicht verfügbarem lokalem Material, hauptsächlich Sand, gebaut und durch schwere Felsen geschützt. Zur Verfestigung des Bauwerks wurde die Böschungsoberkante bis zu einer Höhe von zwei Metern mit Verfüllmaterial belastet, bevor sie für den Bau der Fahrbahn abgeflacht wurde.
Mit dem Bau des neuen Tiefwasserhafens wurde im Oktober 2000 begonnen. Weniger als zwei Jahre später, im Juni 2002, konnte das erste Schiff in Northport anlegen. Der zweite Liegeplatz wurde nur wenige Monate nach der Inbetriebnahme des ersten Liegeplatzes fertiggestellt. Das Projekt wurde im Rahmen eines Festpreisvertrags für Planung und Bau im Wert von 30 Mio. NZ$ gebaut. Der neue Hafen umfasst einen 50 ha großen Umschlagplatz (davon 32 ha auf aufgeschüttetem Land) und einen 390 m langen Kai mit zwei Anlegestellen, an denen Massengutfrachter mit einem Gewicht von 65.000 t, einer maximalen Länge von 230 m und einem maximalen Tiefgang von 13 m abgefertigt werden können. Die Fletcher Construction Company Ltd. war das Unternehmen für Planung und Bau des Hafens und Beca Carter Hollings and Ferner der Konstrukteur. Ursprünglich wurde für die Stützwand eine kombinierte HZ/AZ-Spundwand vorgeschlagen, um sowohl die angrenzende Rekultivierung zu begrenzen als auch die Rückseite des Kaidecks zu stützen. Das Deck besteht aus einer Ortbetonplatte, die auf der Seeseite von zwei Reihen betongefüllter Stahlspundbohlen getragen wird. Im endgültigen Entwurf von BCHF wurde die kombinierte Spundwand jedoch durch eine kostengünstigere AZ 36 Wand ersetzt. Der Entwurf berücksichtigt die hohen Lasten (Eigenlast von 85 kN/m, Nutzlast von 240 kN/m). Die beachtliche Breite der gewählten AZ-Bohlen (1,26 m pro Doppelbohle) ist ein Vorteil in Bezug auf die Produktivität der Konstruktion. Obwohl am anderen Ende der Welt hergestellt, wurden die 3.000 t Spundbohlen für das Northport-Projekt innerhalb von 3 Monaten an die Baustelle geliefert.
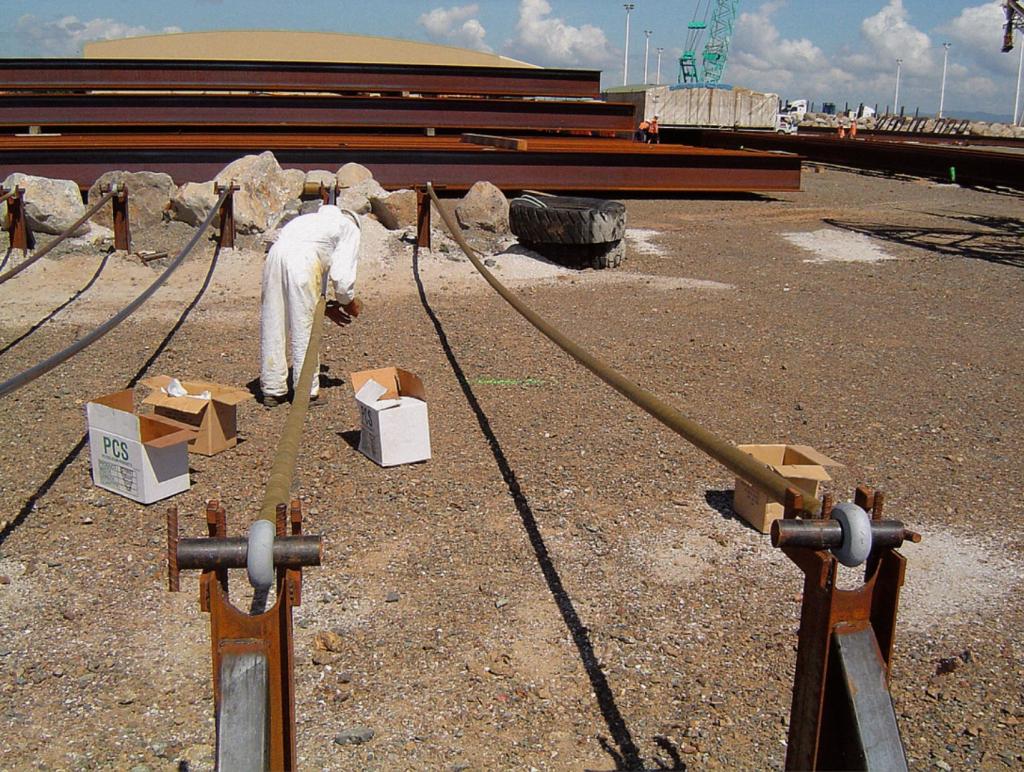
Ein Führungsrahmen mit zwei Stützebenen im Abstand von 8 m garantierte die erforderliche Ausrichtung. Das Führungsgestell wurde mit Stahlrohren fixiert, die mit demselben Rammgerät wie die Spundbohlen bis zum Einbringwiderstand gerammt wurden. Neun Paare von AZ 36 Bohlen wurden in den Führungsrahmen eingesetzt und in Platten gerammt, um die erforderliche Vertikalität zu gewährleisten. Die Spundbohlen AZ 26 des Totmannankers mussten nicht eingerammt werden: Sie wurden einfach von der Böschung aus aufgestellt und abgestützt, bis auf beiden Seiten genügend Sand vorhanden war.
Bei einer geplanten Lebensdauer von 50 Jahren wurde besonders darauf geachtet, dass die kritischsten Teile der Wand ausreichend vor Korrosion geschützt sind: die Gezeitenzone und die Oberkante der Unterwasserzone, die mit der Höhe der Anker zusammenfällt. Die Spundbohlen wurden mit zwei 175-µm-Schichten einer teerfreien Epoxidharzbeschichtung namens Altra Tar beschichtet. Nach der Montage wurden die Anker mit Denso Ultraflex-Korrosionsschutzband umwickelt und die Kupplungen mit Schrumpfschläuchen versehen.
Von Anfang an waren zwei weitere Liegeplätze mit einer Länge von 14,5 m geplant. Der Bau des Liegeplatzes Nr. 3 begann Ende 2005 unter Verwendung einer kombinierten Spundwandlösung von ArcelorMittal.
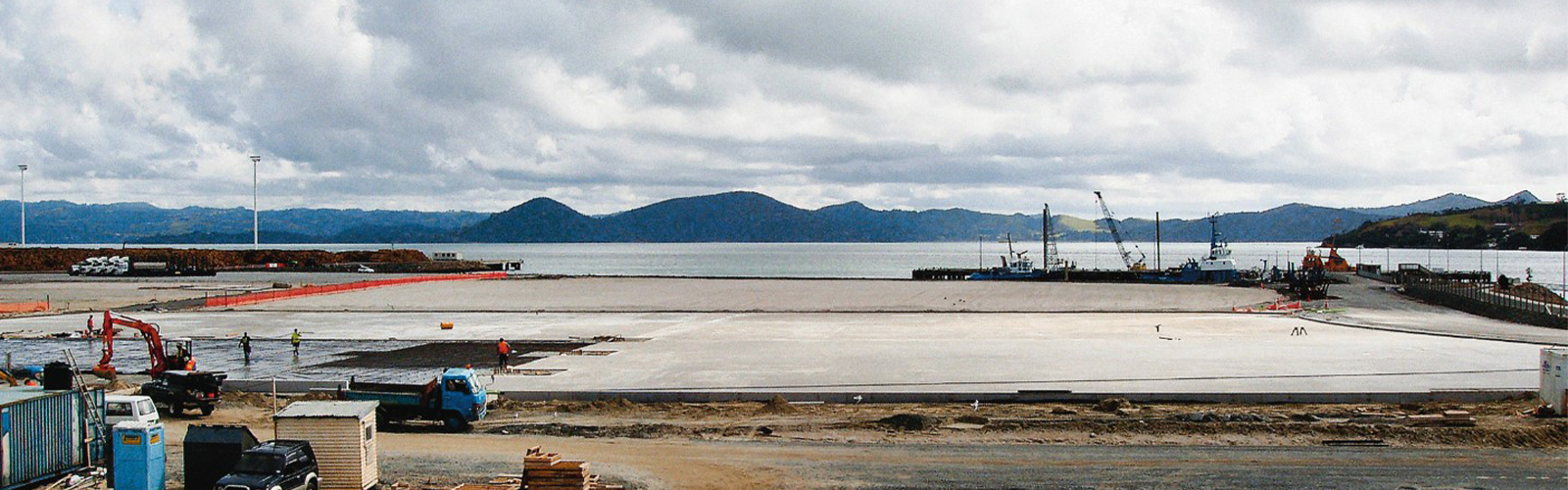